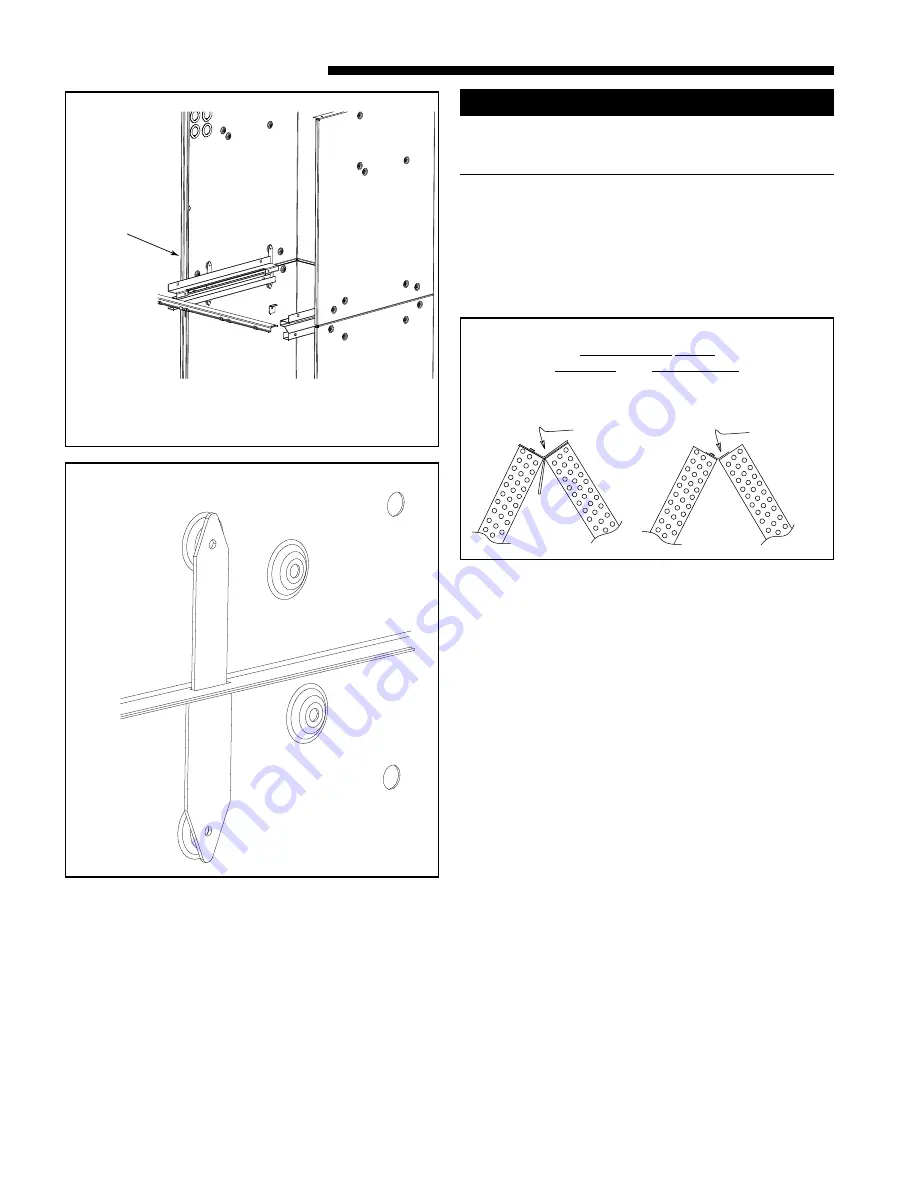
© 2008 Trane
4
18-GE08D1-6
Installer’s Guide
top of the coil. Remove the two screws holding
the two brackets at the top of the coil. Remove
drip tray by gently breaking the seal between the
drip tray and drain pan.
b. Remove the factory installed baffle assembly
from the apex of the coil by using a 5/16"
nutdriver to remove the screws. Replace this
baffle with the factory supplied narrow coil
baffle using the screws removed previously
(See Figure 5). Reinstall coil assembly.
▲
CAUTION
!
When installing the narrow coil baffle, make sure to
align the baffle up with the holes so NOT to puncture
the coil tubing.
c. Position unit on Pedestal or other suitable foun-
dation. If Pedestal is not used, a frame strong
enough to support the total weight must be pro-
vided. Provide a minimum height of 14 inches for
proper unrestricted airflow.
d. If a return air duct is connected to the air han-
dler, it must be the same dimensions as shown in
the outline drawing.
e. On units with sheetmetal returns: Return ple-
num should be flanged. Sheetmetal screws must
be 1/2" in length or shorter.
f. No sheetmetal screws may be used to attach re-
turn duct work on the side of the unit.
g. Pedestal and unit should be isolated from the
foundation using a suitable isolating material.
h.
Openings where field wiring enters the
cabinet must be completely sealed.
Location
of power entry is shown on the outline drawing.
Use 2.5" clear stickers to seal all unused electri-
cal knockouts. See Figure 11.
i. After ductwork connections are made, seal air-
tight and per local codes.
DOWNFLOW
a.
For maximum efficiency
, the horizontal drip
tray should be removed. See Figures 6, 7 and
8. Tray removal requires that the coil be re-
moved by sliding the coil out on the coil chan-
nel supports. The tray is detached by removing
the two screws at the drain pan and the two
screws holding the two brackets at the top of
2 PIECE WRAPPER SPEAR
4
Remove
and
Discard
Replace
with
Narrow
Baffle
FOR MAXIMUM EFFICIENCY ON
HORIZONTAL LEFT,
UPFLOW AND DOWNFLOW
5
CLOSEUP OF SPEAR LOCATIONS
3
1
2
3
4
SCREWS 5-8
LOCATED ON
LEFT SIDE