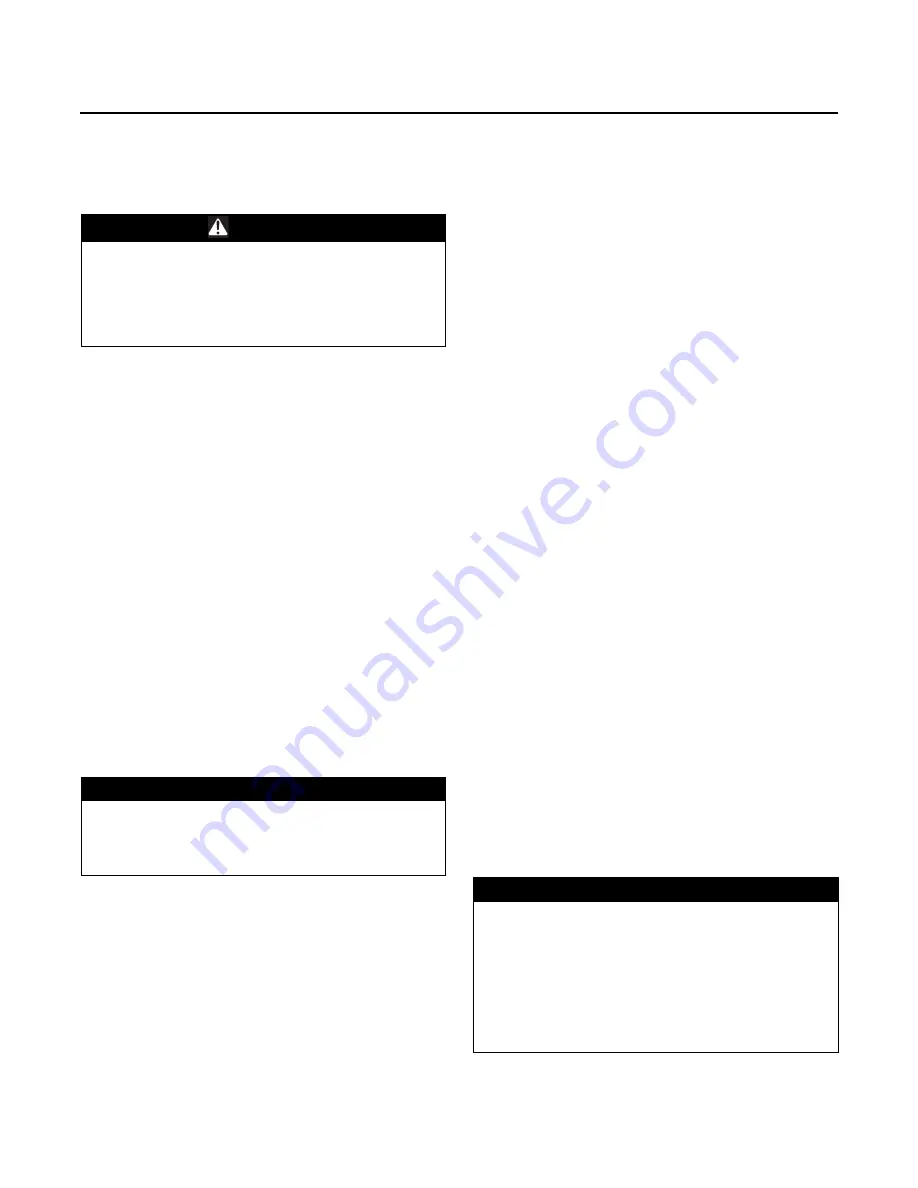
Maintenance
RT-SVX055D-EN
23
Monthly Maintenance
Before completing the following checks, turn the unit OFF
and lock the main power disconnect switch open.
WARNING
Hazardous Voltage!
Disconnect all electric power, including remote
disconnects before servicing. Follow proper lockout/
tagout procedures to ensure the power can not be
inadvertently energized. Failure to disconnect power
before servicing could result in death or serious injury.
Filters
Inspect the return air filters. Clean or replace them if
necessary. Refer to the unit Service Facts for filter
information.
Condensate Overflow Switch
During maintenance, the switch float (black ring) must be
checked to ensure free movement up and down.
Cooling Season
•
Check the unit’s drain pans and condensate piping to
ensure that there are no blockages.
•
Inspect the evaporator and condenser coils for dirt,
bent fins, etc. If the coils appear dirty, clean them
according to the instructions described in
•
Manually rotate the condenser fan(s) to ensure free
movement and check motor bearings for wear. Verify
that all of the fan mounting hardware is tight.
•
Inspect the F/A-R/A damper hinges and pins to ensure
that all moving parts are securely mounted. Keep the
blades clean as necessary.
NOTICE
Equipment Damage!
Never turn the motor shaft by hand or with a wrench.
Forcibly turning the motor shaft can damage the gear
train and motor beyond repair.
•
Verify that all damper linkages move freely; lubricate
with white grease, if necessary.
•
Check supply fan motor bearings; repair or replace the
motor as necessary.
•
Check the fan shaft bearings for wear. Replace the
bearings as necessary.
•
Check the supply fan belt. If the belt is frayed or worn,
replace it. Refer to
“Fan Belt Adjustment—Belt Drive
for belt replacement and adjustments.
•
Verify that all wire terminal connections are tight.
•
Remove any corrosion present on the exterior surfaces
of the unit and repaint these areas.
•
Generally inspect the unit for unusual conditions (e.g.,
loose access panels, leaking piping connections, etc.).
•
Make sure that all retaining screws are reinstalled in
the unit access panels once these checks are complete.
•
With the unit running, check and record the: ambient
temperature; compressor suction and discharge
pressures (each circuit); superheat (each circuit);
Record this data on an “operator’s maintenance log”
like the one shown in
. If the operating
pressures indicate a refrigerant shortage, measure the
system superheat. For guidelines, refer to
.
Note:
Do NOT release refrigerant to the atmosphere! If
adding or removing refrigerant is required, the
service technician must comply with all federal,
state and local laws.
Heating Season
•
Inspect the unit’s air filters. If necessary, clean or
replace them.
•
Check supply fan motor bearings; repair or replace the
motor as necessary.
•
Inspect both the main unit control panel and heat
section control box for loose electrical components
and terminal connections, as well as damaged wire
insulation. Make any necessary repairs.
•
Verify that the electric heat system operates properly.
Condenser Coil Cleaning
Regular coil maintenance, including annual cleaning,
enhances the unit’s operating efficiency by minimizing:
compressor head pressure and amperage draw;
evaporator water carryover; fan brake horsepower, due to
increase static pressure losses; airflow reduction.
At least once each year, or more often if the unit is located
in a “dirty” environment, clean the condenser coils using
the instructions outlined below. Be sure to follow these
instructions as closely as possible to avoid damaging the
coils.
Microchannel (MCHE) Coils
NOTICE
Coil Damage!
DO NOT use any detergents with microchannel
condenser coils. Use pressurized water or air ONLY,
with pressure no greater than 600psi. Failure to do so
could result in coil damage.
For additional information regarding the proper
microchannel coil cleaning procedure, refer to RT-
SVB83*-EN.
Due to the soft material and thin walls of the MCHE coils,
the traditional field maintenance method recommended