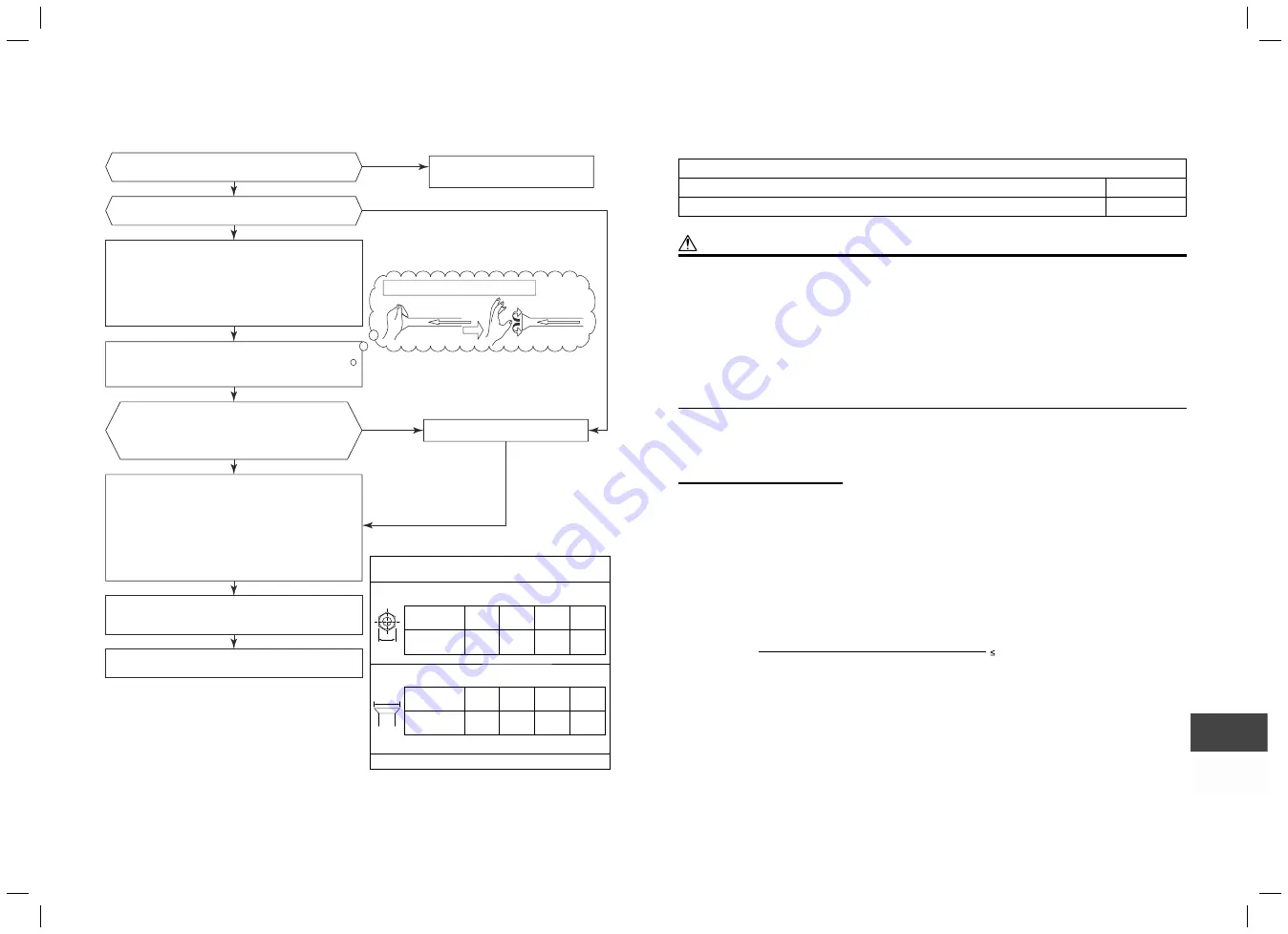
– 18 –
Are there scratches or dents on the existing pipes?
YES
NO
YES
NO
YES
NO
Is it possible to operate the existing air conditioner?
After the existing air conditioner is operated in
cooling mode for approx. 30 minutes or longer,*
recover the refrigerant.
Refer to “13 Refrigerant recovery”
For cleaning the pipes and recovering oil
Refrigerant recovery: Pump down method
Remove the existing air conditioner from the piping
and carry out flushing (nitrogen pressure 0.5 MPa)
to remove any remains inside of the pipe.
Was largely discolored oil or a large quantity of
remains discharged? (When the oil
deteriorates, the color of the oil changes to a
muddy or black color.)
Nitrogen gas pressure 0.5 MPa
Existing pipes: Cannot be used.
Use new pipes.
Clean the pipes or use new pipes.
(If there is discharge of remains, it is judged that a
large quantity of remains are present.)
Connect the indoor / outdoor units to the existing pipe.
Use a flare nut attached to the main unit for the
indoor / outdoor units. (Do not use the flare nut of the
existing pipe.)
Re-machine the flare machining size to size for
R410A.
(Airtight test), Vacuum dry, Refrigerant charge, Gas
leak check
Test run
Piping necessary to change the
nut / machining
size due to pipe compression
1) Flare nut width: H
in (mm)
H
Copper pipe
outer diameter
1/4”
(6.4)
3/8”
(9.5)
1/2”
(12.7)
5/8”
(15.9)
For
R410A
0.67”
(17)
0.87”
(22)
1.02”
(26)
1.14”
(29)
2) Flare machining size: A
in (mm)
A
Copper pipe
outer diameter
1/4”
(6.4)
3/8”
(9.5)
1/2”
(12.7)
5/8”
(15.9)
For
R410A
0.36”
(9.1)
0.52”
(13.2)
0.65”
(16.6)
0.78”
(19.7)
Becomes a little larger for R410A
flare
Do not apply refrigerator oil to the flare surface.
15
Speci
fi
cations
This product contains fluorinated greenhouse gases covered by the Kyoto Protocol
Chemical Name of Gas
R410A
Global Warming Potential (GWP) of Gas
1,975
CAUTION
1. Paste the enclosed refrigerant label adjacent to the charging and/or recovering location.
2. Clearly write the charged refrigerant quantity on the refrigerant label using indelible ink. Then, place the
included transparent protective sheet over the label to prevent the writing from rubbing off.
3. Prevent emission of the contained fluorinated greenhouse gas. Ensure that the fluorinated greenhouse gas is
never vented to the atmosphere during installation, service or disposal. When any leakage of the contained
fluorinated greenhouse gas is detected, the leak shall be stopped and repaired as soon as possible.
4. Only qualified service personnel are allowed to access and service this product.
5. Any handling of the fluorinated greenhouse gas in this product, such as when moving the product or
recharging the gas, shall comply under (EC) Regulation No. 842/2006 on certain fluorinated greenhouse
gases and any relevant local legislation.
6. Periodical inspections for refrigerant leaks may be required depending on European or local legislation.
7. Contact dealers, installers, etc., for any questions.
Warnings on refrigerant leakage
Check of concentration limit
The room in which the air conditioner is to be installed requires a design that in the event of refrigerant
gas leaking out, its concentration will not exceed a set limit.
The refrigerant R410A which is used in the air conditioner is safe, without the toxicity or combustibility of ammonia,
and is not restricted by laws to be imposed which protect the ozone layer. However, since it contains more than
air, it poses the risk of suffocation if its concentration should rise excessively. Suffocation from leakage of R410A
is almost non-existent.
If a conditioner system is to be installed in a small room, select a suitable model and installation procedure so
that if the refrigerant accidentally leaks out, its concentration does not reach the limit (and in the event of an
emergency, measures can be made before injury can occur).
In a room where the concentration may exceed the limit, create an opening with adjacent rooms, or install
mechanical ventilation combined with a gas leak detection device.
The concentration is as given below.
Total amount of refrigerant (kg)
Min. volume of the indoor unit installed room (m
3
)
Concentration limit (kg/m
3
)
The concentration limit of R410A which is used in multi air conditioners is 0.3 kg/m
3
.
EN
TH
ID
35-EN
36-EN
1131601101 EN FR ES.indb 18
1131601101 EN FR ES.indb 18
4/8/2565 BE 10:14
4/8/2565 BE 10:14