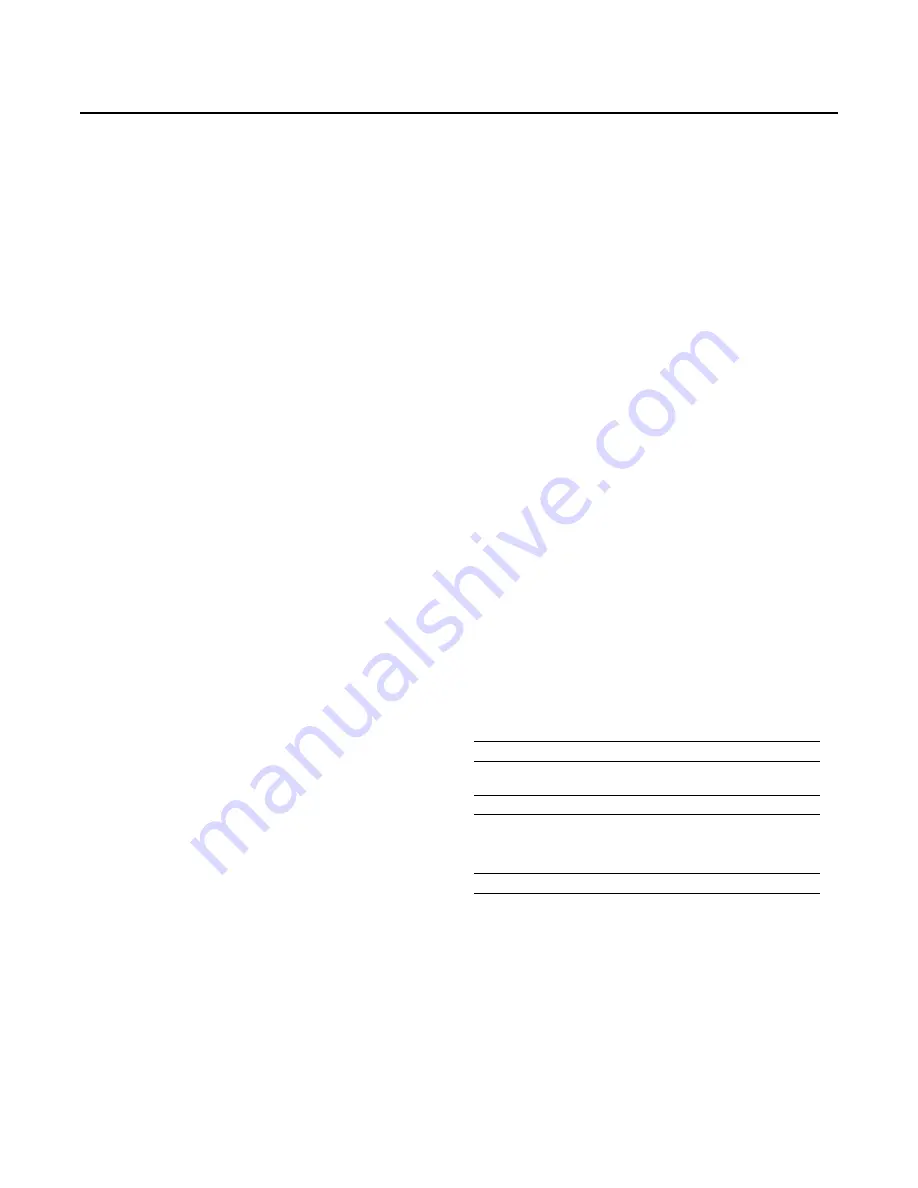
Sequence of Operation
RT-SVX26R-EN
49
If the unit has modulating heat, the unit can be made to do
discharge heating with VAV control. This is done by
placing a contact closure across the “Changeover Input”
on the RTAM. During this mode, the unit will heat to the
Supply Air Heating Se/- 3.5°F. During low load or
low airflow conditions the actual temperature swing of the
discharge air will likely be greater.
The RTRM utilizes a proportional and integral control
scheme with the integration occurring when the supply air
temperature is outside the deadband. As long as the
supply air temperature is within the setpoint deadband,
the system is considered to be satisfied and no staging up
or down will occur.
Supply Air Temperature Control with an
Economizer
The economizer is utilized to control the supply air cooling
at +1.5°F around the supply air temperature setpoint range
of 40°F and 90°F providing the outside air conditions are
suitable. While economizing, the mechanical cooling is
disabled until the economizer dampers have been fully
open for three minutes. If the economizer is disabled due
to unsuitable conditions, the mechanical cooling will cycle
as though the unit had no economizer.
VHR Relay Output
During unoccupied mode, daytime warm-up (DWU) and
morning warm-up (MWU) the VFD will open to 100%. All
VAV boxes must be opened through an ICS program or by
the VHR wired to the VAV boxes. The RTRM will delay
100% fan operation approximately 6.5 minutes when
switching from occupied cooling mode to a heating mode.
Zone Temperature Control without
a Night Setback Panel or ICS - Unoccupied
Cooling
When a field supplied occupied/unoccupied switching
device is connected between RTRM J6-11 and RTRM J6-12,
both the economizer and the mechanical cooling will be
disabled.
Zone Temperature Control without
a Night Setback Panel or ICS - Unoccupied
Heating
When a field supplied occupied/unoccupied switching
device is connected between RTRM J6-11 and J6-12 and
DWU is enabled, the zone temperature will be controlled at
10°F below the Morning Warm-up setpoint, but not less
than 50°F, by cycling one or two stages of either gas or
electric heat, whichever is applicable.
Morning Warm-up (MWU) Control
Morning Warm-up is activated if the zone temperature is at
least 1.5°F below the MWU setpoint whenever the system
switches from Unoccupied to Occupied status. The MWU
setpoint may be set from the unit mounted potentiometer
or a remotely mounted potentiometer. The setpoint
ranges are from 50°F to 90°F. When the zone temperature
meets or exceeds the MWU setpoint, the unit will switch to
the “Cooling” mode. The economizer will be held closed
during the morning warm-up cycle.
Daytime Warm-up (DWU) Control
Daytime Warm-up is applicable during occupied status
and when the zone temperature is below the initiation
temperature. It can be activated or deactivated through
ICS or a night setback zone sensor. If ICS or a night setback
zone sensor is not utilized, DWU can be activated by
setting the DWU enable DIP switch (RTAM) to ON and
supplying a valid morning warm-up setpoint. The unit is
shipped with a Morning Warm-up setpoint configured and
the Daytime Warm-up function is activated (switch on).
Opening the DWU enable switch will disable this function.
If the system control is local, the DWU initiation setpoint is
3°F below the Morning Warm-up setpoint. The termination
setpoint is equal to the Morning Warm-up setpoint. If the
system control is remote (Tracer™), the DWU setpoint is
equal to the Tracer Occupied heating setpoint. The
initiation and termination setpoints are selectable
setpoints designated by Tracer. When the zone
temperature meets or exceeds the termination setpoint
while the unit is in an Occupied, “Auto” Mode or switched
to the “Cooling” Mode, the unit will revert to the cooling
operation. If an Occupied “Heating” Mode is selected, the
unit will only function within the DWU perimeters until the
system is switched from the “Heat” Mode or enters an
Unoccupied status.
Note:
When a LCI is installed on a VAV unit, the MWU
setpoint located on the RTAM board is ignored. The
MWU and DWU setpoints come from the higher
priority LCI-R DAC.
Supply Duct Static Pressure Control
The supply duct static pressure is measured by a
transducer with a 0.25 to 2.125 Vdc proportional output
which corresponds to an adjustable supply duct static
pressure of 0.3" w.c. to 2.5" w.c. respectively with a
Table 19. Variable air volume mode operation
System Mode
Fan “Auto”
Fan “On”
Heat
DWU Active
DWU Off
DWU
2
Off
4
DWU
2
VAV Heating
4
Cool
VAV Cooling
1
VAV Cooling
1
Auto
DWU Active
DWU Off
DWU or
Cooling
1,2,3,4
VAV Cooling
1
DWU or
Cooling
1,2,3,4
VAV Cooling or
Heating
1
Off
Off
4
Off
4
Notes:
1. If Cooling is selected the supply fan will run continuously. If VAV
Heating is activated the supply fan will run continuously.
2. If Daytime Warmup is Activated, the supply fan will run
continuously.
3. Auto changeover between Cooling and Daytime
Warmup depends upon the DWU initiate setpoint.
4. The fan will be Off any time the system selection switch
is “Off”.