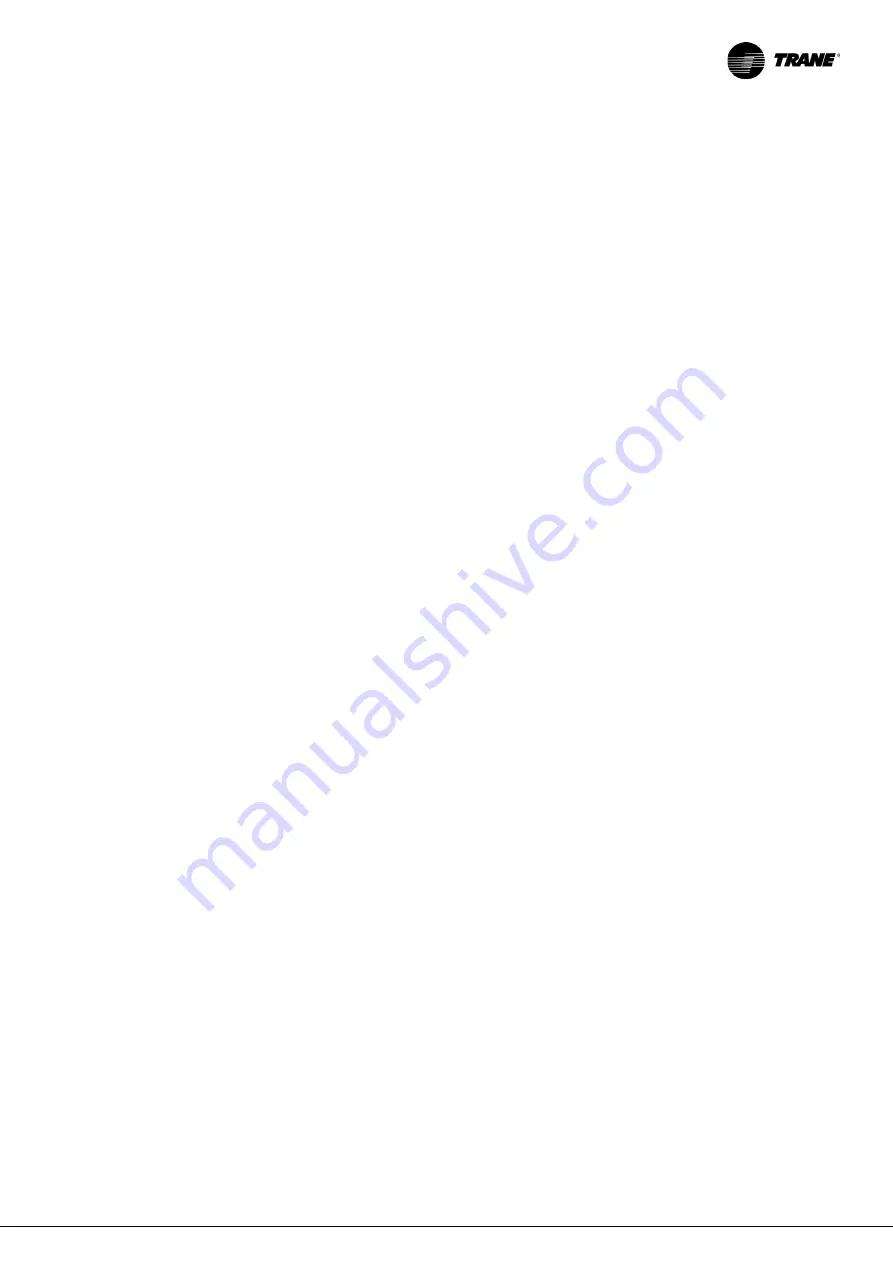
Page 37
11 OPERATOR RESPONSIBILITIES
It is important that the operator is properly trained and familiar with the equipment before working on the unit. In
addition to reading this manual, the operator must study the manual operation of the microprocessor and the
wiring diagram to understand the sequence of start- up, operation, shutdown sequences, and the criterion of
operation of all safety devices. During the initial start-up of the unit an authorized technician is available to
answer any questions and educate on the proper functioning. We recommend the operator to maintain a record
of the operating data for each unit installed and all maintenance activities and periodic service. If the operator
observes abnormal or unusual operating conditions, consult the authorized service technician.
12 START-UP PRELIMINARY PROCEDURES
12.1
STARTING CHECK
Before starting the unit, even only momentarily, all the machinery supplied by the chilled water, like the air
handling units, pumps, etc. have to be checked. The pump auxiliary contacts and the flow switch have to be
connected to the control panel as indicated in the electrical diagram. Before carrying out interventions on the
valve regulations, loosen the relevant valve gland. Open the discharge valve of the compressor. Open the liquid
shutoff valve placed on the liquid line. Measure the suction pressure. If it is lower than 0.42 MPa pry open the
solenoid valve on the liquid line by means of an electrical bridge. Bring the suction pressure to 0.45 MPa, then
remove the jumper. Charge all the water circuit progressively. Starts up the water pump of the evaporator with
the calibration valve shut and then slowly open it.
Discharge the air from the high points of the water circuit and check the direction of the water flow. Carry out
calibration of the flow by using a measurer (if present or available) or by means of a combination of the
readings of the manometers and the thermometers. In the starting phase calibrate the valve on the pressure
difference read on the manometers, carry out drainage of the tubes and then carry out fine calibration on the
temperature difference between the water in and the water out. The regulation is calibrated in the factory for
water in to the evaporator at 12°C and water out at 7°C. With the general switch open, check that the electrical
connections are tightly clamped. Check for any possible refrigerant leaks. Check that the electrical data on the
label correspond to those of the mains supply. Check that the thermal charge available is appropriate for
starting.
12.2
REFRIGERANT CHARGE
Trane CCUF units are shipped without any refrigerant charge
Danger: Do not use the compressor to vacuum the system.
Summary of Contents for CCUF
Page 26: ...Page 26 USER SIDE...
Page 28: ...Page 28 USER SIDE...