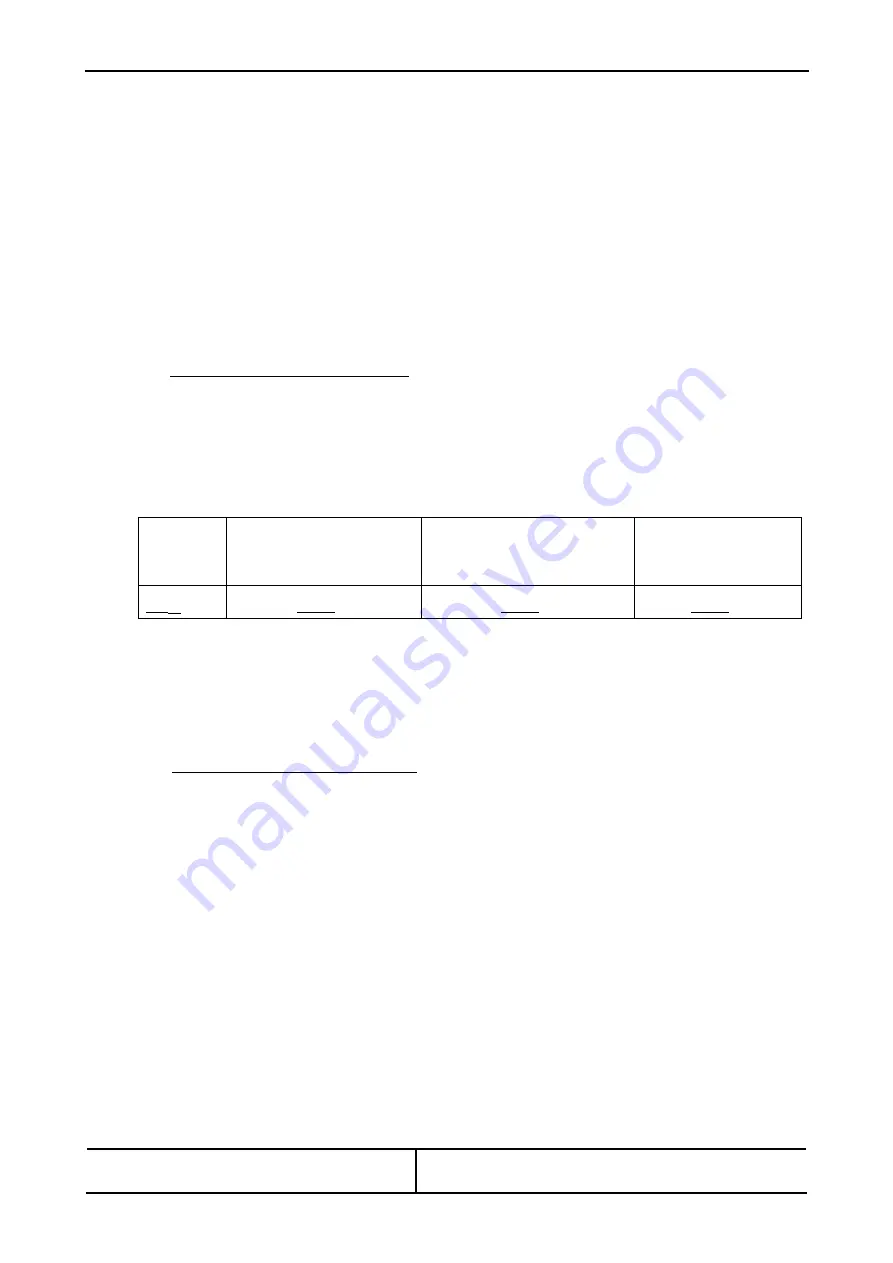
Specification No. TENTATIVE
Sheet
5
Toshiba Matsushita Display Technology Co.,Ltd
Date: 2008 – 11- 07
Date: - -
New No. LTA057A341F-14
Old No.
←
# Special
←&
Addition
←
Change
4) GAS GENERATED FROM THE PART MATERIAL FOR A SET
Some plastic materials and shock absorbing materials (rubber) used in the system may generate gases that may
cause the deterioration of the polarizer laminated on LCD’s panel or internal parts of the LCD module. Prior
confirmation is required.
5) GAS GENERATED FROM CASING /PACKAGING MATERIAL FOR A SET
Some materials used for packaging (for which sulfuric acid is used in the recycling process) generate gases that may
cause the deterioration of the polarizer laminated on LCD’s panel or internal parts of the LCD module. Prior
confirmation is required.
2-2. DESIGNING POWER SUPPLIES AND INPUT SIGNALS TO LCD MODULE
1) CAPACITY OF POWER SUPPLY
The fuse (KAMAYA /Type:FCC16152AB
<
TP
>
) is attached at the power supply line in the LCD module.
The sufficient electric capacity is needed for effective operation of this fuse. As for this fuse, there is no effect in the
former circuit. As an example, some parts such as I/F connector may be damaged with fire and/or smoke when the
power supply is shorted at I/F connector part. Have a suitable protection circuit also in the set side for accident
prevention. In equipping the set side with a fuse, please choose the fuse of suitable specification so that a fuse does
not blow by the rush current at operation start.
Power
Supply
Recommended maximum
output current of
power supply
Recommended Fuse Rating
(in case of using fuse
for current limiter)
Built-in Fuse Rating
(for reference)
V
DD
4.0 A
1.5 A
1.5 A
2) SEQUENCE OF POWER SUPPLIES AND INPUT SIGNALS
Power-supply lines should be designed as follows.
Power supplies should always be turned on before the input signals are supplied to LCD module, and the input
signals should be disconnected before power supplies are turned off.
If this sequence is not followed, it may cause mis-operation of the panel.
Refer to "Sequence of Power Supplies and Signals" described in this Specification for details.
In addition, refer to individual specifications for unused terminals.
3) IMAGE STICKING IN A DISPLAY
Design the system not to display the same pattern for a long time.
Continuing the same pattern display for a long time or inputting the signals besides recommendation may cause the
phenomenon “image sticking” which remains vaguely after changing patterns.
4) GROUNDING FOR METAL FRAME(BEZEL)
Connecting metal frame (front bezel or/and rear case) of LCD module to ground is strongly recommended.
Generally grounding from metal frame of LCD module effects to improve endurance of ESD, various noise and
radiation interference from system design.
However, there are the above performance differences by system structure, so final conclusion for the grounding
should be decided after confirmation of matching with system side.