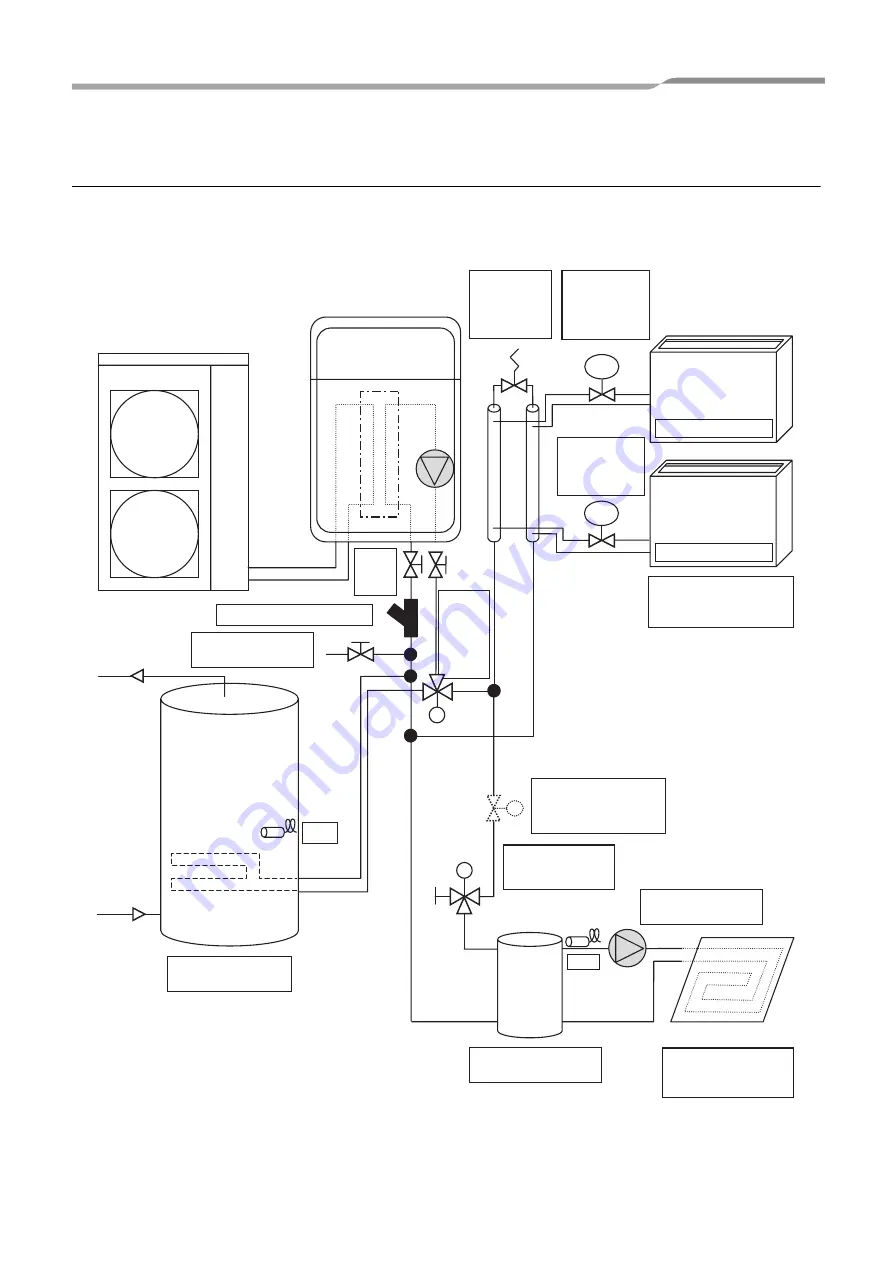
– 8 –
Hydro Unit
Installation Manual
Example of 2-zone temperature control and hot water supply
system
The following shows an example of the 2-zone temperature control.
A buffer tank and a water pump are required for the 2-zone temperature control.
▼
Fig. 5-02
M
M
M
TTW
TFI
TRV
TRV
Temp.
Regulating
Valve
(Mechanical)
Isolating
Valves
(Service)
Strainer (40 mesh / 0.4 mm)
Diverting
3-Way
Valve for
Sanitary
Hot
Water
Cylinder
Drain Cock for water
Charge and Drain
Zone 1
Fan Coil Unit (Heating
or Cooling)
Temperature
Regulating
Valve
(Mechanical)
Hi-Pressure
By-Pass
Valve
Indirect Sanitary Hot
Water Cylinder
Mixing 3-Way
Valve for Under
Floor Heating
External Pump for
Under Floor Heating
Motorized 2-Way Valve
is required if fan coil
units are in cooling
operation.
Direct Buffer tank for
Under Floor Heating
Zone 2
Under-floor Heating
(2-Way Valve Control)
8-EN
Summary of Contents for HFC series
Page 47: ...EF99808601 ...