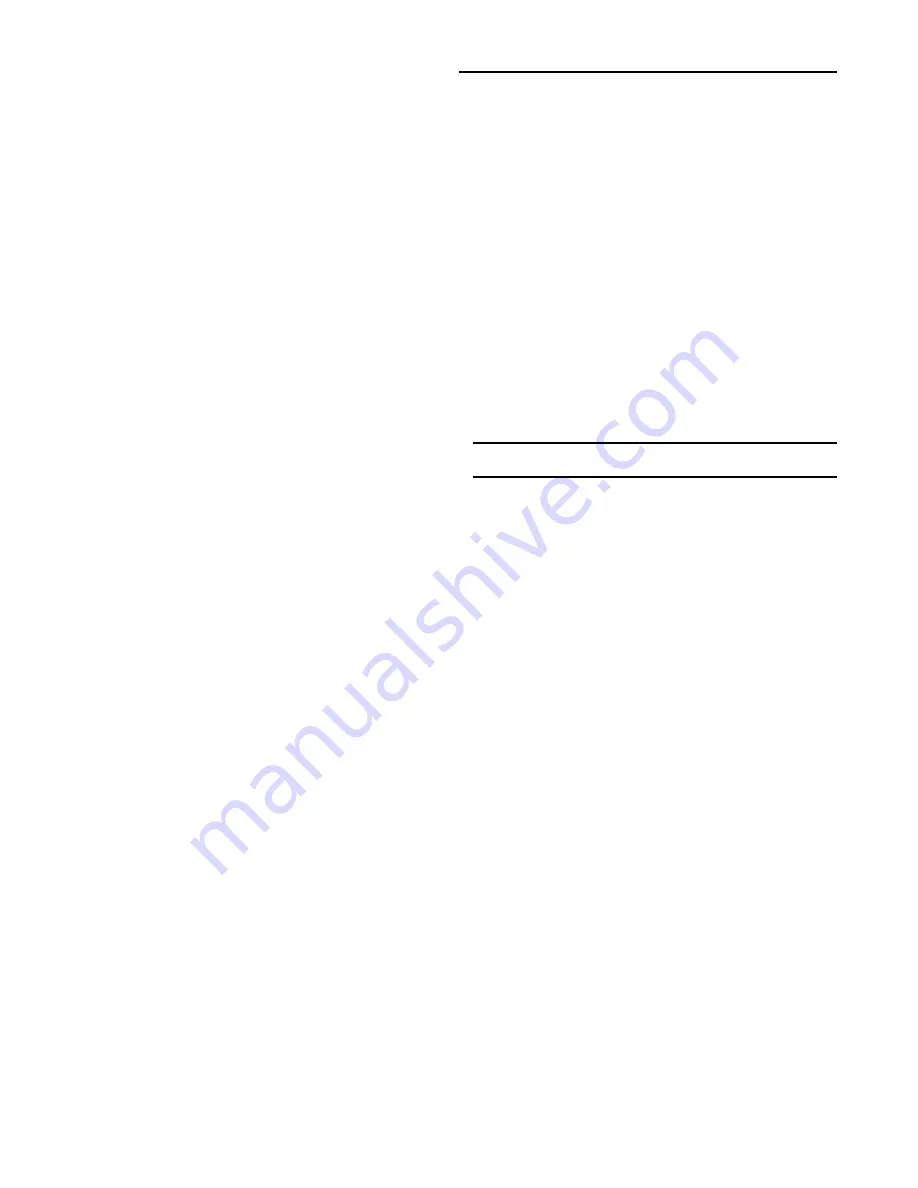
53
Starting the Compressors (Continued)
Scroll Compressor Operational Noises
Because the scroll compressor is designed to accommodate
liquids (both oil and refrigerant) and solid particles without
causing compressor damage, there are some characteristic
sounds that differentiate it from those typically
associated with a reciprocating compressor. These sounds
(which are described below) are characteristic, and do not
affect the operation or reliability of the compressor.
At Shutdown:
When a Scroll compressor shuts down, the gas within the
scroll compressor expands and causes momentary reverse
rotation until the discharge check valve closes. This results
in a “flutter” type sound.
At Low Ambient Start-Up
When the compressor starts up under low ambient condi-
tions, the initial flow rate of the compressor is low due to the
low condensing pressure. This causes a low differential
across the thermal expansion valve that limits its capacity.
Under these conditions, it is not unusual to hear the com-
pressor rattle until the suction pressure climbs and the flow
rate increases.
During Normal Operation
The scroll compressor emits a higher frequency tone (sound)
than a reciprocating compressor.
Compressor Crankcase Heaters
Each compressor is equipped with a crankcase heater.
When the compressor is "Off", the crankcase heater is ener-
gized. When the compressor is "On", the crankcase heater is
de-energized. The proper operation of the crankcase heater
is important to maintain an elevated compressor oil tempera-
ture during the "Off" cycle to reduce oil foaming during com-
pressor starts.
When the compressor starts, the sudden reduction in crank-
case pressure causes the liquid refrigerant to boil rapidly
causing the oil to foam. This condition could damage com-
pressor bearings due to reduced lubrication and could cause
compressor mechanical failures.
When power has been "Off" for an extended period, allow
the crankcase heater to operate a minimum of 8 hours be-
fore starting the unit.
Charging by Subcooling
The outdoor ambient temperature must be between 65° and
105° F and the relative humidity of the air entering the
evaporator must be above 40 percent. When the tempera-
tures are outside of these ranges, measuring the operating
pressures can be meaningless.
With the unit operating at "Full Circuit Capacity", acceptable
subcooling ranges between 14 F to 22 F.
Measuring Subcooling
1. At the liquid line service valve, measure the liquid line
pressure. Using a Refrigerant 22 pressure/temperature
chart, convert the pressure reading into the corresponding
saturated temperature.
2. Measure the actual liquid line temperature as close to the
liquid line service valve as possible. To ensure an accu-
rate reading, clean the line thoroughly where the tempera-
ture sensor will be attached. After securing the sensor to
the line, insulate the sensor and line to isolate it from the
ambient air.
Note: Glass thermometers do not have sufficient
contact area to give an accurate reading.
3. Determine the system subcooling by subtracting the actual
liquid line temperature (measured in step 2) from the satu-
rated liquid temperature (converted in step 1).
Summary of Contents for Voyager RT-SVX17C-EN
Page 8: ...8 Figure 1 Unit Dimensions for TC_ TE_ and YC_330 360 and 420 MBH Units Low Heat ...
Page 9: ...9 Figure 1 continued Unit Dimensions for YC_330 360 and 420 MBH Units High Heat ...
Page 10: ...10 Figure 1 continued Unit Dimensions for TC_ TE_ and YC_480 and 600 MBH Units Low High Heat ...
Page 24: ...24 Figure 10 Typical FieldWiring Requirements for CV Control Options ...
Page 78: ......
Page 79: ......
Page 80: ......