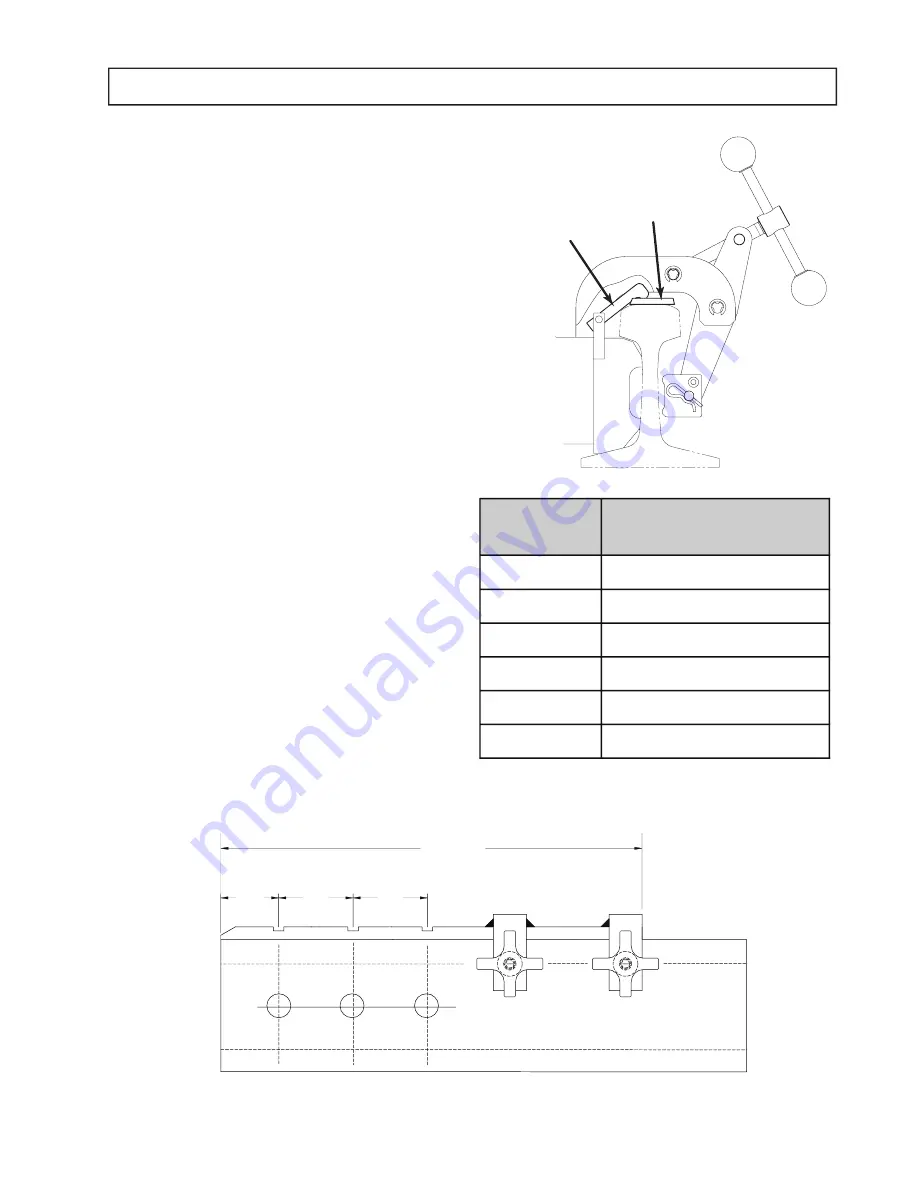
Positioning of Optional Hole Location Template
Template is positioned on head of rail with tapered tip fl ush
with end of rail and side locking screws fastened to rail
head. Notches in template give precise location of hole
centerlines to be drilled.
The rail clamp assembly has a locating arm which rests
in the template notches. The locating arm is adjustable to
accommodate the full range of rail sizes.
To use the locating arm, raise the drill unit over the rail with
the template attached and gently rest drill down until shoes
make contact with the rail. Flip the arm to make contact
with the template. Slowly slide drill across the template
until the arm falls into notch.
The arm must contact the sides of the matching notch.
Following the Clamping Instructions, clamp unit onto rail.
When the hole is completed, raise the arm by fl ipping the
arm back toward the body of the drill. Before drilling next
hole remove chips around cutter. Then move the drill side-
ways, ensuring the arm is clear of the notch, and fl ip arm
down. Slide the drill sideways until arm falls in the next
notch, and repeat the procedure as necessary.
Note: The locating arm must be fl ipped back, resting
on the body of the drill before putting the drill unit on
the rail. Failure to do so can result in damage to the
hole locating arm system.
Hole location templates are offered as optional equipment.
Four of these templates are provided with established hole
spacings. The 40570 template is produced to customer
specifi ed hole spacing. See chart for the template to match
your application.
8
Template
Part No.
Hole Spacing
40570
Customer Specified
40701
3-1/2" X 6" X 6"
40702
2-11/16" X 5-1/2" X 5-1/2"
40703
2-1/2" X 5" x 5"
40704
2-1/2" X 6-1/2" X 6-1/2"
40706
2- 23/32" x 5-1/2" x 5-1/2"
Locating Arm
Location Template
28-1/2"
"A"
"B"
"C"
Specify “A”, “B”, “C” when ordering custom template
Custom Template Spacing