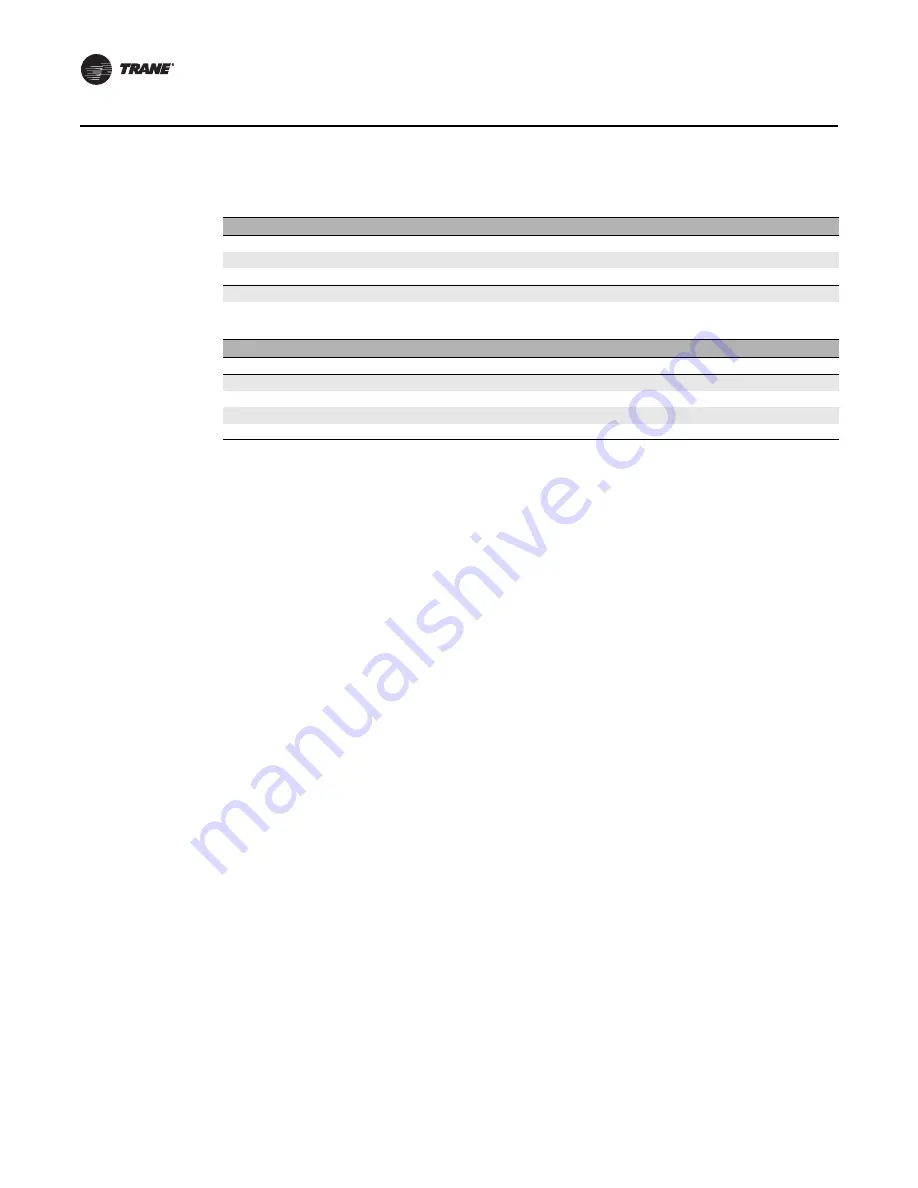
22
CLCH-SVX08A-EN
Wiring
Gas Heaters with 200–1000 MBh Output
Single-phase 120, 208, 230, 460 or 575 volt power is required to operate the heater controls or
power the transformer (TRANS1), if provided.
Single-phase power for 208, 230 460 and 575 voltage is provided for the gas heat off two legs of
the three-phase supply to the air-handling unit. A transformer in the piping vestibule is provided
to step down the voltage required for gas heat.
Gas Heaters with 1250–2400 MBh Output
Three-phase 208, 230, 460 or 575 volt power is required to operate the exhaust fan and power the
transformer (TRANS1).
Low-Voltage Wiring
NOTICE:
Equipment Damage!
The gas heat system must not operate without a supply fan providing airflow. Operating the gas
heat system without supply fan could result in equipment or property damage.
The gas heat control system requires a binary signal for on/off control. Provide an interlock in the
start-stop signal circuit with the air handler supply fan. This interlock must insure the start-stop
signal is interrupted to the gas heat system if the supply fan is shut off. The gas heat system must
not operate without the supply fan providing airflow.
The control system also requires a 0 to 10 Vdc analog signal for modulation where 10 Vdc is a signal
for full heat. A 4 to 20 mA interface module is available and may have been installed on the unit
for the control signal in lieu of the 0 to 10 Vdc signal.
Table 8.
Power supply requirements
3:1 and 10:1 Burner Turndown Units
Gas Output (MBh)
200-1000
1250-2000
2000
3
Voltage/Ph
115-575/1
208-575/3
208/230/460/575/3
Minimum Circuit Ampacity (MCA)
less than 15
less than 15
1
19.71/17.9/9.0/7.2
Maximum Overcurrent Protection (MOP)
15
15
2
25/25/15/15
Note:
1
All except the 2000 MBh output, 208 volt, 3 phase unit. This unit will have a marked MCA of 16.1
2
All except the 2000 MBh output, 208 and 230 volt, 3 phase units. These units have a marked MOP of 20
3
2000 MBh with optional 3 hp exhaust motor required for long horizontal flue vents
20:1 Burner Turndown Units
Gas Output (MBh)
1250-1750
2000
2400
Voltage/Ph
208-575/3
208/230/460/575/3
208/230/460/575/3
Minimum Circuit Ampacity (MCA)
less than 15
17.3/16.0/8.0/6.4
20.9/19.0/9.5/7.6
Maximum Overcurrent Protection (MOP)
15
20/20/15/15
25/25/15/15
Note:
The MCA and MOP for the 2000 MBh with optional 3 hp exhaust motor will be the same as 2400 MBh.
Summary of Contents for Gas Heat Sections for Performance Climate Changer Air Handlers
Page 23: ...CLCH SVX08A EN 23 Wiring Figure 13 200 1000 MBh 3 1 or 10 1 turndown wiring diagram ...
Page 24: ...24 CLCH SVX08A EN Wiring Figure 14 1250 2000 MBh 3 1 or 10 1 turndown wiring diagram ...
Page 25: ...CLCH SVX08A EN 25 Wiring Figure 15 1250 2400 MBh 20 1 turndown wiring diagram ...
Page 35: ...CLCH SVX08A EN 35 Notes ...