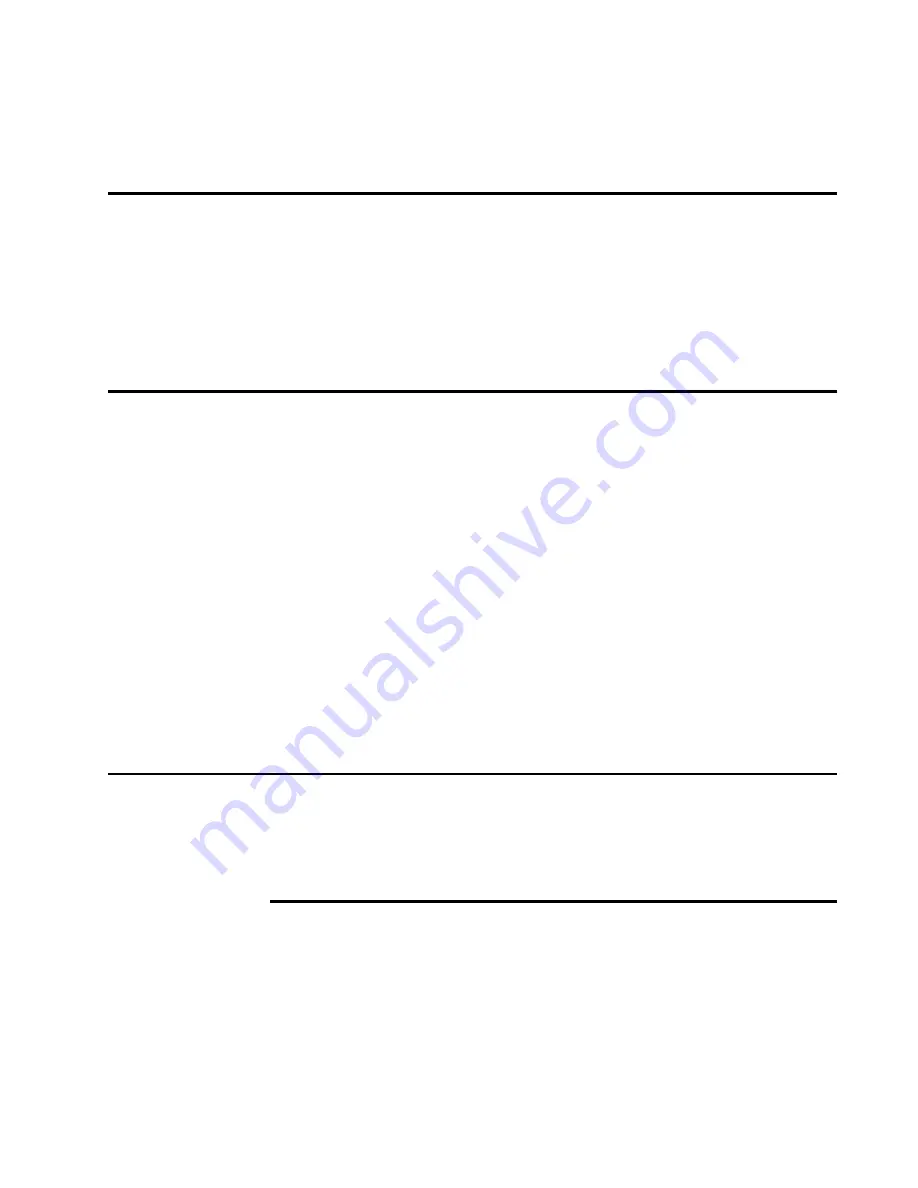
6-3
Chapter 6
Troubleshooting the Installation
This chapter provides information on cross-lane interference and
troubleshooting instructions for use when installing and testing the
IT2200 Reader System with Multimode Capability.
Required Equipment
You need the following equipment to complete the tuning procedure:
•
Hydraulic lift
•
Test computer (PC or lunch box type) with the IT2200 Engineering Host #11254-
00 software, Version 1.03 installed and an available ISA slot for installing a
reader logic card
•
Data cable to use as an extension cable to the installed data cable. Use a 2m (6-ft)
DB-25, fully wired, plug and socket end cable.
•
One pair of walkie talkie radios, preferably UHF band
•
Multimeter, Fluke 87 or equivalent
•
Vehicle. Use a car or truck for interior tags or a truck for exterior tags.
•
Commercial grade heat gun
Cross-Lane Interference in RFID Systems
As discussed in “Noise and Interference Immunity” on page 2-10, RFID systems are
subject to various types of interference that can affect the level of communications
between a tag and reader system. Another type of interference that can result from the
operation of the reader system is called cross-lane interference.
What Is Cross-Lane Interference?
Cross-lane interference occurs when the RF generated in one toll lane interrupts the
RFID operation in another lane thereby causing the affected lane to perform poorly.
Before diagnosing cross-lane interference, it is necessary to understand what consti-
tutes a satisfactorily performing lane.
Summary of Contents for Amtech IT2200
Page 1: ...IT2200ReaderSystem P N 411554 Installation Maintenance Service Guide withMultimodeCapability...
Page 2: ......
Page 5: ......
Page 6: ......
Page 7: ...Contents...
Page 8: ......
Page 19: ...1 Before You Begin...
Page 20: ......
Page 25: ...2 Theory of Operation...
Page 26: ......
Page 41: ...3 System Components...
Page 42: ......
Page 67: ...4 Installing the IT2200 Reader System...
Page 68: ......
Page 91: ...5 Tuning the Lane...
Page 92: ......
Page 109: ...6 Troubleshooting the Installation...
Page 110: ......
Page 129: ...7 Preventive Maintenance...
Page 130: ......
Page 133: ...A Acronyms and Glossary...
Page 134: ......
Page 142: ...IT2200 Reader System with Multimode Capability Installation Maintenance Service Guide A 10...
Page 143: ...B Block Diagrams...
Page 144: ......
Page 153: ...C System Technical Specifications...
Page 154: ......
Page 160: ...IT2200 Reader System with Multimode Capability Installation Maintenance Service Guide C 8...
Page 161: ...D Hardware Interfaces...
Page 162: ......
Page 185: ...E Connector Pin outs...
Page 186: ......
Page 204: ...IT2200 Reader System with Multimode Capability Installation Maintenance Service Guide E 20...