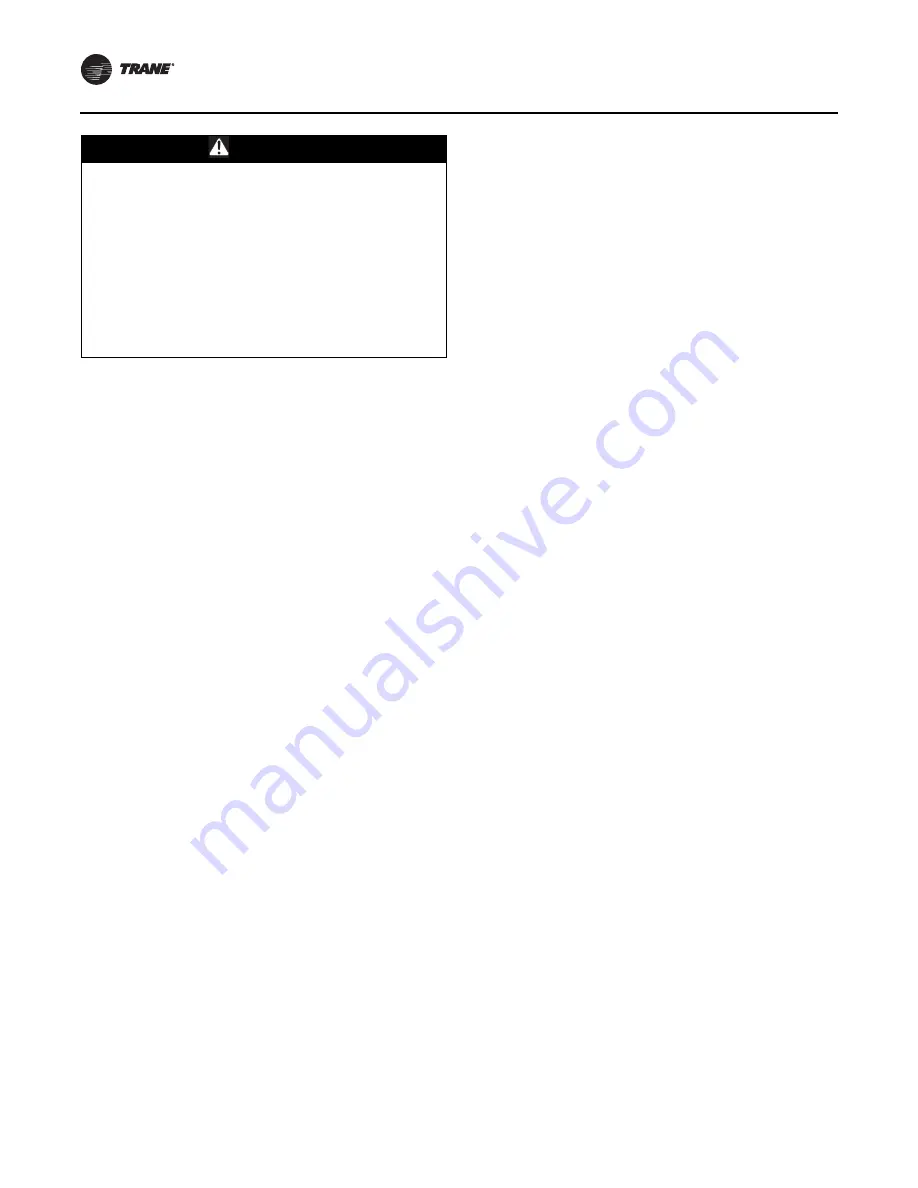
General Information
10
COM-SVN003B-EN
Mechanical Failure
Replace only the failed compressor in a tandem or trio set.
Important:
On tandem or trio assemblies, the suction
and discharge lines must NOT be modified,
except for the use of slip joint couplings.
Other modification may cause oil return
issues and lead to compressor failure. Cut
the lines in a convenient place, remove the
compressor, and then unbraze the lines
from the compressor. On re-installation,
reinstall lines to compressor and
reassemble the cut lines utilizing a slip
coupling.
Minimize system and compressor open times to avoid
excessive moisture absorption by the POE oil. Maximum
suggested open time is 15 minutes.
Drain and replace oil in all the non-failed compressors.
The CSHW compressor has an oil drain with a Schrader
®
valve that can be used to remove the oil (see
Replace unit liquid line filter-drier. This is a very important
part of controlling moisture in R-410A POE oil systems.
Reuse the compressors mounting isolators or mounting
spacers that are used with the existing compressor
assembly.
Braze the compressor into the system. Compressor
connections are copper-plated steel. Use BAg-28, 40%
silver, with paste flux to make the copper tube connections
to the compressor.
Proceed with the following as described in the following
sections:
•
•
“Vacuum Testing and Evacuation,” p. 15
•
•
“Verification Before Start-Up,” p. 16
Electrical Failure
Follow the mechanical failure guidelines. In addition to the
Mechanical Failure Guidelines, check for acid in the
system.
Test the acid condition of the oil in the compressors using
an acid test kit. Use Trane Part Numbers CHM00414 and
45006.
Two Types of Motor Failures
Light
- If oil test kit is negative and oil is only slightly
discolored, treat in the same manner as a mechanical
failure.
Severe
- If oil test kit is positive with strong pungent odor
and dark oil, drain and replace oil in all of the non-failed
compressors.
Reuse the compressor mounting isolators or mounting
spacers that are used with the existing compressor
assembly.
This type of failure requires changing both the suction and
liquid line filter-driers. Use replaceable filter-drier cores to
facilitate changing filter-driers, if required.
Install the suction filters no closer than the distance listed
in the following table. The distance is measured from the
centerline of the suction inlet tee.
1. Use acid removal type filter-drier cores in both the
suction filter and liquid line filter drier.
2. Change when the pressure drop exceeds 4 psig.
Test oil after 24 hours of operation. Change filter-drier
again if required. If oil is still acid, drain and replace oil in
all the non-failed compressors.
After system is clean, test kit indicates okay, remove the
suction clean up filter-drier and replace the liquid line drier
with standard filter drier cores.
WARNING
Hazard of Explosion!
Failure to follow instructions below could result in
death or serious injury or equipment or property-only
damage. Use only dry nitrogen with a pressure
regulator for pressurizing unit. Do not use acetylene,
oxygen or compressed air or mixtures containing them
for pressure testing. Do not use mixtures of a hydrogen
containing refrigerant and air above atmospheric
pressure for pressure testing as they may become
flammable and could result in an explosion. Refrigerant,
when used as a trace gas should only be mixed with dry
nitrogen for pressurizing units.