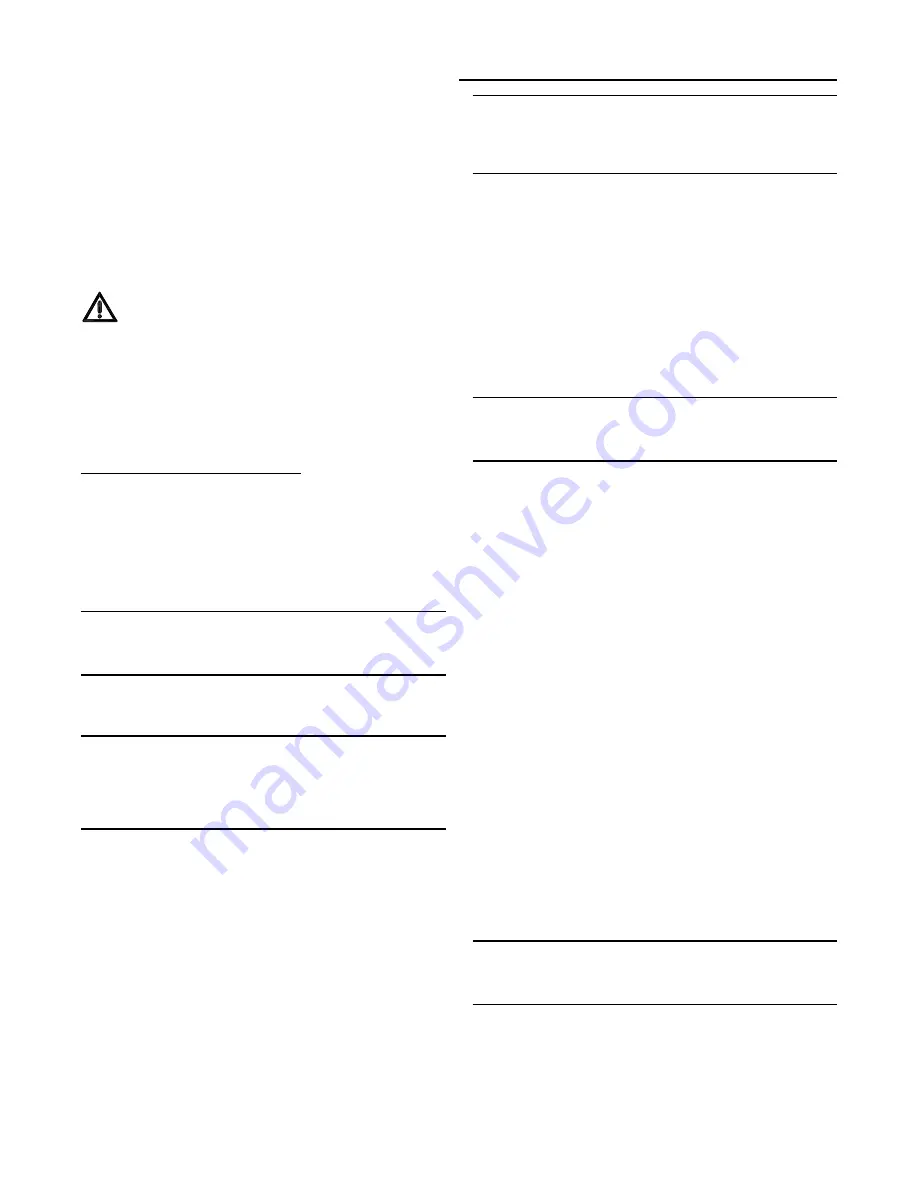
48
Starting the Compressors
9. Loosen the adjustment screws on each side of the damper
and slide it downward to the required opening.
10. Tighten the adjustment screws and re-install the mist
eliminators and the mist eliminator retainer bracket.
Open the main power disconnect or the unit mounted discon-
nect switch to shut the unit off and to reset the UCP.
Before closing the disconnect switch, ensure that the com-
pressor discharge service valve(s), suction service valve(s),
and liquid line service valve(s) are backseated.
CAUTION
Compressor Damage!
Do not allow liquid refrigerant to enter the suction line.
Excessive liquid accumulation in the liquid lines may re-
sult in compressor damage.
Compressor service valves must be fully opened before
start-up (suction, discharge, liquid line and oil line).
Starting 27.5 through 35 Ton units,
install a set of service
gauges onto the suction and discharge service ports. To start
the compressor Test, close the main power disconnect
switch or the unit mounted disconnect switch.
Jump across the "Test Terminals" on LTB1 three consecutive
times if it is a constant volume application, or five times if it is
a variable air volume application for two to three seconds per
jump. Refer to Figure 13 for the Cooling Test sequence.
Note: To prevent compressor damage due to no
refrigerant flow, do not pump the system down with
the compressor(s) below 7 PSIG under any
circumstance.
Once the first stage compressor has started, verify that the
compressor is rotating in the correct direction.
Note: If a scroll compressor is rotating backwards, it
will not pump and a loud rattling sound can be
observed. Check the electrical phasing at the
compressor terminal box. If the phasing is correct,
before condemning the compressor, interchange
any two leads to check the internal motor phasing.
If the compressors are allowed to run backward for an ex-
tended period (15 to 30 minutes), the motor windings can
overheat and cause the motor winding thermostats to open.
This will cause a “compressor trip” diagnostic and stop the
compressor.
With the first compressor operating safely, (i.e. sufficient op-
erating pressures), jump across the "Test Terminals" once
again. This will allow the second stage compressor to start.
Observe the operation of the compressors and the system
operating pressures.
After both compressors have been operating for approxi-
mately 30 minutes and all of the condenser fans are "On",
use Table 23 to determine the proper operating pressures.
For subcooling guidelines, refer to "Checking Subcooling" at
the end of this section.
Note! Do Not release refrigerant to the atmosphere!
If adding or removing refrigerant is required, the
service technician must comply with all federal,
state and local laws. Refer to general service
bulletin MSCU-SB-1 (latest edition).
Starting 40 and 50 Ton units,
install a set of service gauges onto the suction and discharge
service ports of each circuit. Follow the same procedures as
above to start the first stage of compressor operation.
After the compressor and the condenser fans have been op-
erating for approximately 30 minutes, use Table 24 or 25 to
determine the proper operating pressures for that circuit.
Jump across the "Test Terminals" once again. This will allow
the second stage compressors to start. The first stage com-
pressor will shut off providing the 3 minute "On" time has
elapsed.
Note: When the second refrigerant circuit is
requested to operate, both compressors will run
simultaneously. Verify that the compressors are
rotating in the correct direction.
Observe the operation of the compressors and the system
operating pressures. After both manifolded compressors and
condenser fans for the circuit have been operating for ap-
proximately 30 minutes, use Tables 24 or 25 to determine
the proper operating pressures. For subcooling guidelines,
refer to "Checking Subcooling" at the end of this section.
Units with Lead/Lag function disabled, jump across the "Test
Terminals" once again. This will allow the third stage of cool-
ing (number one circuit) to start providing the 3 minute "Off"
time has been satisfied.
Compressor Oil
Once all of the compressors have been started, verify that
the oil level is correct. The oil level may be down to the bot-
tom of the sightglass but should never be above the
sightglass.
After shutting the compressors off, check the oil’s appear-
ance. Discoloration of the oil indicates that an abnormal con-
dition has occurred. If the oil is dark and smells burnt
,
it has
overheated because of: compressor is operating at ex-
tremely high condensing temperatures; high superheat; a
compressor mechanical failure; or, occurrence of a motor
burnout.
If the oil is black and contains metal flakes, a mechanical fail-
ure has occurred. This symptom is often accompanied by a
high compressor amperage draw.
Note: If a motor burnout is suspected, use an acid
test kit to check the condition of the oil. Test results
will indicate an acid level exceeding 0.05 mg KOH/g
if a burnout occurred.
The scroll compressor uses Trane OIL-42 without substitu-
tion. The appropriate oil charge for a 9 and 10 Ton scroll
compressor is 8.5 pints. For a 14 and 15 Ton scroll compres-
sor, use 13.8 pints.
Summary of Contents for Voyager RT-SVX17C-EN
Page 8: ...8 Figure 1 Unit Dimensions for TC_ TE_ and YC_330 360 and 420 MBH Units Low Heat ...
Page 9: ...9 Figure 1 continued Unit Dimensions for YC_330 360 and 420 MBH Units High Heat ...
Page 10: ...10 Figure 1 continued Unit Dimensions for TC_ TE_ and YC_480 and 600 MBH Units Low High Heat ...
Page 24: ...24 Figure 10 Typical FieldWiring Requirements for CV Control Options ...
Page 78: ......
Page 79: ......
Page 80: ......