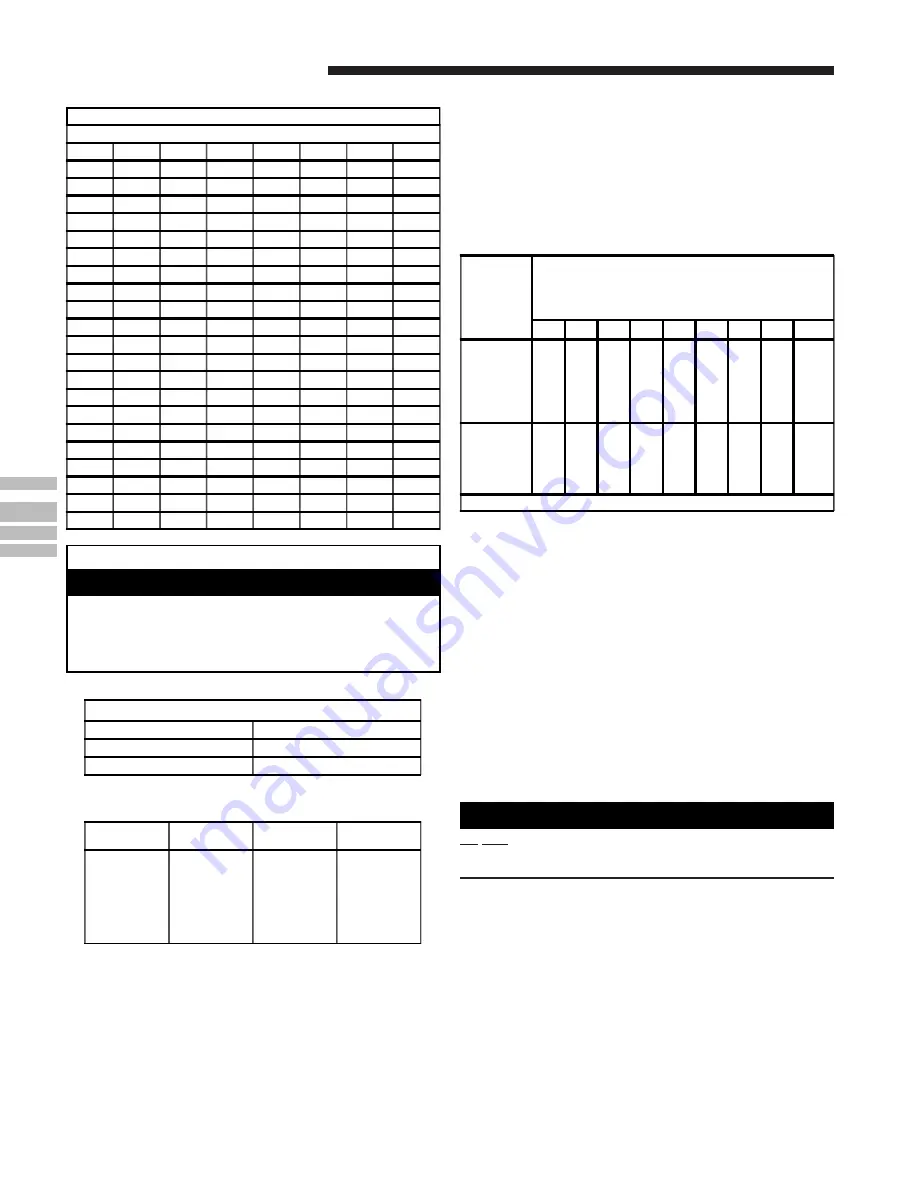
22
18-CD19D5-10
Installer’s Guide
If the desired input rate cannot be achieved with a change in
manifold pressure, then the orifices must be changed. LP
installations will require an orifice change. See Table 13 for help
in selecting orifices if orifice change is required. Furnace input
rate and temperature rise should be checked again after chang-
ing orifices to confirm the proper rate for the altitude.
Installations above 4,000 feet may require a pressure switch
change. If required, use the BAYHALT*** Kit (High Altitude
Accessory Kit) listed in PRODUCT DATA.
TABLE 13
Orifice
Twist Drill
Size If
Installed
At Sea
Level
ALTITUDE ABOVE SEA LEVEL
and Orifice Required At Other Elevations
2000 3000 4000 5000 6000 7000 8000 9000 10000
42
43
44
45
46
47
42
44
45
46
47
48
43
44
45
47
47
48
43
44
45
47
47
49
43
45
46
47
48
49
44
45
47
48
48
49
44
46
47
48
49
50
45
47
48
49
49
50
46
47
48
49
50
51
47
48
50
50
51
52
54
55
56
57
58
54
55
56
58
59
55
55
56
59
60
55
55
57
59
60
55
56
57
60
61
55
56
57
60
62
55
56
58
61
62
56
56
59
62
63
56
56
59
63
63
56
57
60
63
64
From National Fuel Gas Code - Table F-4
START-UP AND ADJUSTMENT
PRELIMINARY INSPECTIONS
With gas and electrical power “OFF”
1. Duct connections are properly sealed
2. Filters are in place
3. Venting is properly assembled
4. Blower door is in place
Flip the switch on the main gas valve within the unit to the
“OFF” position. Turn the external gas valve to “ON”. Purge the
air from the gas lines. After purging, check all gas connections
for leaks with a soapy solution — DO NOT CHECK WITH AN
OPEN FLAME. Allow 5 minutes for any gas that might have
escaped to dissipate. LP Gas being heavier than air may require
forced ventilation. Flip the switch on the gas valve in the unit to
the “ON” position.
LIGHTING INSTRUCTIONS
▲
WARNING
!
DO NOT attempt to manually light the burner. Failure to follow
this warning could result in property damage, personal injury,
or death.
Lighting instructions appear on each unit. Each installation
must be checked out at the time of initial start up to insure
proper operation of all components. Check out should include
putting the unit through one complete cycle as outlined below.
Turn on the main electrical supply and set the thermostat above
the indicated temperature. The ignitor will automatically heat,
then the gas valve is energized to permit the flow of gas to the
burners. After ignition and flame is established, the flame
control module monitors the flame and supplies power to the gas
valve until the thermostat is satisfied.
TABLE 10
GAS FLOW IN CUBIC FEET PER HOUR
2 CUBIC FOOT DIAL
SEC. FLOW SEC. FLOW SEC. FLOW SEC. FLOW
8
900
29
248
50
144
82
88
9
800
30
240
51
141
84
86
10
720
31
232
52
138
86
84
11
655
32
225
53
136
88
82
12
600
33
218
54
133
90
80
13
555
34
212
55
131
92
78
14
514
35
206
56
129
94
76
15
480
36
200
57
126
96
75
16
450
37
195
58
124
98
73
17
424
38
189
59
122
100
72
18
400
39
185
60
120
104
69
19
379
40
180
62
116
108
67
20
360
41
176
64
112
112
64
21
343
42
172
66
109
116
62
22
327
43
167
68
106
120
60
23
313
44
164
70
103
124
58
24
300
45
160
72
100
128
56
25
288
46
157
74
97
132
54
26
277
47
153
76
95
136
53
27
267
48
150
78
92
140
51
28
257
49
147
80
90
144
50
The following warning complies with State of California law, Proposition 65.
Hazardous Gases!
Exposure to fuel substances or by-products of incomplete
fuel combustion is believed by the state of California to
cause cancer, birth defects, or other reproductive harm.
▲
WARNING
!
TABLE 11
FINAL MANIFOLD PRESSURE SETTINGS
FUEL
PRESSURE
NATURAL GAS
3.5" W.C.
LP GAS
11.0" W.C.
TABLE 12
PART NUMBERS FOR REPLACEMENT ORIFICES
DRILL
SIZE
PART
NUMBER
DRILL
SIZE
PART
NUMBER
44
45
46
47
48
49
50
ORF00501
ORF00644
ORF00909
ORF00910
ORF01099
ORF00503
ORF00493
54
55
56
57
58
59
ORF00555
ORF00693
ORF00907
ORF00908
ORF01338
ORF01339
HIGH ALTITUDE DERATE
Input ratings (BTUH) of these furnaces are based on sea level
operation and should not be changed at elevations up to 2,000 ft.
If the installation is 2,000 ft. or above, the furnace input rate
(BTUH) shall be reduced 4% for each 1,000 ft. above sea level.
The furnace input rate shall be checked by clocking the gas flow
rate (CFH) and multiplying by the heating value obtained from
the local utility supplier for the gas being delivered at the
installed altitude. Input rate changes can be made by adjusting
the manifold pressure (min 3.0 - max 3.7 in. W.C. - Natural Gas)
or changing orifices (orifice change may not always be required).