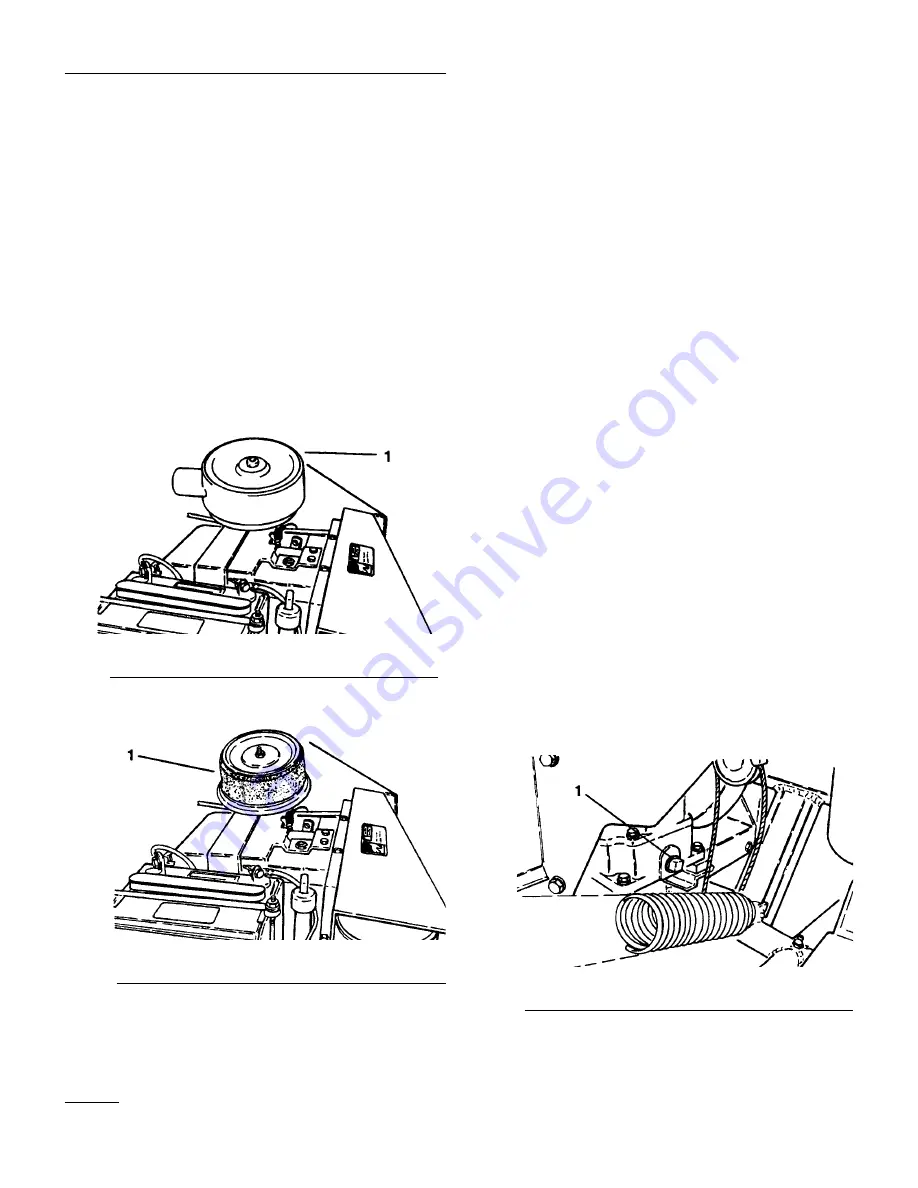
1.
Remove the lock nut and cover.
2.
Remove the foam pre-cleaner by sliding it off the
paper element.
3.
Wash the pre-cleaner in detergent and warm water.
Then wrap it in a cloth and squeeze it dry. Do not
wring it. Next, saturate the precleaner in engine oil
and squeeze it to remove excess oil.
4.
Install the cleaned pre-filter on the paper cartridge.
Inspect the paper element every 50 hours of operation
and replace it when it is dirty or damaged. Do not wash
the paper element or clean it with compressed air.
CHANGING ENGINE OIL AND THE
OIL FILTER
Diesel models:
Change the oil and the oil filter initially after the first
20 hours of operation, thereafter change the oil every 50
hours and the oil filter every 100 hours.
1.
Locate the engine the oil drain plug on bottom, rear
of the oil pan. Remove the drain plug and let the
oil flow into the drain pan. When the oil stops,
install the drain plug.
2.
Locate the engine filter on the rear of the engine.
Remove the oil filter. Apply a light coat of clean
oil to the new filter seal before screwing it on. DO
NOT OVER-TIGHTEN.
3.
Add oil to the crankcase.
Gasoline models:
For new engines, change the oil after the first 5 operat-
ing hours. Thereafter, under normal conditions change
the oil after every 25 hour of engine operation. Change
more often if you operate the engine in dusty or dirty
conditions.
If possible, run the engine just before changing the oil,
which will make the oil flow more freely and carry more
contaminants.
26
Maintenance
Figure 33
1.
Air cleaner cover
Figure 34
1.
Foam pre-cleaner
Figure 35
1.
Crankcase drain plug (gasoline engines)
Summary of Contents for reelmaster 216
Page 24: ...Figure 28 Figure 29 Figure 30 Figure 31 24 Maintenance ...
Page 34: ......
Page 35: ......
Page 36: ......