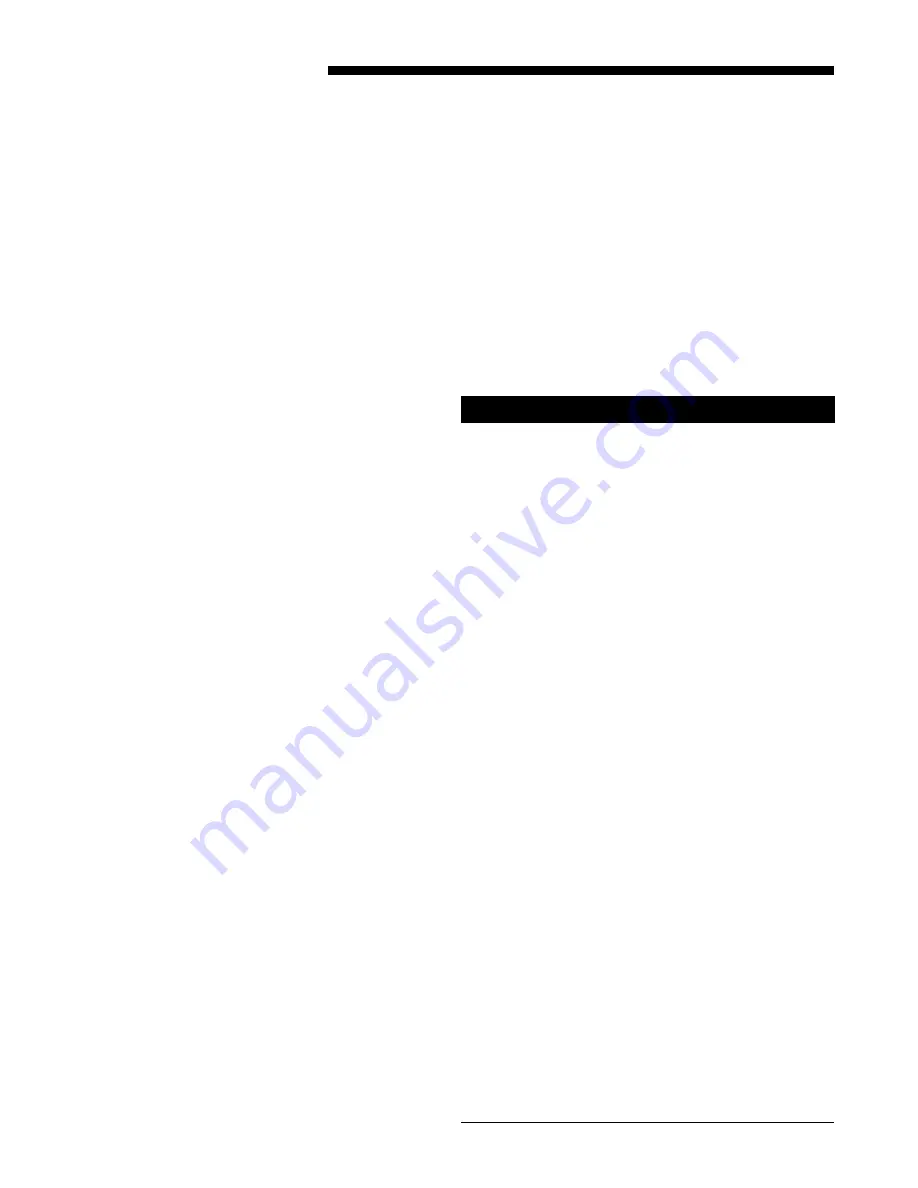
© 2009 Trane All Rights Reserved
18-CD29D1-3
Installer’s Guide
SAFETY SECTION
The following safety practices and precautions must be
followed during the installation, servicing, and operation
of this furnace.
1. Use only with the type of gas approved for this fur-
nace. Refer to the furnace rating plate.
2. Install this furnace only in a location and position as
specified in “Location and Clearances” (page 4), of
these instructions.
3. Provide adequate combustion and ventilation air to
the furnace space as specified in “Air for Combus-
tion and Ventilation” (pages 8-9), of these instruc-
tions.
4. Combustion products must be discharged outdoors.
Connect this furnace to an approved vent system
only, as specified in the “Venting” section (starting
on page 15), of these instructions.
5. Never test for gas leaks with an open flame. Use a
commercially available soap solution made specifi-
cally for the detection of leaks to check all connec-
tions, as specified in “Gas Piping” (pages 31-32), of
these instructions.
6. Always install the furnace to operate within the
furnace’s intended temperature-rise range with a
duct system which has an external static pressure
within the allowable range, as specified on the unit
rating plate. Airflow with temperature rise for cfm
versus static is shown in the Service Facts accompa-
nying this furnace.
7. When a furnace is installed so that supply ducts
carry air circulated by the furnace to areas outside
the space containing the furnace, the return air
shall also be handled by a duct(s) sealed to the fur-
nace casing and terminating outside the space con-
taining the furnace.
8. A gas-fired furnace for installation in a residential
garage must be installed as specified in “Location
and Clearances” section (page 4), of these instruc-
tions.
▲
WARNING
!
CARBON MONOXIDE POISONING HAZARD
Failure to follow the steps outlined below for each ap-
pliance connected to the venting system being placed
into operation could result in carbon monoxide poi-
soning or death.
The following steps shall be followed for each appli-
ance connected to the venting system being placed
into operation, while all other appliances connected to
the venting system are not in operation:
1. Seal any unused openings in the venting system.
2. Inspect the venting system for proper size and
horizontal pitch, as required in the National Fuel
Gas Code, ANSI Z223.1/NFPA 54 or the CAN/CGA
B149 Installation Codes and these instructions.
Determine that there is no blockage or restriction,
leakage, corrosion and other deficiencies which
could cause an unsafe condition.
3. As far as practical, close all building doors and
windows and all doors between the space in which
the appliance(s) connected to the venting system
are located and other deficiencies which could
cause an unsafe condition.
4. Close fireplace dampers.
5. Turn on clothes dryers and any appliance not con-
nected to the venting system. Turn on any exhaust
fans, such as range hoods and bathroom exhausts,
so they are operating at maximum speed. Do not
operate a summer exhaust fan.
6. Follow the lighting instructions. Place the appli-
ance being inspected into operation. Adjust the
thermostat so appliance is operating continuously.
7. If improper venting is observed during any of the
above tests, the venting system must be corrected
in accordance with the National Fuel Gas Code,
ANSI Z221.1/NFPA 54 and/or CAN/CGA B149.1 In-
stallation Codes.
8. After it has been determined that each appliance
connected to the venting system properly vents
where tested as outlined above, return doors, win-
dows, exhaust fans, fireplace dampers and any
other gas-fired burning appliance to their previous
conditions of use.
9. The furnace may be used for temporary heating of
buildings or structures under construction only
when the following conditions have been met:
a.
The furnace venting system must be complete
and installed per manufacturers instructions.
b.
The furnace is controlled only by a room ther-
mostat (no field jumpers).
c.
The furnace return air duct must be complete
and sealed to the furnace and clean air filters
are in place.
d.
The furnace input rate and temperature rise
must be verified to be within nameplate mark-
ing.
e.
100% of the furnace combustion air require-
ment must come from outside the structure.
Safety signal words are used to designate a degree or
level of seriousness associated with a particular hazard.
The signal words for safety markings are
WARNING
and
CAUTION
.
a.
WARNING
indicates a potentially hazardous situa-
tion which, if not avoided, could result in death or
serious injury.
b.
CAUTION
indicates a potentially hazardous situation
which, if not avoided, may result in minor or moder-
ate injury. It is also used to alert against unsafe
practices and hazards involving only property dam-
age.