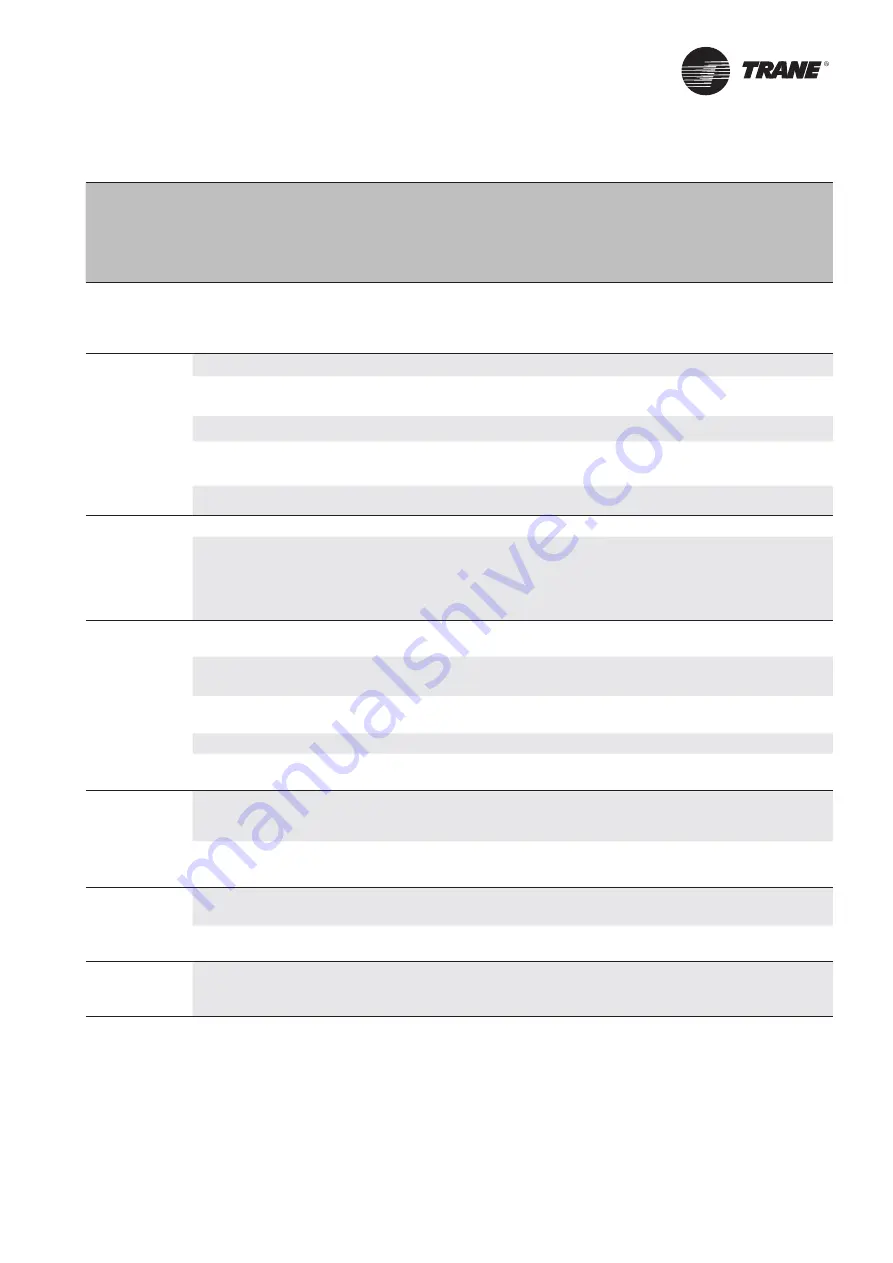
63
RF-SVX003A-GB
Troubleshooting
SYMPTOM
cooling
heating
Who can take
corrective
action
U = User
S = specialised
personnel
Probable cause
Possible remedy
I
Frost in
liquid pipe
downstream
from a
fi
lter
X
X
S
The liquid
fi
lter is clogged
Replace the
fi
lter
L
The unit
works
continuously
without ever
stopping
X
X
S
Lack of refrigerant gas
See item G.
X
X
U
Incorrect tuning of the
operating thermostat
Check the setting
X
X
S
Excessive thermal load
Reduce the thermal load
X
X
S
Compressor does not give
the thermal output
Check, change or revise
X
X
S
The liquid
fi
lter is clogged
Replace
M
The
unit works
regularly
but with an
insuf
fi
cient
capacity
X
X
S
Low refrigerant charge
See point G
X
X
S
4-way reversing valve
defective
Check the power supply
and the coils of the valve
and replace the valve
N
Frost in the
compressor
intake pipe
X
X
S
Expansion device that is
not working properly
Verify replace
X
S
Water circulation pump
blocked
Unlock the pump
X
X
S
Water circulation pump
defective
Check the pump and
replace if necessary
X
X
S
Low refrigerant charge
See point G
X
X
S
The liquid
fi
lter is clogged
Replace
O
The
defrosting
cycle is never
activated
X
S
4-way reversing valve
defective
Check the power supply
and the coil of the valve
and replace the valve
X
S
The defrost thermostat
is worn out or has an
incorrect calibration value
Check and replace if
defective or change the
calibration value
P
Abnormal
noises
detected in
the system
X
X
S
Compressor noisy
Check and replace if
necessary
X
X
S
The panels vibrate
Fasten properly
Q
Unit does
not start
X
X
s
phases of the supply
network reversed
Invert phases