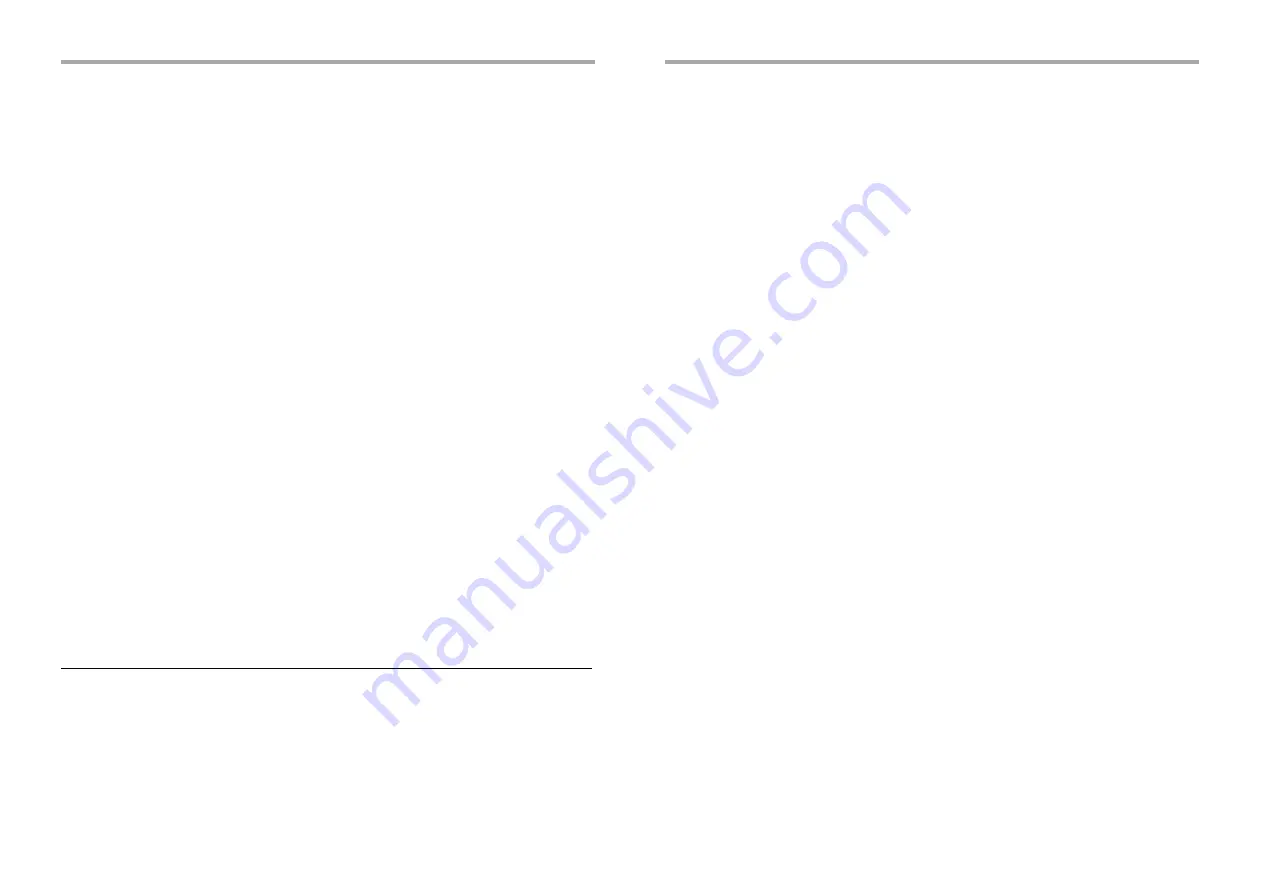
– 7 –
19.Recovery
• When removing refrigerant from a system, either for servicing or decommissioning, it is
recommended good practice that all refrigerants are removed safely.
• When transferring refrigerant into cylinders, ensure that only appropriate refrigerant
recovery cylinders are employed.
• Ensure that the correct number of cylinders for holding the total system charge are
available.
• All cylinders to be used are designated for the recovered refrigerant and labelled for that
refrigerant (i.e. special cylinders for the recovery of refrigerant).
• Cylinders shall be complete with pressure-relief valve and associated shut-off valves in
good working order.
• Empty recovery cylinders are evacuated and, if possible, cooled before recovery
occurs.
• The recovery equipment shall be in good working order with a set of instructions
concerning the equipment that is at hand and shall be suitable for the recovery of all
appropriated refrigerants.
• In addition, a set of calibrated weighing scales shall be available and in good working
order.
• Hoses shall be complete with leak-free disconnect couplings and in good condition.
• Before using the recovery machine, check that it is in satisfactory working order, has
been properly maintained and that any associated electrical components are sealed to
prevent ignition in the event of a refrigerant release.
• Consult manufacturer if in doubt.
• The recovered refrigerant shall be returned to the refrigerant supplier in the correct
recovery cylinder, and the relevant waste transfer note arranged.
• Do not mix refrigerants in recovery units and especially not in cylinders.
• If compressors or compressor oils are to be removed, ensure that they have been
evacuated to an acceptable level to make certain that flammable refrigerant does not
remain within the lubricant.
• The evacuation process shall be carried out prior to returning the compressor to the
suppliers.
• Only electric heating to the compressor body shall be employed to accelerate this
process.
• When oil is drained from a system, it shall be carried out safely.
2
INSTALLATION OF R32 OR R410A
REFRIGERANT AIR CONDITIONER
This PMV Kit adopts the HFC refrigerant (R32 OR R410A) which does not deplete the ozone layer.
Be sure to read and follow the Installation Manuals for indoor and outdoor units for precautions regarding the
characteristics of the refrigerant, the tools used, and the refrigerant piping. It is different from the conventional
refrigerant (R22).
Refrigerant piping
• Piping material used for the conventional refrigerant cannot be used.
• Use copper pipe with 0.8 mm or more thickness for Dia.6.4, Dia.9.5, Dia.12.7 mm.
• Flare nut and flare works are also different from those of the conventional refrigerant.
Take out the flare nut attached to the unit of the air conditioner, and use it.
13-EN
14-EN