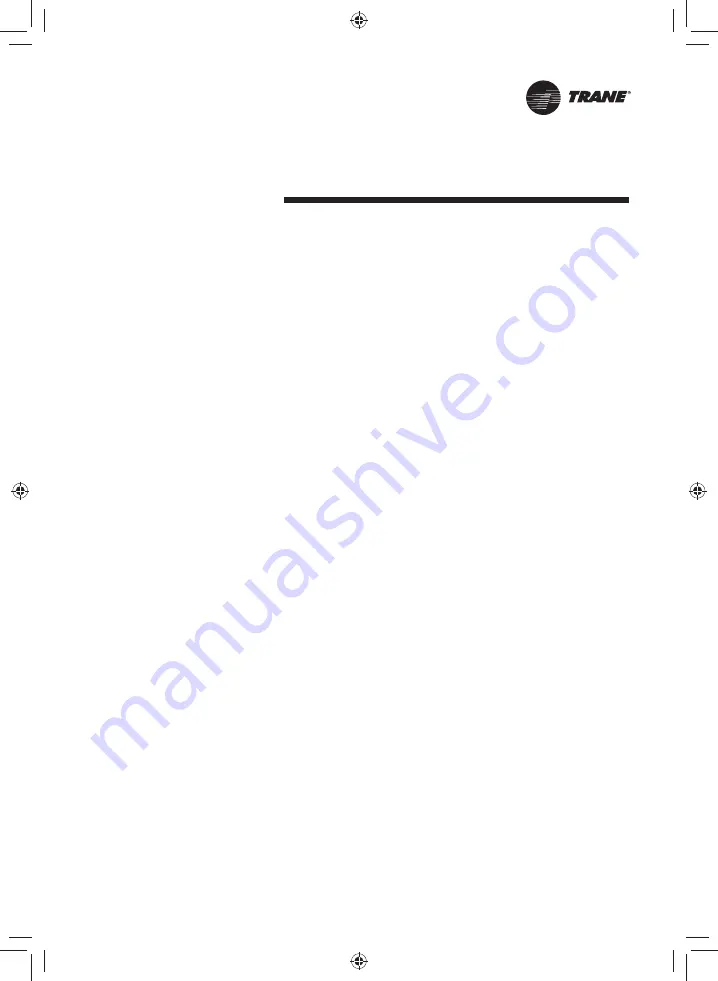
TTA-R407C-EN1113
23
Operation
Sequence of Operation
General
Operation of the system cooling
cycles is controlled by the position of
the system switch on the room
thermostat.
Evaporator Fan (Indoor Supply Air)
The evaporator fan is controlled by
an ON/AUTO switch on the room
thermostat. With the switch positioned
at AUTO and the system operating in
the cooling mode, fan operation
coincides with the cooling run cycles.
When the fan switch is positioned at
ON, fan operation is continuous.
Cooling Mode
With the disconnect switch in the
“ON” position, current is supplied
to the compressor crankcase heater
(s) and control transformer. The
crankcase heater (s) supplies heat to
the compressor (s) during the “OFF”
cycle. With the room thermostat
system switch positioned at COOL
and the fan switch at AUTO, the
compressor contactor energizes on a
call for cooling. When the contacts of
the compressor contactor energizes
on a call for cooling. When the
contacts of the compressor contactor
close, operation of the compressor
and condenser fan begins.
The evaporator fan contactor also
energizes on a call for cooling and
initiates evaporator fan operation.
On dual circuit units, when second
stage cooling is required, Y2 from the
indoor thermostat will energize 2nd
compressor.
Note:
With the thermostat fan switch
in the ON position, the evaporator
fan will operate continuously,
regardless of compressor or
condenser fan operation.
Safety Controls
Note: All of these controls may not be
installed on your unit, check electrical
schematic.
Low Pressure Cut-Out (LPCO)
This control’s sensor is located in the
suction (gas line, near the compressor).
This control will stop the compressor
and the outdoor fans in suction
pressure drops below the Low
Pressure Cut-Out setting.
High Pressure Cut-Out (HPCO)
This control’s sensor is located in the
liquid line. This device will shut off the
compressor and the outdoor fan (s) if
the discharge pressure exceeds the
High Pressure Cut-Out’s setting.
Internal Overload Protector (IOL)
This device is a current/thermal
actuated warp switch, imbedded
in the compressor motor windings.
If will shut off the compressor if
the temperature or current of the
compressor motor windings exceeds
its design trip temperature.
Note:
The IOL will put the
compressor back in operation once
the compressor motor heat has
dropped below the trip setting;
however, a check of the refrigerant
and electrical systems should be
made to determine the cause and
be corrected.
Installation Checklist
Complete this checklist once the
unit is installed to verify that all
recommended procedures have
been accomplished before starting
the system. Do not operate the
system until all items covered by this
checklist are complete.
❏
Inspect unit location for proper
required service clearances.
❏
Inspect unit location for proper free
air clearances.
❏
Inspect unit location for secure.
Level mounting position.
Refrigerant Piping
❏
Performed initial leak test?
❏
Connected properly sized and
constructed liquid and suction lines
to the connection stubs at both the
indoor and outdoor units?
❏
Insulated the entire suction line?
❏
Insulated portions of liquid line
exposed to extremes in
temperature?
❏
❏
Charge each circuit with proper
amount of R407C?
Electrical Wiring
❏
Provided unit power wiring (with
disconnect) to proper terminals in
the unit control Section?
❏
Installed system indoor thermostat?
❏
Installed system low voltage
interconnecting wiring to proper
terminals of outdoor unit, indoor
unit and system thermostat?
Unit Start-Up
Once the unit is properly installed and
pre-start procedures are complete,
start the unit by turning the System
Switch on the indoor thermostat to
either COOL or AUTO. The system
should operate normally.
the indoor air handler is closed before
operating the system. Operating the
outdoor unit without the indoor fan
energized, can cause unit trip-out on
high pressure control and/or liquid
flood-back to the compressors.
Evacuated each refrigerant circuit
to 350 microns (-76 cm.Hg)?
4
Caution:
Ensure the disconnect for
TTA-R407C-EN1113.indd 23
TTA-R407C-EN1113.indd 23
12-Sep-16 13:28:23
12-Sep-16 13:28:23