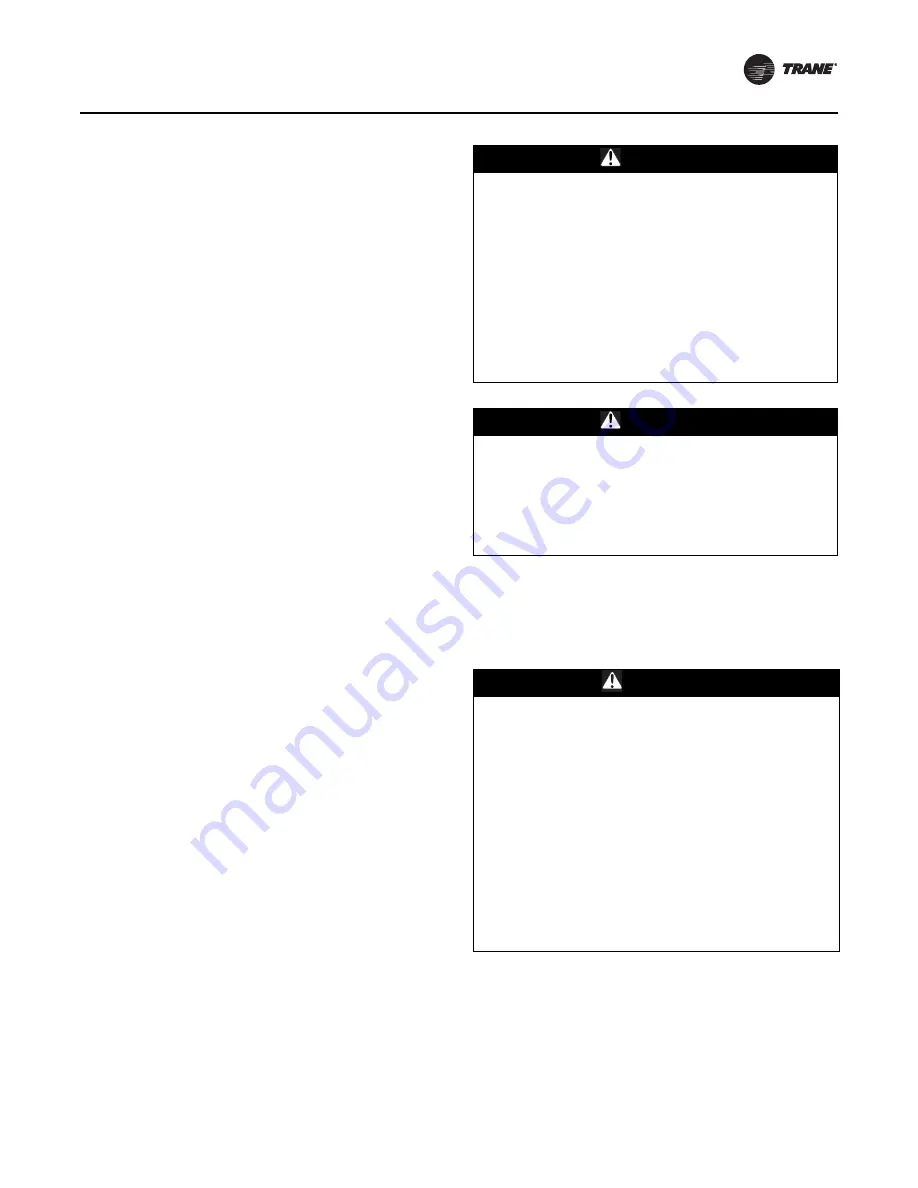
Disassembly
CVHM-SVN001C-EN
11
•
Recharge the chiller with dry nitrogen to 5 psig; the
contractor should assist a qualified Trane Technician
with this responsibility
•
Replace and/or repair insulation
•
Reconnect electrical connections
•
Spot paint the chiller if necessary
The disassembly and reassembly procedures described in
this manual should be performed only on chillers that have
been ordered with this shell option. The process is to be
initiated by experienced service technicians. Contact your
local Trane Service office for assistance if required.
This manual discusses a typical disassembly process.
Proper lifting techniques vary based on mechanical room
layout.
•
It is the responsibility of the person(s) performing the
work to be properly trained in the safe practice of
rigging, lifting, securing, and fastening the
components involved.
•
It is the responsibility of the person(s) providing and
using the rigging and lifting devices to inspect these
devices to ensure they are free from defect and are
rated to meet or exceed the published weights.
•
Always use rigging and lifting devices in accordance
with the applicable instructions for such devices.
•
Cap or cover open lines to prevent entry of foreign
material
.
Note:
Additional O-rings and couplings are shipped with
the chiller when the separable shell kit is selected.
Also refer to wiring diagram 2311-4146*.
Wiring Disassembly
Before separating shells, remove the purge, the
compressor, wrap pipe, economizer line, control panel,
and the various unit mounted sensors (frame LLIDs) as
indicated. If possible, the best method is to remove the
sensor and carefully coil the wire after labeling the device
and its location to aid in reinstallation. All sensors connect
to the buss wiring with a universal plug. This allows easy
disconnection and reconnection of the sensors.
Adaptive Frequency Drive
Removal
If you need to temporarily remove the entire Adaptive
Frequency™ Drive (AFD) cabinet from the chiller to allow
unit installation through restricted spaces or the AFD
cabinet shipped disassembled from the chiller, use the
following general information and instructions. The
maximum weight of the drive is 1900 lb (862 kg).
Note:
For specific weights of the AFD cabinet, refer to
submittal package.
1. Remove the AFD upper support bracket bolts at the
wrap-around pipe side. There are two bolts in each
bracket.
2. Close the isolation valves for the AFD cooling lines,
both feed and return.
WARNING
Heavy Objects!
Failure to follow instructions below or properly lift
component could result in component dropping and
possibly crushing operator/technician which could
result in death or serious injury, and equipment or
property-only damage. Ensure that all the lifting
equipment used is properly rated for the weight of the
component being lifted. Each of the cables (chains or
slings), hooks, and shackles used to lift the component
must be capable of supporting the entire weight of the
component. Lifting cables (chains or slings) may not be
of the same length. Adjust as necessary for even
component lift.
WARNING
Improper Unit Lift!
Failure to properly lift unit could result in death or
serious injury or possible equipment or property-only
damage. Test lift unit approximately 24 inches (61 cm)
to verify proper center of gravity lift point. To avoid
dropping of unit, reposition lifting point if unit is not
level.
WARNING
Hazard of Explosion and Deadly Gases!
Failure to follow all proper safe refrigerant handling
practices could result in death or serious injury.
Never solder, braze or weld on refrigerant lines or any
unit components that are above atmospheric pressure
or where refrigerant may be present. Always remove
refrigerant by following the guidelines established by
the EPA Federal Clean Air Act or other state or local
codes as appropriate. After refrigerant removal, use dry
nitrogen to bring system back to atmospheric pressure
before opening system for repairs. Mixtures of
refrigerants and air under pressure may become
combustible in the presence of an ignition source
leading to an explosion. Excessive heat from soldering,
brazing or welding with refrigerant vapors present can
form highly toxic gases and extremely corrosive acids.