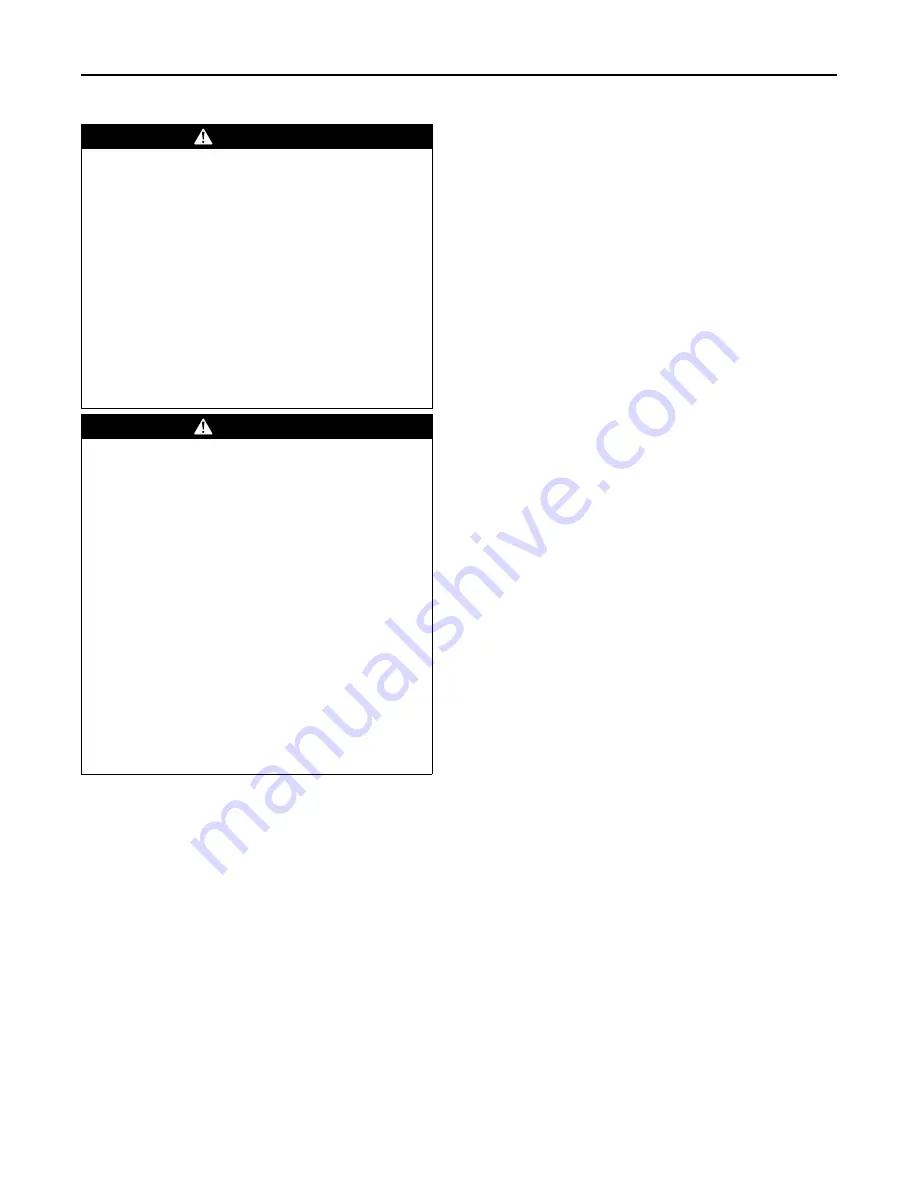
RT-SVX069D-EN
3
WARNING
Follow EHS Policies!
Failure to follow instructions below could result in
death or serious injury.
•
All Trane personnel must follow the company’s
Environmental, Health and Safety (EHS) policies
when performing work such as hot work,
electrical, fall protection, lockout/tagout,
refrigerant handling, etc. Where local
regulations are more stringent than these
policies, those regulations supersede these
policies.
•
Non-Trane personnel should always follow local
regulations.
WARNING
Hazard of Explosion or Fire!
Failure to follow instructions could result in death or
serious injury and equipment or property damage.
Do not store or use gasoline or other flammable
vapors and liquids in the vicinity of this or any other
appliance.
IF YOU SMELL GAS, follow instructions below:
•
Do not try to light any appliance.
•
Do not touch any electrical switch.
•
Do not use any phone in your building.
•
Open windows and doors.
•
Alert others and evacuate building immediately.
•
From a phone outside of the building,
immediately call your gas supplier. Follow the
gas supplier’s instructions. If you cannot reach
your gas supplier, call the fire department.
Overview of Manual
One copy of this document ships inside the control panel of
each unit and is customer property. It must be retained by
the unit’s maintenance personnel..
Important:
Do not release refrigerant to the atmosphere! If
adding or removing refrigerant is required, the
service technician must comply with all
federal, state, and local laws.
This booklet describes the proper installation, startup,
operation, and maintenance procedures for air cooled
systems.
By carefully reviewing the information within this manual
and following the instructions, the risk of improper
operation and/or component damage will be minimized.
It is important that periodic maintenance be performed to
help assure trouble free operation. A maintenance
schedule is provided at the end of this manual. Should
equipment failure occur, contact a qualified service
organization with qualified, experienced HVAC technicians
to properly diagnose and repair this equipment.
Copyright
This document and the information in it are the property of
Trane, and may not be used or reproduced in whole or in
part without written permission. Trane reserves the right to
revise this publication at any time, and to make changes to
its content without obligation to notify any person of such
revision or change.
Trademarks
All trademarks referenced in this document are the
trademarks of their respective owners.
Factory Training
Factory training is available through Trane University™ to
help you learn more about the operation and maintenance
of your equipment. To learn about available training
opportunities contact Trane University™.
Online:
Phone: 855-803-3563
Email:
Revision History
•
Updates to Dimensional Data chapter.
•
Updates to Electrical Data chapter.