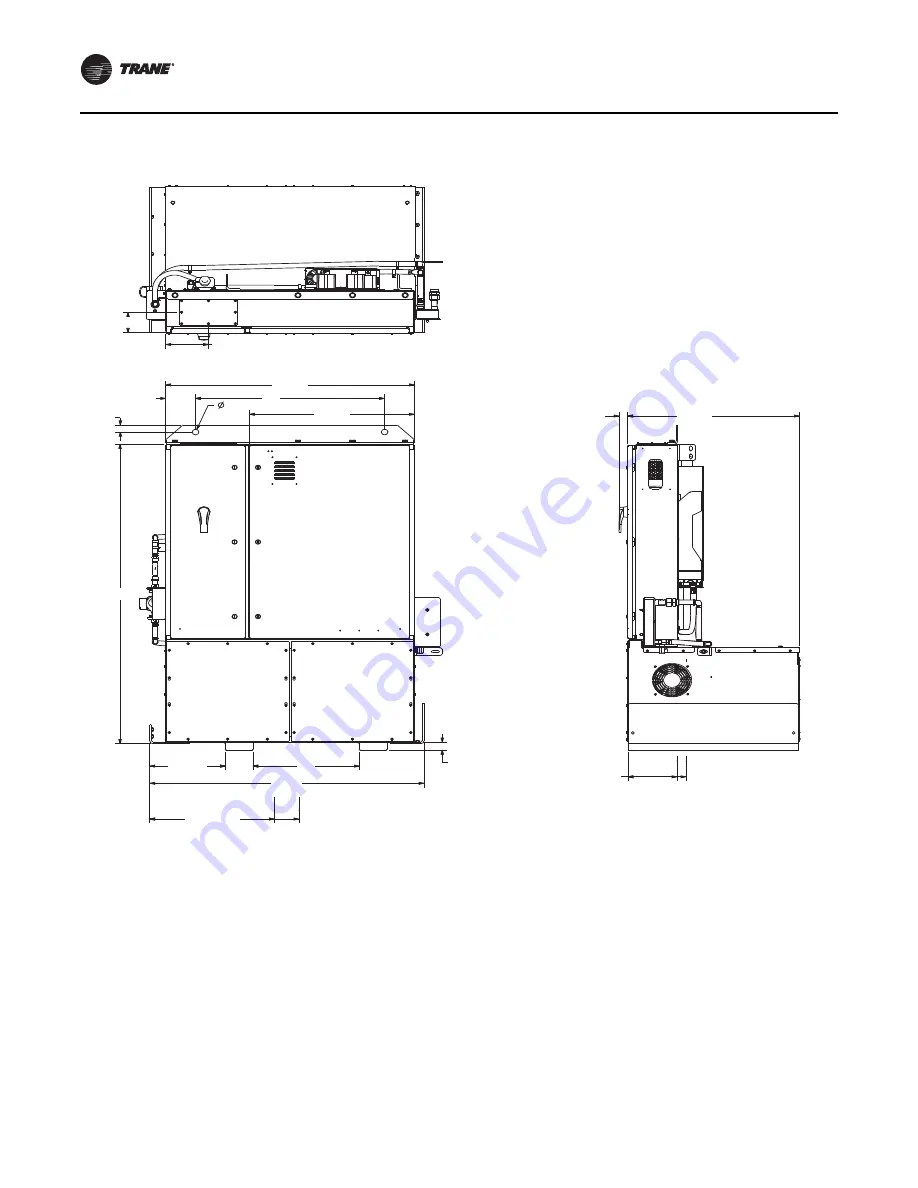
Components and Weights
8
CVHM-SVN001C-EN
Note:
The holes on the top of the drive can be used for
lifting the drive.
Figure 2.
CVHM drive dimensions, in.
56-5/8
15-11/16
5-5/8
22
1-7/8
CENTER
OF GRAVITY
26 TO 31
CENTER
OF GRAVITY
10 TO 12
72-5/16
1-11/16
51-5/16
6-1/8
39
1-3/8
1-3/4
35-7/16
34-1/16
5
8-13/16