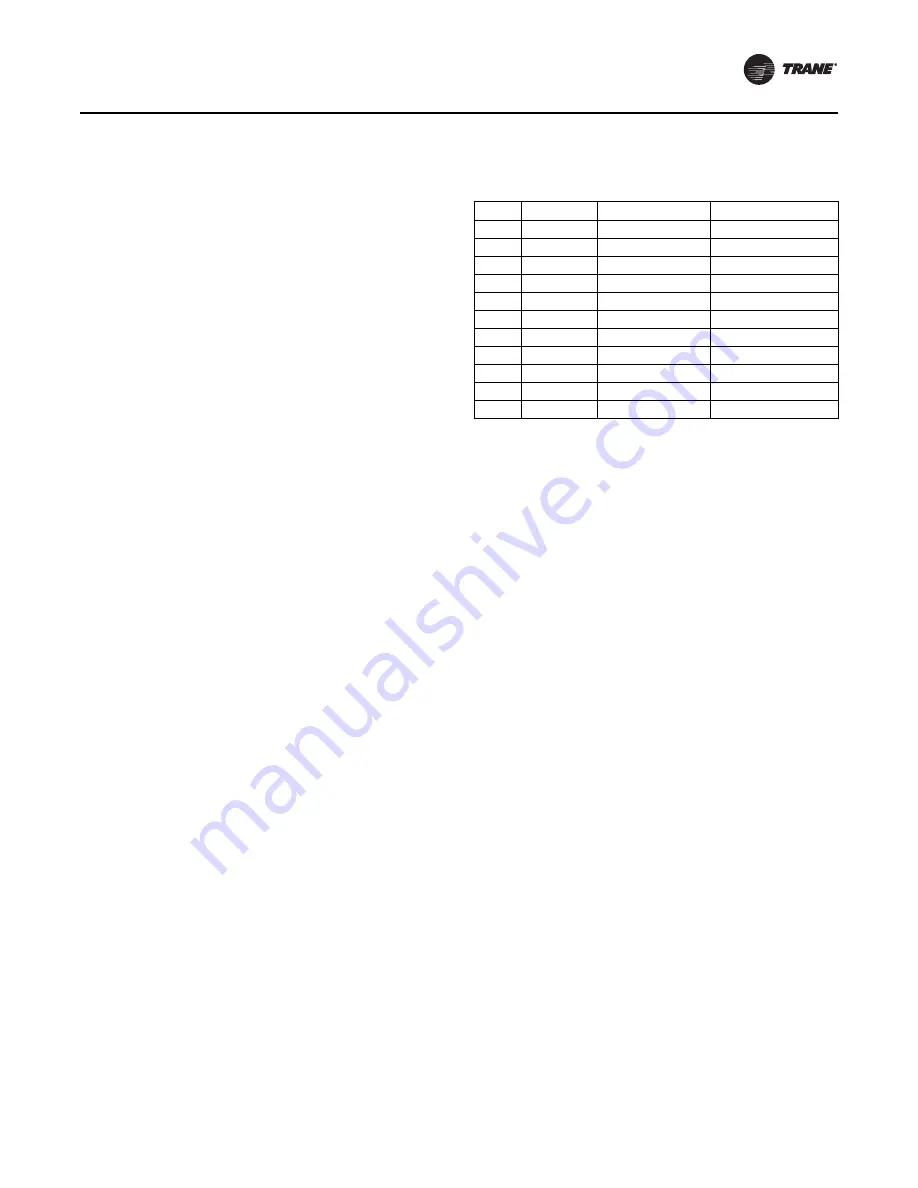
AFDG/AFDU Startup Procedure
AFDG-SVU01L-EN
35
Note:
If the set values do not match, contact the
local Trane Service agency first, or, the
La Crosse Business Unit Technical Service
Department. The correct values are listed
on the unit nameplate shipped with each
unit.
5. In order to view the AFDG/AFDU configurable settings,
go to the Chiller Configuration tab in the Tracer® TU
service tool and select the AFD expanding section.
6. If the drive LLID is not found or if it is necessary to re-
bind the drive LLID, follow the procedure below.
a. The drive’s main DC bus must be charged in order
for the drive LLID to be recognized or bound. Close
the drive disconnect and apply line power to the
drive.
b. With a laptop connected to the chiller and with
Tracer® TU running, enter the binding view menu
of Tracer® TU and locate the “Starter” LLID in the
menu. Select the “Bind” button for the AFD Starter
LLID.
c. The screen “Is the device alone selected?” displays.
In the AFD, wave magnet on the LLID and light the
“service” LED.
d. On the Tracer® TU screen, select the “yes” button
to indicate the LLID has been selected.
e. When properly bound, exit the binding view.
f. Perform any remaining startup items.
7. When ready, start the drive from the Tracer®
AdaptiView™ display.
8. Check the AFDG/AFDU chiller drive response to the
UC800. Initially, the drive will go to 38 hertz and stay
there until the CenTraVac™ chiller vanes open based
on load. The drive will change the speed from there
based on load demand.
9. Document all information on the Startup log.
Drive Settings
Set the values in the order shown in
based on
information obtained from the chiller nameplate.
For additional information, refer to the programming
manual that is shipped with the drive. The programming
manual includes a detailed section that discusses
accessing the parameters in the drive.
This process is summarized briefly below:
1. To access the parameters, press the
Main Menu
key.
2. If required, enter the password (
999
).
3. To select a parameter group, use the up/down arrow
keys to highlight the parameter group, and then press
the
Enter
key to access that group.
4. Use the up/down arrow keys to access the parameter
number, and then press the
OK
key.
5. Use the up/down arrow keys to change the parameter,
and then press the
OK
key to change the setting.
Table 10. Job specific settings
Group Parameter Description
Value
1
20
Motor kW
Set to nameplate CPKW
1
22
Motor voltage
Nameplate voltage
1
24
Motor current
Set to nameplate TVA
1
25
Motor nominal speed Set to nameplate TRPM
1
30
Stator resistance
Set to nameplate SRES
1
35
Main reactance
Set to nameplate MGRE
4
16
Torque limit mode
Set to maximum
4
18
Current limit
Set to maximum
8
(a)
(a) If the customer is connecting to the remote-mounted AFDG with MOD-
BUS®, Group 8 parameters MUST be selected.
01
Control site
1
02
Control word source 0
53
Start select
0
6. If the chiller does not start, re-enter the motor kW,
voltage, and current. The stator resistance and main
reactance values will change based on the motor table
look up that is built into the drive.
If the motor still will
not start,
then perform an AMA (the AMA will
physically measure the stator resistance and main
reactance values, including the connecting cables
between the drive and the motor; the values will then
be set in the drive when the AMA is complete).
To perform an AMA:
a. Change the following parameters:
•
0-40 Hand on key; set to enable.
•
0-41 Off key; set to enable.
•
5-12 Terminal 27 digital input; set to 0, no
function.
b. Go to parameter 1-29 automatic motor adaptation
(AMA) and enter 1 to enable complete AMA.
c. Press the hand key “on” to start the AMA. The
display should now begin to show the steps
completing; there are approximately 16 steps that
need to be completed. If the drive displays an Alarm
53, change the motor voltage value in parameter
1-22 (for example, change from 460 volt to 480 volt
or visa versa) and then try running the AMA again.
d. After the AMA is finished, the display will read
“Press OK to finish AMA.” Press
OK
.
Important:
After the AMA is finished, set parameters
0-40, 0-41, 5-12, and 1-29 back to their
original settings.
7. If the drive is still having difficulty starting the motor, it
may be necessary to perform a reset on the drive; this
procedure will reset the drive parameters back to the
original Danfoss defaults. After this has been
completed, first set the parameters in
and
then set the values in