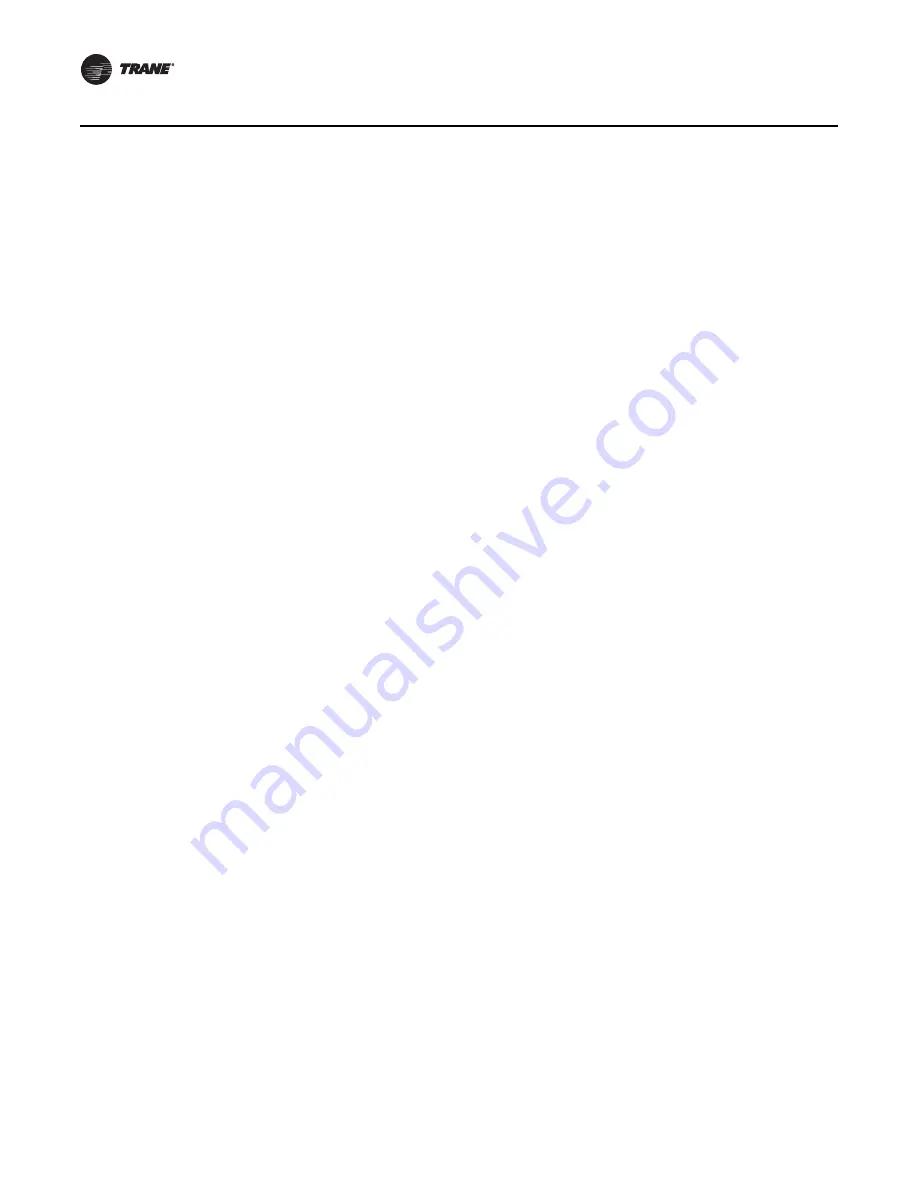
58
T-Series Climate Changer Air Handler IOM •
CLCH-SVX06A-EN
Installation - Piping
Liquid Lines
Line Sizing.
Properly sizing the liquid line is critical to a successful split-system
application. The selected tube diameter must provide at least 5°F [2.7°C] of subcooling
at the expansion valve throughout the operating envelope. Increasing the size of the
liquid line will not increase the available subcooling.
Routing.
Install the liquid line with a slight slope in the direction of flow so that it can be
routed with the suction line. Minimize tube bends and reducers because these items tend
to increase pressure drop and to reduce subcooling at the expansion valve. Liquid line
receivers, other than those that are factory-installed, are not recommended.
Insulation. The liquid line is generally warmer than the surrounding air, so it does not
require insulation. In fact, heat loss from the liquid line improves system capacity
because it provides additional subcooling.
Components. Liquid-line refrigerant components necessary for a successful job include
a filter drier, access port, solenoid valve, moisture-indicating sight glass, expansion
valve(s), and ball shutoff valves.
Figure 44
illustrates the proper sequence for positioning
them in the liquid line. Position the components as close to the evaporator as possible.
•
Filter drier. There is no substitute for cleanliness during system installation. The filter
drier prevents residual contaminants, introduced during installation, from entering
the expansion valve and solenoid valve.
•
Access port. The access port allows the unit to be charged with liquid refrigerant and
is used to determine subcooling. This port is usually a Schraeder valve with a core.
•
Solenoid valve. In split systems, solenoid valves isolate the refrigerant from the
evaporator during off cycles; under certain conditions, they may also trim the amount
of active evaporator as compressors unload. Generally, the “trim” solenoid valve is
unnecessary for variable-air-volume comfort-cooling applications, and is only
required for constant-volume applications when dehumidification is a concern.
•
Moisture-indicating sight glass. Be sure to install one moisture-indicating sight glass
in the main liquid line. The only value of the sight glass is its moisture indication
ability. Use actual measurements of temperature and pressure—not the sight glass—
to determine subcooling and whether the system is properly charged. The moisture
indicator/sight glass must be sized to match the size of the liquid line at the thermal
expansion valve.
•
Thermal expansion valve. The expansion valve is the throttling device that meters the
refrigerant into the evaporator coil. Metering too much refrigerant floods the
compressor; metering too little elevates the compressor temperature. Choosing the
correct size and type of expansion valve is critical to assure it will correctly meter
refrigerant into the evaporator coil throughout the entire operating envelope of the
system. Correct refrigerant distribution into the coil requires an expansion valve for
each distributor.