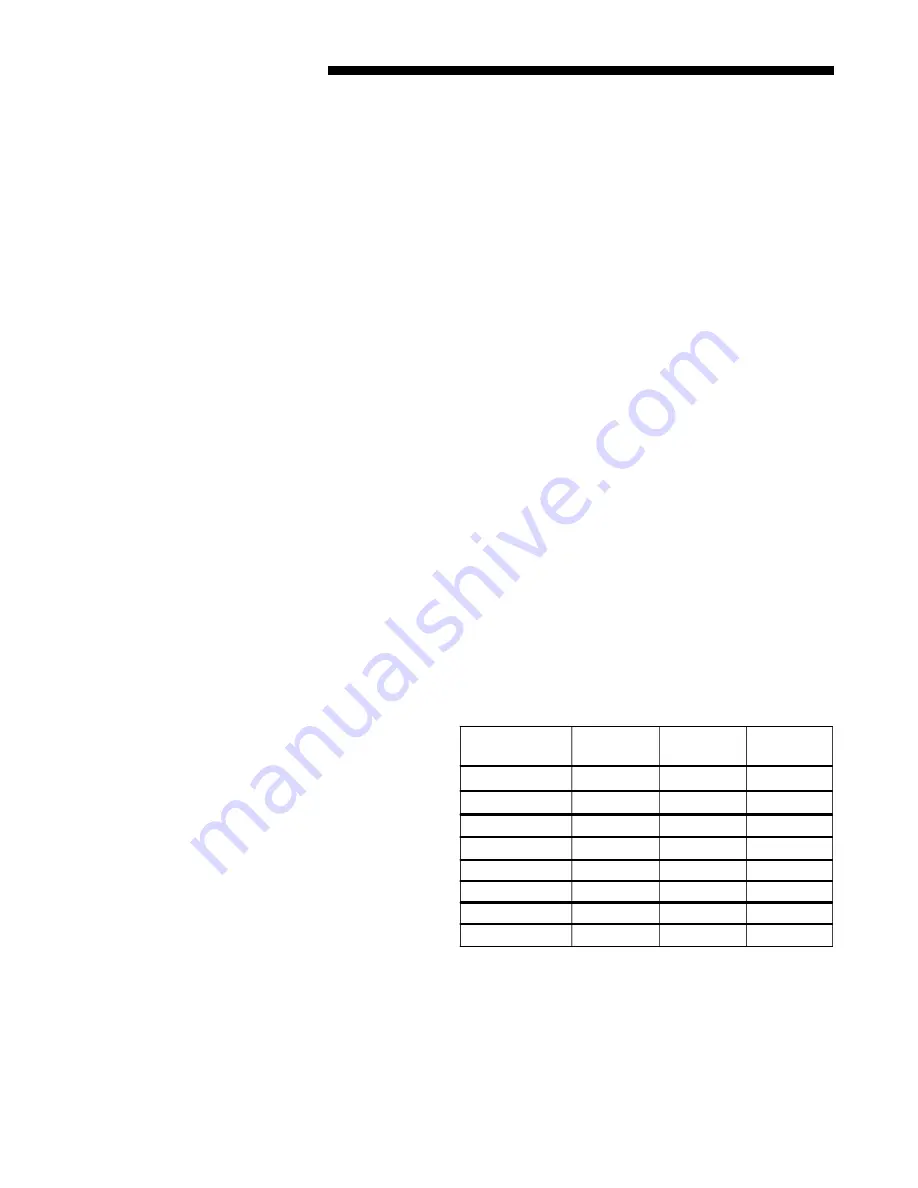
14
Installer’s Guide
minutes after Y is applied.
The liquid temperature set point will not change
during system start-up.
The dip switches should be set prior to initial
application of the Y signal to the Control Module.
The dip switches should be set for each specific
HVAC system based upon the following
instructions:
8c. Determine liquid temperature set point
Reference appropriate high side charging chart
for liquid pressure for cooling units and head
pressure for heat pump units.
Locate the high side pressure for 70 deg F
outdoor temperature at the expected indoor wet
bulb temperature in Table 2. Correct the high
side pressure according to the specific unit being
used. For Heat pumps subtract 7 psi, for cooling
only units subtract 0
(zero) psi. Using the
refrigerant properties chart, find the saturation
temperature for the calculated liquid pressure.
Subtract the anticipated sub-cooling temperature
(typically 12 degrees) from the saturation
temperature to obtain an estimate of the liquid
temperature. Set S2 dip switch 1, 2 and 3 settings
to the nearest liquid temperature set point in the
table below.
S2 Dip Switch
4:
Off - Automatic Mode
(recommended setting)
On - Manual Mode
8b. Dip Switches (S2)
The Control Module will control a liquid
temperature set point as determined by the dip
switch settings. The dip switch is used:
1. To select either Automatic mode or Manual
Mode operation (S2 dip switch 4 setting).
2. To select the liquid temperature set point (S2
dip switch 1, 2 and 3 settings).
Automatic Mode (S2 dip switch 4 in “Off”
position) - The Control Module determines the
approach temperature
based upon the liquid and
ambient temperature readings. The
approach
temperature
= liquid temperature – ambient
temperature. The approach temperature is
calculated only when the ambient temperature is
in the range of 65 to 75 deg F and the outdoor fan
is on continuously. If the Control Module has not
yet acquired an approach temperature, S2 dip
switch 1, 2 and 3 settings are used for
determining the liquid temperature set point the
same as in Manual Mode. If the Control Module
has acquired an
approach temperature
, then the
liquid temperature set point is determined as
follows:
Liquid Temperature Set Point =
Approach
Temperature
+ 70 deg F
Manual Mode (S2 dip switch 4 in “On” position) -
The S2 dip switch 1,2,3 settings are read by the
Control Module and used to determine the liquid
temperature set point when:
1) Y is first applied,
2) After initial startup mode completion, during
the system control mode and no sooner than six
8. System Setup
The Control Module contains a momentary test
switch (S1) and a 4-position installer selectable
dip switch (S2). Both components are located in
the lower right hand corner of the Control
Module. See Figure 11 on page 10.
8a. Test Switch (S1)
The test switch provides a means of verifying that
the fan motor is under the control of the Low
Ambient Control Module. A "Y" signal must be
present in order to test the control. Depressing the
test switch causes the fan to alternately cycle on
(for 3 seconds) and off (for 3 seconds) for a total
time of 12 seconds. The on / off fan operation may
be observed by watching the fan once the test
function has been invoked or by monitoring the
head pressure using a gauge set. The LED on the
solid state relay should light when voltage is being
applied to the fan motor. Once the 12-second test
period is complete the control resumes normal
control operation.
LIQUID TEMP
SET POINT°F
DIP
SWITCH 1
DIP
SWITCH 2
DIP
SWITCH 3
70 °F
OFF
OFF
OFF
76 °F
OFF
OFF
ON
82 °F
OFF
ON
OFF
88 °F
OFF
ON
ON
94 °F
ON
OFF
OFF
100 °F
ON
OFF
ON
106 °F
ON
ON
OFF
112 °F
ON
ON
ON
Table 2. Liquid Temperature Set Point
8d. LEDs
The Control Module contains two LEDs, one
green and one red surface mount. See Figure 11
on page 10. The green LED is a status indicator
labeled Lite Port on the Control Module and
flashes at a ½ second on (plus fast blink at the
end for lite port data) and ½ second off rate in
the cooling mode. In the heating mode the green