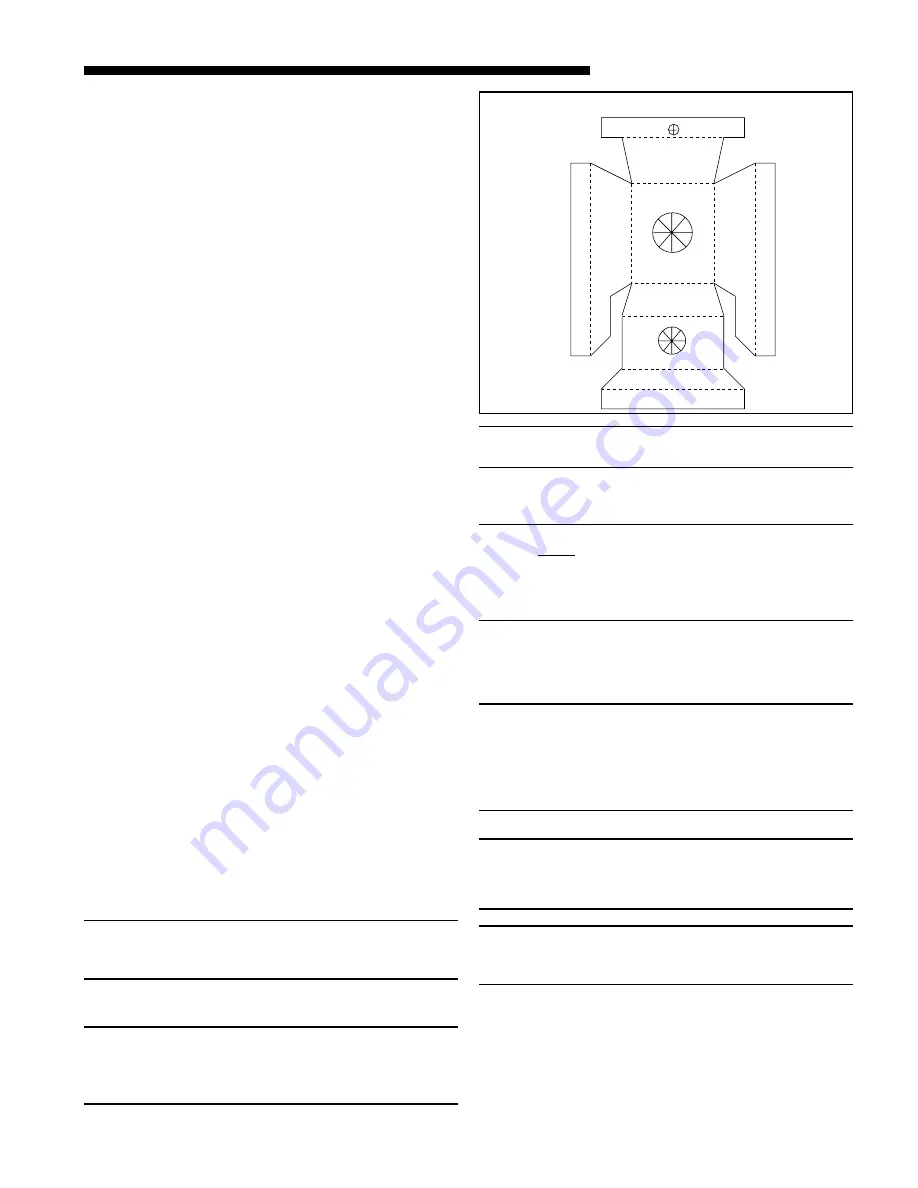
18-GE01D1-9
5
Installer’s Guide
face velocity of the filter being used. The factory
installed filter should then be removed
from the unit.
b. Unit is shipped from the factory in the upflow or
horizontal right configuration. Unit conversion is
not required.
c. The unit is designed for suspension using 1/4" -
20 threaded rods. Other means of suspension are
allowed as long as the unit is supported from
both ends as well as the middle to prevent sag-
ging and service access is not obstructed.
d. If the unit is not suspended it must be isolated
carefully to prevent sound transmission. Vibra-
tion isolators (purchased locally) must be placed
under the unit.
e. It is always recommended that an auxiliary drain
pan be installed under a horizontal air handler
(See Condensate Drain Piping) to prevent possible
damage to ceilings.
f. Isolate the auxiliary drain pan from the unit or
from the structure.
g. Connect the auxiliary drain line to a separate
drain line (no trap is needed in this line) and ter-
minate according to local codes.
h. If a return duct is connected to the Air Handler,
it must be the same dimensions as the return
opening shown in the outline drawings.
i. Openings where field wiring enters the cabi-
net must be completely sealed. Location of
power entry is shown on the outline drawing.
Use 2.5" clear stickers to seal all unused electrical
knockouts and cage nut openings.
C. DUCT CONNECTIONS
The supply and return air ducts should be connected to
the unit with flame retardant duct connectors.
Convertible duct flanges are provided on the discharge
opening to provide a “flush fit” for 3/4" or 1-1/2" duct board
applications, see the Outline drawing on page 10 for sizes
of the duct connections. After the duct is secured, seal
around the supply duct to prevent air leakage.
NOTE:
If the convertible duct flanges are not used, they must be
removed and discarded for proper airflow.
D. REFRIGERANT PIPING
IMPORTANT:
Refrigerant piping must be routed to maintain service access
to blower compartment and provide easy removal of filter
access panel and filter.
NOTE:
Refrigerant piping must be sealed along with field wiring.
1. Refrigerant connections are made outside the cabi-
net.
NOTE:
TXV bulb MUST be protected (wrap a wet rag around the
suction line between the TXV bulb and the braze joint) or
removed, while brazing the tubing. Overheating of the
sensing bulb will affect the functional characteristics and
performance of the air handler.
NOTE:
The Referigerant lines must be sealed and Electrical
inlets need to be sealed at both the low and the high
voltage.
2. Installation of refrigerant lines is covered in the in-
stallation instructions packaged with the outdoor unit.
Evacuation, leak testing and brazing procedures are in-
cluded in those instructions. Read those instructions be-
fore starting installation of refrigerant lines.
E. BRAZING TO EVAPORATOR SECTION
NOTE:
A brazing shield is provided in the information pack accom-
panying this unit. This shield fits over the refrigerant fittings
while brazing. Wet the shield before brazing. See Fig. 5.
IMPORTANT:
Do not unseal refrigerant tubing until ready to cut and fit
refrigerant lines.
1. Remove both sealing caps from indoor coil.
2. Field supplied tubing should be cut square, round
and free of burrs at the connecting end. Clean the
tubing to prevent contaminants from entering the
system.
BRAZE SHIELD
5