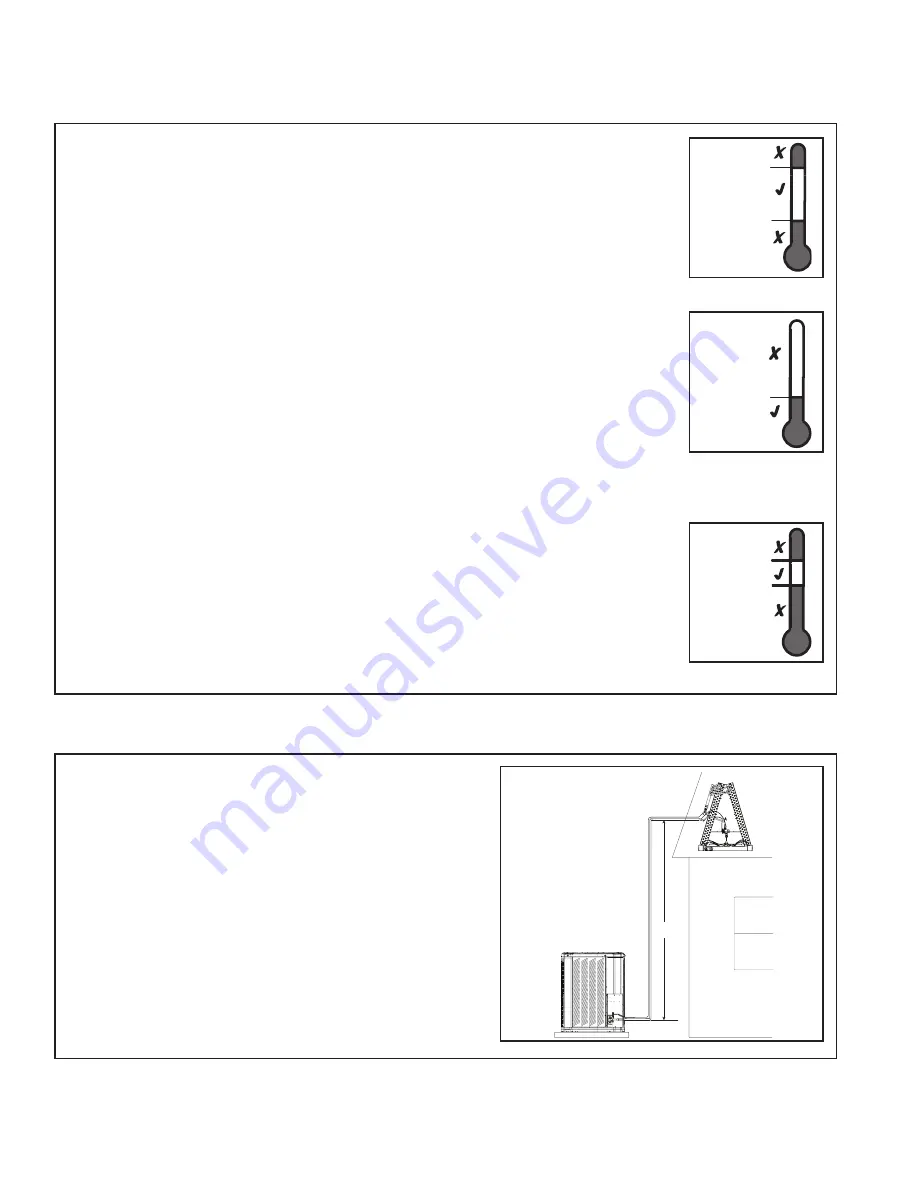
18
18-BC77D1-6
STEP 1 - Check the outdoor temperatures.
Subcooling (in cooling mode) is the only recom-
mended method of charging above 55º F ambi-
ent outdoor temperature. See Section 14.2.
For outdoor temperatures below 55º F, see Sec-
tion 14.3.
Note:
It is important to return in the spring or
summer to accurately charge the system in the
cooling mode when outdoor ambient tempera-
ture is above 55º F.
For best results the indoor temperature should
be kept between 70º F to 80º F.
STEP 1 - Use the refrigerant line total length
and lift measurements from Section 5.3.
Total Line Length = __________ Ft.
Vertical Change (Lift) = __________ Ft.
Section 14. System Charge Adjustment
14.1 Temperature Measurements
14.2 Subcooling Charging in Cooling (Above 55º F Outdoor Temp.)
LIFT
Indoor Temp
80º F
70º F
Outdoor Temp 1
55º F
120º F
Outdoor Temp 2
See Section 14.3 for
Outdoor
Temperatures
Below 55º F
See Section 14.2 for
Outdoor
Temperatures
Above 55º F
55º F