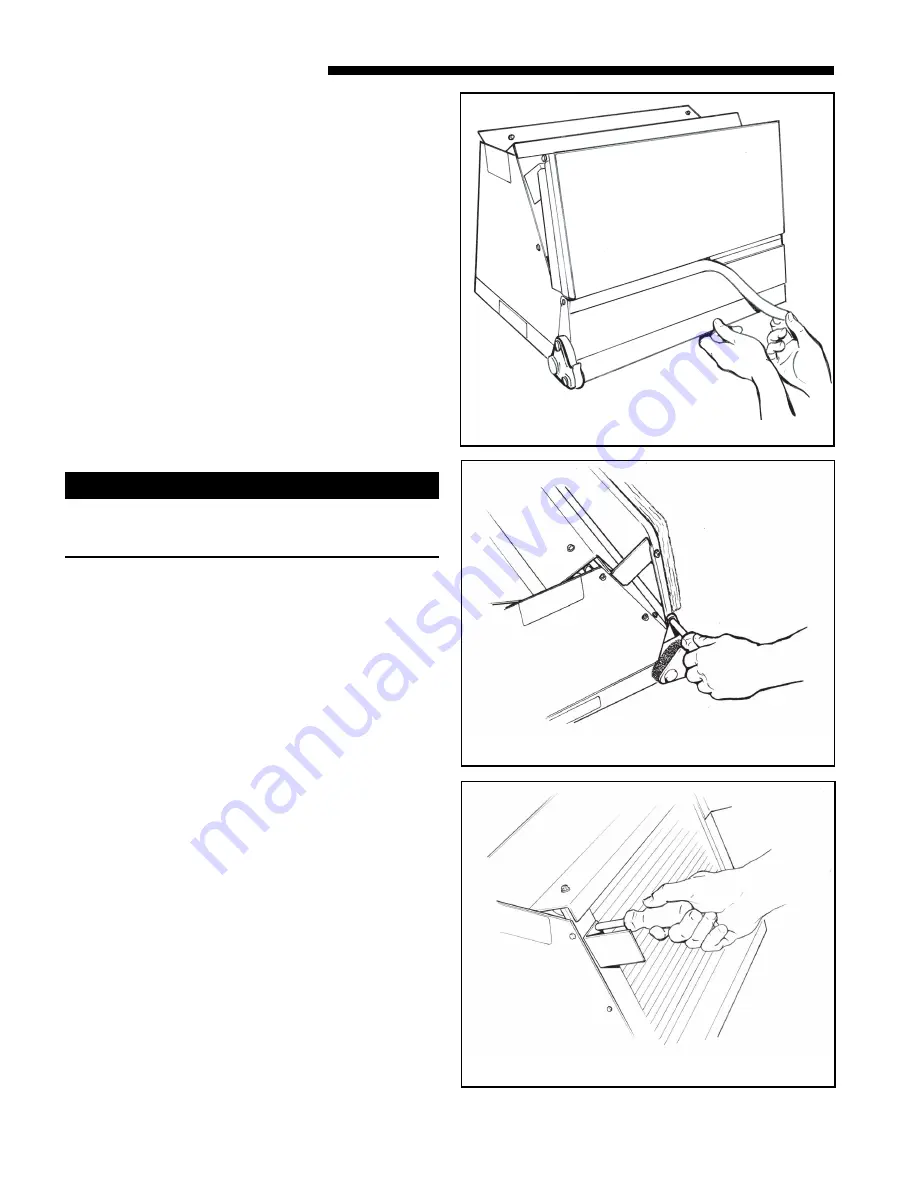
4
18-GE12D1-8
Installer’s Guide
C. UNIT INSTALLATION
UPFLOW
a.
For maximum efficiency
, the horizontal drip
tray should be removed. See Figures 5, 6 and 7.
Tray removal requires that the coil be removed
by sliding the coil out on the coil channel sup-
ports. There is a coil support tab at the top of the
coil connected to the case must be removed first.
Remove 1 inch insulation strip covering the lip of
the drip tray. The tray is detached by removing
the two screws at the drain pan. Remove the two
screws holding the two brackets at the top of the
coil. Remove drip tray by gently breaking the
seal between the drip tray and drain pan.
b. Remove the factory installed baffle assembly
from the apex of the coil by using a 5/16"
nutdriver to remove the screw. Replace this
baffle with the factory supplied narrow coil baffle
using the screws removed previously. See Figure
8. Reinstall coil assembly.
▲
CAUTION
!
When installing the narrow coil baffle, make sure to
align the baffle up with the holes so NOT to puncture
the coil tubing.
c. Position unit on Pedestal or other suitable foun-
dation. If Pedestal is not used, a frame strong
enough to support the total weight must be pro-
vided. Provide a minimum height of 14 inches for
proper unrestricted airflow.
d. If a return air duct is connected to the air han-
dler, it must be the same dimensions as shown in
the outline drawing on page 14.
e. Pedestal and unit should be isolated from the
foundation using a suitable isolating material.
f.
Openings where field wiring enters the
cabinet must be completely sealed.
Location
of power entry is shown on the Outline Drawing.
Use 2.5" clear stickers provided to seal all unused
electrical knockouts. See Figure 13.
g. After ductwork connections are made, seal air-
tight and per Local codes.
DOWNFLOW
a.
For maximum efficiency
, the horizontal drip
tray should be removed. See the Downflow Kit
Installer's Guide 18-GJ23D1-1 for complete in-
structions.
b. If a return duct is connected to the air handler, it
must be the same dimensions as the return
opening shown in the outline drawing on page
15.
Figure 5 Drip Pan Foam Removal
Figure 6 Horitzontal Drip Pan Removal
Figure 7 Drip Pan Bracket Removal