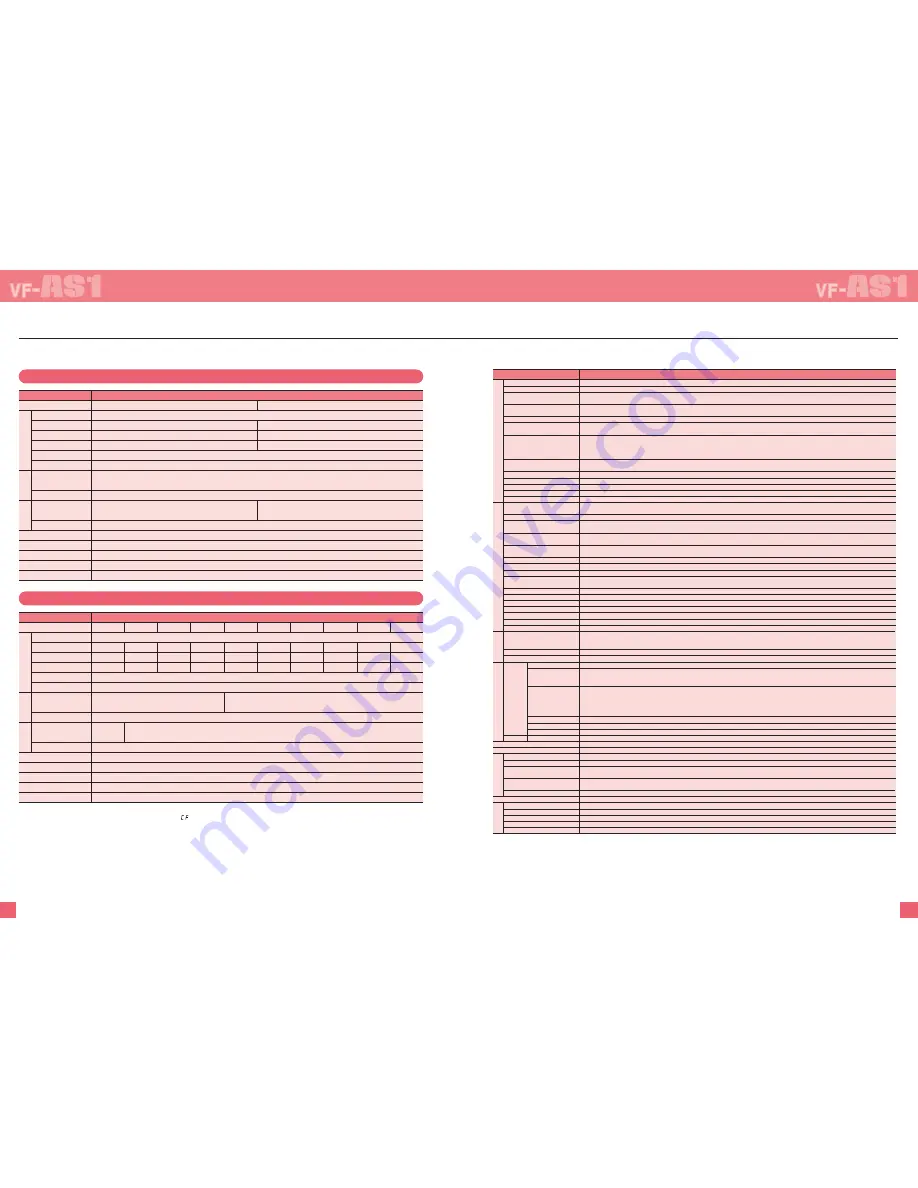
11
12
■
Standard specifications (200 V class -55 to 75 kW, 400 V class -90 to 500 kW model)
■
Common Specifications
200 V class
400 V class
Note 1) Capacity is calculated at 220V for the 200V models and at 440V for the 400V models.
Note 2) Indicates the value when the PWM carrier frequency (parameter ) is 2.5 kHz or less.
When low noise (PWM carrier frequency 8 kHz) is required at 18.5 kW or more, use an inverter of capacity one rank higher than the motor capacity.
Note 3)
±
10% when the inverter is used continuously (load of 100%)
Note 4) Inverters, 18.5kW or greater, do not have wiring port covers. They have large openings, but there is no space to bend the external cables inside the unit. If they are fitted
external to the cabinet, please use an optional wiring port cover.
Note 5) For 200V-55kW, 400V-90kW or larger model, be sure to install DC reactor.
However, this is unnecessary for DC input specifications.
Note 6) Three-phase 380~480V-50/60Hz for 4900PC
Note 7) Complies with the European EMC Directive
IEC/EN61800-3, 2nd environment, category C3
Item
Specification
Applicable Motor (kW)
Type
Form
Output Capacity (kVA)
Note 1)
Output Current (A)
Note 2)
Output Voltage
Overload Current Rating
Dynamic
Braking Circuit
Dynamic Breaking Resistor
Voltage/frequency
Allowable Fluctuation
Protective method
Cooling method
Color
Built-in Filter
DC Reactor
VFAS1–
3-phase, 200 to 240 V (The maximum output voltage is the same as the input voltage.)
150%–1 minute, 165%–2 seconds
Built-in
Compatible with external options
V10% – 15%
Note 3)
Frequency
±
5%
IP20 enclosed type (JEM1030)
Note 4)
Forced air cooling
RAL7016
External filter (optional)
Attached DC reactor
Note 5)
55
2550P
84
221
75
2750P
109
285
3-phase, 200 to 240 V – 50/60 Hz
3-phase, 200 to 220 V – 50 Hz
3-phase, 200 to 240 V – 60 Hz
Item
Specification
Applicable Motor (kW)
Type
Form
Output Capacity (kVA)
Note 1)
Output Current (A)
Note 2)
Output Voltage
Overload Current Rating
Dynamic
Braking Circuit
Dynamic Breaking Resistor
Voltage/frequency
Allowable Fluctuation
Protective method
Cooling method
Color
Built-in Filter
DC Reactor
90
4900PC
136
179
110
4110KPC
164
215
132
4132KPC
197
259
160
4160KPC
239
314
200
4200KPC
295
387
220
4220KPC
325
427
280
4280KPC
419
550
355
4355KPC
511
671
400
4400KPC
578
759
500
4500KPC
717
941
VFAS1–
3-phase, 380 to 480 V (The maximum output voltage is the same as the input voltage.)
150%–1 minute, 165%–2 seconds
Compatible with external options
3-phase, 380 to 440 V – 50 Hz
3-phase, 380 to 480 V – 60 Hz
V10% – 15%
Note 3)
Frequency
±
5%
IP20 enclosed type (JEM1030)
Note 4)
Forced air cooling
RAL7016
EMI noise filter
Note 7)
Attached DC reactor
Note 5)
Built-in
Compatible with external options
Note 6)
Standard specifications
Rating
Po
w
e
r
Supply
Electr
ic
Br
aking
Rating
Po
w
e
r
Supply
Electr
ic
Br
aking
Item
Specification
Control specifications
Oper
ation specifications
Protectiv
e
function
Displa
y
functions
Output signal
En
vironments
Note 1: 16 contact input terminals (of which 8 are options) are programmable contact input terminals, and they make it possible to arbitrarily select from 136 types of signals.
Note 2: Programmable ON/OFF output terminals make it possible to arbitrarily select from 150 types of signals.
Note 3: Programmable analog output terminals make it possible to arbitrarily select from 55 types of signals.
Note 4: When using inverters where the ambient temperature will rise above 50
°
C, remove the upper cover and operate each inverter at a current lower than the rated one.
Note 5: This function protects inverters from overcurrent due to output circuit ground fault.
4-digit and
7-segment
LED
Sinusoidal PWM control
LED
Main circuit voltage feedback control. (Switchable between automatic adjustment/fix/control off)
Setting between 0.01 to 500Hz. Default max. frequency is set to 0.01 to 60Hz.
Maximum frequency adjustment (30 to 500Hz)
0.01Hz: operation panel input (60Hz base),
0.02Hz: analog input (60Hz base, 11 bit/0 to 10Vdc)
Within
±
0.2% (25
°
C
±
10
°
C): analog input
±
0.01% (25
°
C
±
10
°
C): digital input
V/f constant, square reduction torque control, automatic torque boost, vector calculation control, base frequency adjustment 1, 2, 3, and 4 (25 to 500Hz), V/F 5-point arbitrary setting,
torque boost adjustment (0 to 30%), start frequency adjustment (0 to 10Hz), stop frequency adjustment (0 to 30Hz)
3k
Ω
potentiometer (possible to connect to 1 to 10k
Ω
-rated potentiometer)
0 to 10Vdc (input impedance Zin: 30k
Ω
)
0 to
±
10Vdc (Zin: 22k
Ω
)
4 to 20mAdc (Zin:242
Ω
)
The characteristic can be set arbitrarily by two-point setting. Compliant with 6 types of input; analog input (RR, VI/II, RX, RX2), pulse input and binary/BCD input (*RX2, binary/BCD
input: optional)
3 places. Setting of jump frequency and width.
Upper limit frequency: 0 to max. frequency, lower limit frequency: 0 to upper limit frequency
Adjustment of proportional gain, integral time, differential time and delay filter
200V-45kW or less, adjustable between 1.0 to 16kHz for 400V-75kW or less200V-55kW or less, adjustable between 1.0 to 8kHz for 400V-90kW or more
Voltage command input specification: DC 0 to
±
10V
0.01 to 6000 sec. Selectable from among acceleration/deceleration. times 1, 2, 3 and 4. Automatic acceleration/deceleration function. S-pattern acceleration/deceleration 1 and 2
pattern adjustable.
Adjustment of braking start frequency (0 to 120Hz), braking (0 to 100%) and braking time (0 to 10 sec.). With emergency stop braking function and motor shaft fix control function.
With F-CC closed to forward run, with R-CC closed to reverse run, with both closed to reverse run. With ST-CC opened to coast stop. Emergency stop by panel operation or terminal
board.
Jog mode, if selected, allows jog operation from the operation panel
Jog run operation by terminal board is possible by setting the parameters.
By changing the combination of open/close between S1, S2, S3, RR/S4-CC, set fre 15-speed operation.
Selectable between acceleration/deceleration time, torque limit and V/f by set frequency.
Capable of restarting after a check of the main circuit elements in case the protective function is activated. Max. 10 times selectable arbitrarily. Waiting time adjustment (0 to 10 sec.)
The cooling fan will be stopped automatically to assure long life when unnecessary.
Possible to keep the motor running using its regenerative energy in case of a momentary power failure. (Default: OFF)
Possible to select each 8 patterns in 2 groups from 15-speed operation frequency. Max. 16 types of operation possible. Terminal board operation/repeat operation possible.
Possible to switch operation by commercial power source or inverter
Increases the operating efficiency of the machine by increasing the rotational speed of the motor when it is operated under light load.
When two or more inverters are used to operate a single load, this function prevents load from concentrating on one inverter due to unbalance.
External input signal adjustment is possible to the operation frequency command value.
Switchable between standard motor/constant torque VF motor, adjustment of overload protection and stall prevention level.
Reset by 1a contact closed (or 1b contact opened), or by operation panel. Or power source OFF/ON. This function is also used to save and clear trip records.
Stall prevention, current limit, overcurrent, overvoltage, short circuit on the load side, ground fault on the load side (Note 5), undervoltage, momentary power failure (15ms or more),
non-stop control at momentary power failure, overload protection, arm overload at starting, overcurrent on the load side at starting, overcurrent and overload at dynamic braking
resistance, fin overheat, emergency stop
Key prohibition selectable between Stop key only, Mode key only, etc. All key operations can be prohibited.
Automatic load reduction control at overloading. (Default: OFF)
Possible to restart the motor in coasting in accordance with its speed and direction. (Default: OFF)
Control system
Output voltage adjustment
Output frequency range
Minimum setting steps of frequency
Frequency accuracy
Voltage/frequency characteristics
Frequency setting signal
Terminal board base frequency
Frequency jump
Upper and lower limit frequencies
PWM carrier frequency
Torque control
DC braking
Forward run/reverse run Note 1)
Jog run Note 1)
Preset speed operation Note 1)
Retry
Soft stall
Cooling fan ON/OFF
Operation panel key operation ON/OFF
control
Regenerative power ride-through control
Auto-restart operation
Simplified pattern operation
Commercial inverter switching
Light-load high-speed operation
Drooping function
Override function
Protective function
Electronic thermal characteristic
Reset
Acceleration/deceleration time
PID control
Input/output terminal input function
Sink/source switching
Failure detection signal
Low speed/speed reach signal output Note 2)
Upper/lower limit frequency signal output
Note 2)
Output for frequency meter/output for ammeter
Note 3)
Pulse train frequency output
Communication function
Operating environments
Ambient temperature
Vibration
Storage temperature
Relative humidity
Stall prevention during operation, overload limit, overload, undervoltage on power source side, DC circuit undervoltage, setting error, in retry, upper limit, lower limit.
Overcurrent, overvoltage, fin overheat, short circuit on the load side, ground fault on the load side, inverter overload, arm overcurrent at starting, overcurrent on the load side at starting,
EEPROM error, RAM error, ROM error, transmission error, (dynamic braking resistor overcurrent/overload), (emergency stop), (undervoltage), (low current), (overtorque), (motor
overload), (output phase failure) The items in the parentheses are selectable.
Operation frequency, operation frequency command, forward run/reverse run, output current, DC voltage, output voltage, compensated frequency, terminal board input/output
information, CPU version, control EEPROM version, past trip history, cumulative operation time, speed feedback, torque, torque command, torque current, exiting current,
PID feedback value, motor overload factor, inverter overload factor, PBR overload factor, PVBR load factor, input power, output power, peak output current, peak DC voltage,
Motor counter pseudo PG, position pulse, RR input, VI/II input, RX input, RX2 input, FM output, AM output, meter adjustment fix output, flash memory version, main circuit
EEPROM version, types of connection option, previous default setting, previous automatic control (AU2)
Display of optional units other than output frequency (motor speed, line speed, etc), current ampere/% switch, voltage volt/% switch
Searches automatically parameters that are different from the standard default setting parameters. Easy to find changed parameters.
User parameter settings can be saved as default settings. Allows to reset the parameters to the user-defined parameter settings.
Displays main circuit capacitor charging.
Possible to select positive logic or negative logic with programmable input/output terminal function menu. Note 1: Note 2: (Default setting: positive logic)
Possible to switch between minus common (CC) and plus common (P24) for control terminal. (Default setting: minus common (CC))
1c contact output (250Vac-2A-cosØ=1, 250Vac-1A-cosØ=0.4, 30Vdc-1A)
Open collector output (24Vdc, max. 50mA, output impedance: 33
Ω
)
Open collector output (24Vdc, max. 50mA, output impedance: 33
Ω
)
Analog output. 1mAdc full-scale DC ammeter or 7.7Vdc-1mA voltmeter
Open collector output (24Vdc, max. 50mA)
RS-485 standard 2-channel equipped (connector: modular 8P)CC-Link, DeviceNet and PROFIBUS-DP are optional.
Indoor use. Altitude: 3000m or less (current reduction necessary if 1000m or more.) Place not exposed to direct sunlight and free of corrosive and explosive gases.
-10 to +60
°
C (Remove the upper cover if 40
°
C or more, max. 60
°
C) Note 4:
-25 to +65
°
C
20 to 93% (free from condensation)
5.9m/s
2
{0.6G} or less (10 to 55Hz) (Compliant with JIS C0040)
Causes of failures
Free unit display
Alarms
Charge display
User default setting
Automatic edit function
Monitoring function