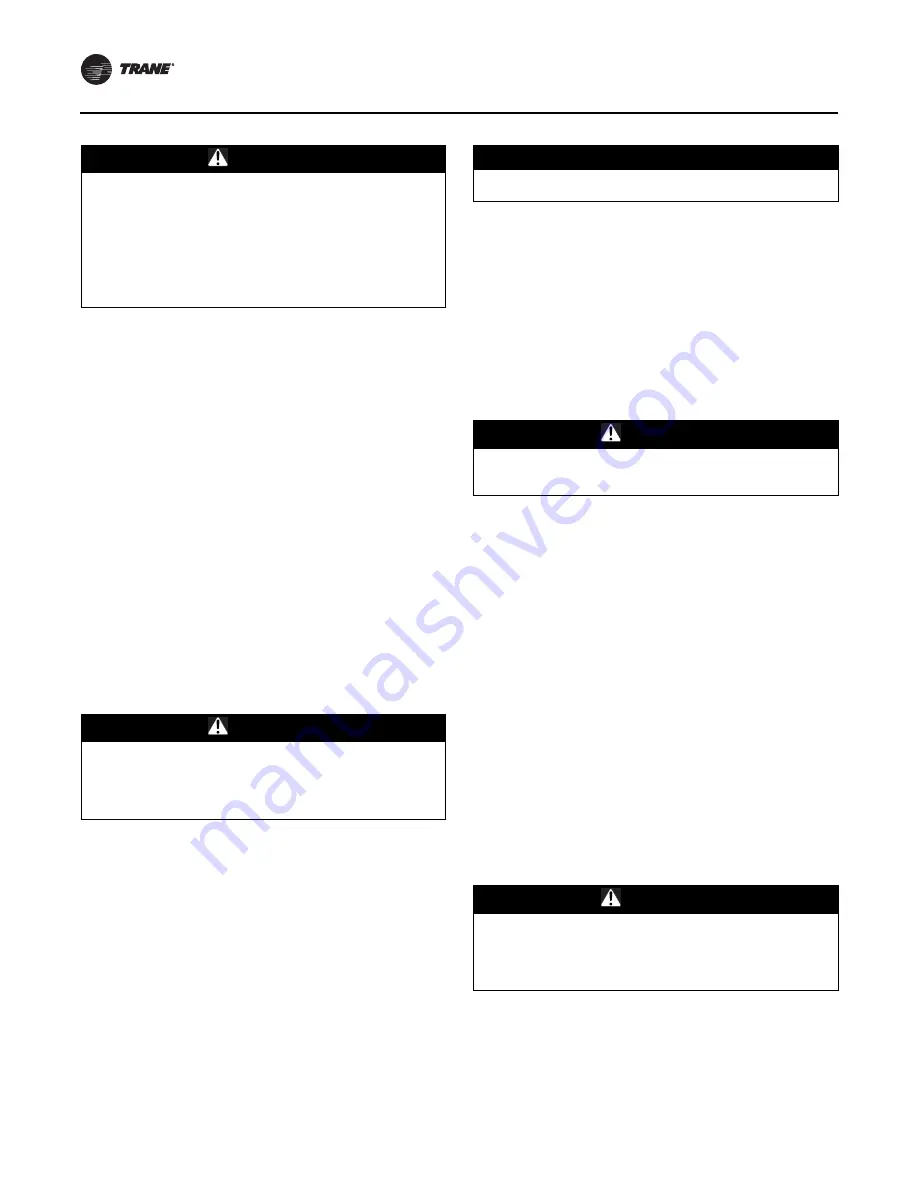
WARNING
Carbon Monoxide!
Your venting system must not be blocked by any snow,
snow drifts, or any foreign matter. Inspect your venting
system to ensure adequate ventilation exists at all
times! Failure to heed these warnings could result in
Carbon Monoxide Poisoning (symptoms include
grogginess, lethargy, inappropriate tiredness, or flu-like
symptoms).
Venting
20
GANE-SVX001B-EN
1. The combustion air system installation must be in
accordance with the current National Fuel Gas Code-
NFPA 54 or ANSI Z223.1 National Fuel Gas Code. In
Canada, installation must be in accordance with CSA-
B149.1 “Installation Code for Natural Gas Burning
Appliances and Equipment” and CSA-B149.2
“Installation Code for Propane Burning Appliances
and Equipment”.
2. A Breidert Type L or Fields inlet cap, furnished by the
customer, must be installed at the termination point of
the combustion air system, Figures 6A & 6B.
3. Each unit heater MUST have it’s own combustion air
system. It MUST NOT be connected to other air intake
systems.
4. Use UL 1738 Listed single wall pipe for the vent
system. For installations in Canada, use corrosion
resistant and gas-tight, listed vent pipe conforming
with local building codes, or in the absence of local
building codes, with current CSA-B149.1, Installation
Codes for Natural Gas Burning Appliances and
Equipment or CSA-B149.2, Installation Codes for
Propane Gas Burning Equipment.
WARNING
Never use pipe of a diameter other than that specified
in Table 1, page 4! Never use PVC, ABS or any other
non-metallic pipe for venting! To do so may result in
serious damage to the unit and or severe personal
injury or death!
5. Long runs of single wall combustion air piping passing
through an unheated space may require insulating if
condensation becomes noticeable.
6. The combustion air system must be installed to
prevent collection of condensate. Pitch horizontal
pipes downward 1/4 inch. per foot (21mm/m) toward
the inlet cap to facilitate drainage. Vertical combustion
air pipes should be piped as depicted in
Figure 11
.
7. The equivalent length of the vent system must not be
less than 5 ft. and must not exceed 50 ft. (15.2m).
Equivalent length equals the total length of straight
pipe plus 10 ft. (3.05m) for each 90° elbow and 4 ft.
(1.22m) for each 45° elbow.
NOTICE
For optimum performance keep the combustion air
system as straight as possible.
8. Each slip joint must be secured with at least three
corrosion resistant screws. Two full turns of 3M #425
Aluminum Foil Tape or its equivalent must then be
used to seal each joint. General Electric RTV-108, Dow-
Corning RTV-732 or an equivalent may be used instead
of the tape.
9. For horizontal combustion air systems longer than 5 ft.
(1.5m), the system must be supported from overhead
building structures at 3 ft. (1m) intervals.
Exhaust Venting
WARNING
Never operate unit heaters without combustion air and
flue gas piping in place or severe personal injury or
death may occur!
1. Vent system installation must be in accordance with
the current National Fuel Gas Code-NFPA 54 or ANSI
Z223.1 National Fuel Gas Code. In Canada installation
must be in accordance with CSA-B149.1 “Installation
Code for Natural Gas Burning Appliances and
Equipment” and CSA-B149.2. “Installation Code for
Propane Burning Appliances and Equipment”.
2. A Breidert Type L or Fields vent cap, furnished by the
customer, must be installed at the termination point of
the vent system, Figures 6A & 6B.
3. Each unit heater MUST have it’s own vent system. It
MUST NOT be connected to other vent systems or to
a chimney.
4. Use UL 1738 Listed single wall pipe. For installations in
Canada, use corrosion resistant and gas-tight, listed
vent pipe conforming with local building codes, or in
the absence of local building codes, with current CSA-
B149.1, Installation Codes for Natural Gas Burning
Appliances and Equipment or CSA-B149.2, Installation
Codes for Propane Gas Burning Appliances and
Equipment.
WARNING
Never use pipe of a diameter other than that specified
in Table 1, page 4! Never use PVC, ABS or any other
non-metallic pipe for venting! To do so may result in
serious damage to the unit and or severe personal
injury or death!
5. Any run of single wall vent pipe passing through an
unheated space must be insulated with an insulation
suitable to 550°F (288°C).
6. The vent system must be installed to prevent collection
of condensate. Pitch horizontal pipes downward 1/4 in.
per foot (21mm/m) toward the vent cap to facilitate