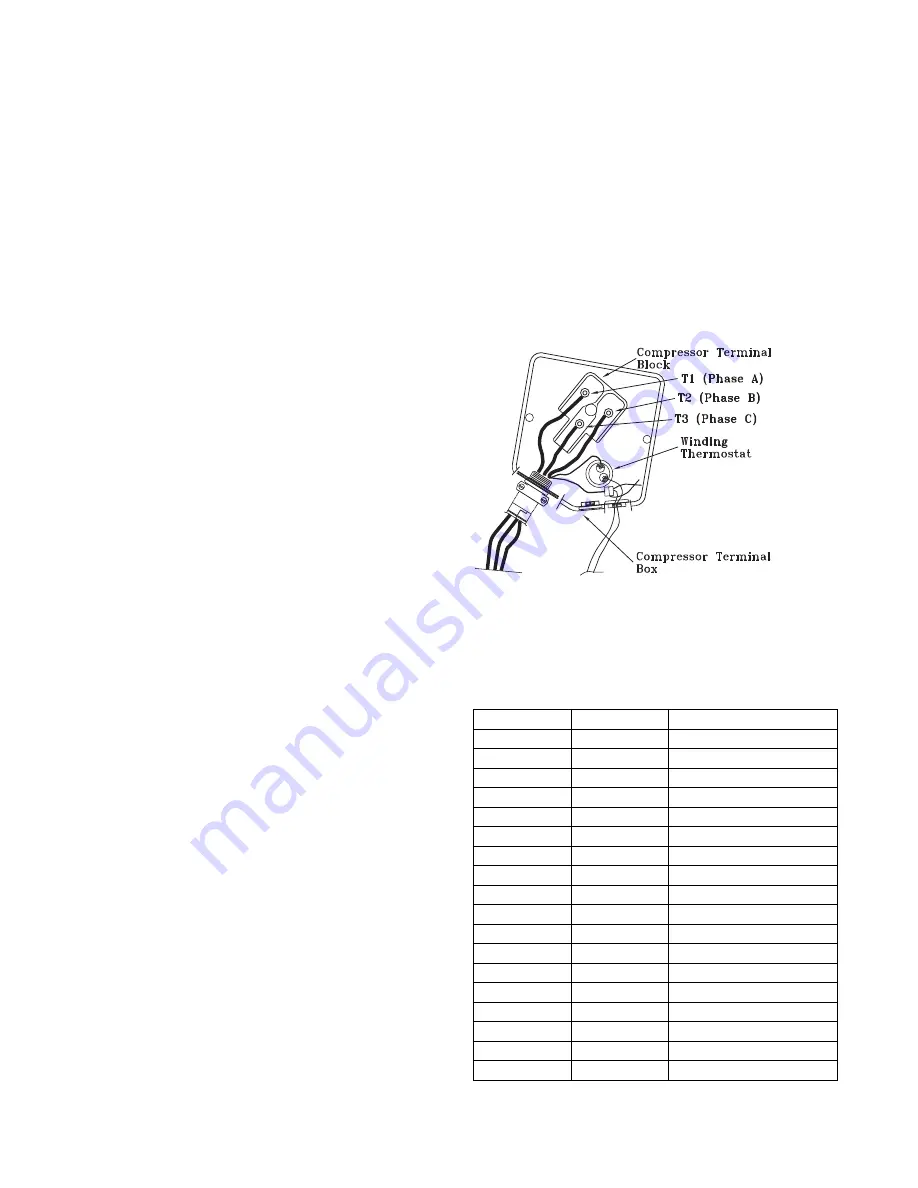
38
RT-SVX26R-EN
Start Up
Economizer Start-Up
Using the Service Test Guide in
momentarily jump across the Test 1 and Test 2 terminals
on LTB1 one-time to start the Minimum Ventilation Test.
1. Set the minimum position setpoint for the economizer
to the required percentage of minimum ventilation
using the setpoint potentiometer located on the
Economizer Control (ECA).
The economizer will drive to its minimum position
setpoint, exhaust fans (if applicable) may start at
random, and the supply fan will start when the
SERVICE TEST is initiated.
The Exhaust Fan will start anytime the economizer
damper position is equal to or greater than the exhaust
fan setpoint.
2. Verify that the dampers stroked to the minimum
position.
3. Momentarily jump across the Test 1 and Test 2
terminals on LTB one additional time if continuing
from previous component start-up or until the desired
start-up component Test is started.
4. Verify that the dampers stroked to the full open
position.
5. To stop the SERVICE TEST, turn the main power
disconnect switch to the “Off” position or proceed to
the next component start-up procedure. Remove
electro mechanical test mode connections (if
applicable).
Compressor Start-Up
1. Attach a set of service gauges onto the suction and
discharge gauge ports for each circuit. Refer to the
refrigerant circuit illustration in the Service Facts.
Using the Service Test Guide in
,
continue the Service Test start-up procedure for each
compressor circuit.
Momentarily jump across the Test 1 and Test 2
terminals on LTB1 one additional time if continuing
from previous component start-up or until the desired
startup component Test is started.
Scroll Compressors
a. Once each compressor has started, verify that the
rotation is correct. If wired correctly the suction
pressure should drop and the discharge pressure
should rise. If a scroll compressor is rotating
backwards, it will not pump and a loud rattling
sound can be observed.
b. If the electrical phasing is correct, before
condemning a compressor, interchange any two
leads (at the compressor Terminal block) to check
the internal phasing. Refer to the following
illustration for the compressor terminal/phase
identification. Do not allow the compressor to
operate backwards for more than 5 seconds.
Operation for a period of time longer than this will
result in compressor damage. Copeland (Alliance)
will experience failure also. If the compressor runs
backward for an extended period, the motor
winding can overheat and cause the motor winding
thermostat to open.
Note:
The Copeland, SSA and SPA scroll compressors for
R-410A units use Trane OIL00094. The correct oil for
Trane CSHD is Trane OIL00079 or OIL00080.
Compressor types are listed in
. The
appropriate oil charge is listed in
Figure 33.
Compressor terminal box
Table 13. Compressor types
Tonnage
C1
C2
YS*150
ZP83KCE
ZP42K5E
YH*150
ZP91KCE
ZP38K5E
YH*150 Reheat
ZP67KCE
ZP67KCE
YS*155
CSHD105
SPA050
YS*180
CSHD110
ZP54K5E
YH*180
ZP104KCE
ZP49K5E
YH*180 Reheat
ZP83KCE
ZP83KCE
YS*175
CSHD120
SPA044
YS*210
CSHD110
ZP54K5E
YH*210
ZP122KCE
ZP54K5E
YH*210 Reheat
CSHD089
ZP83KCE
YS*200
CSHD142
SSA083
YS*240
CSHD155
ZP76KCE
YH*240
CSHD142K*0M
ZP61K5E
YH*240 Reheat
CSHD120
CSHD120
YS*250
CSHD120
CSHD120
YS*300
CSHD161
ZP83KCE
YH*300
ZPT122K5E
ZP122KCE