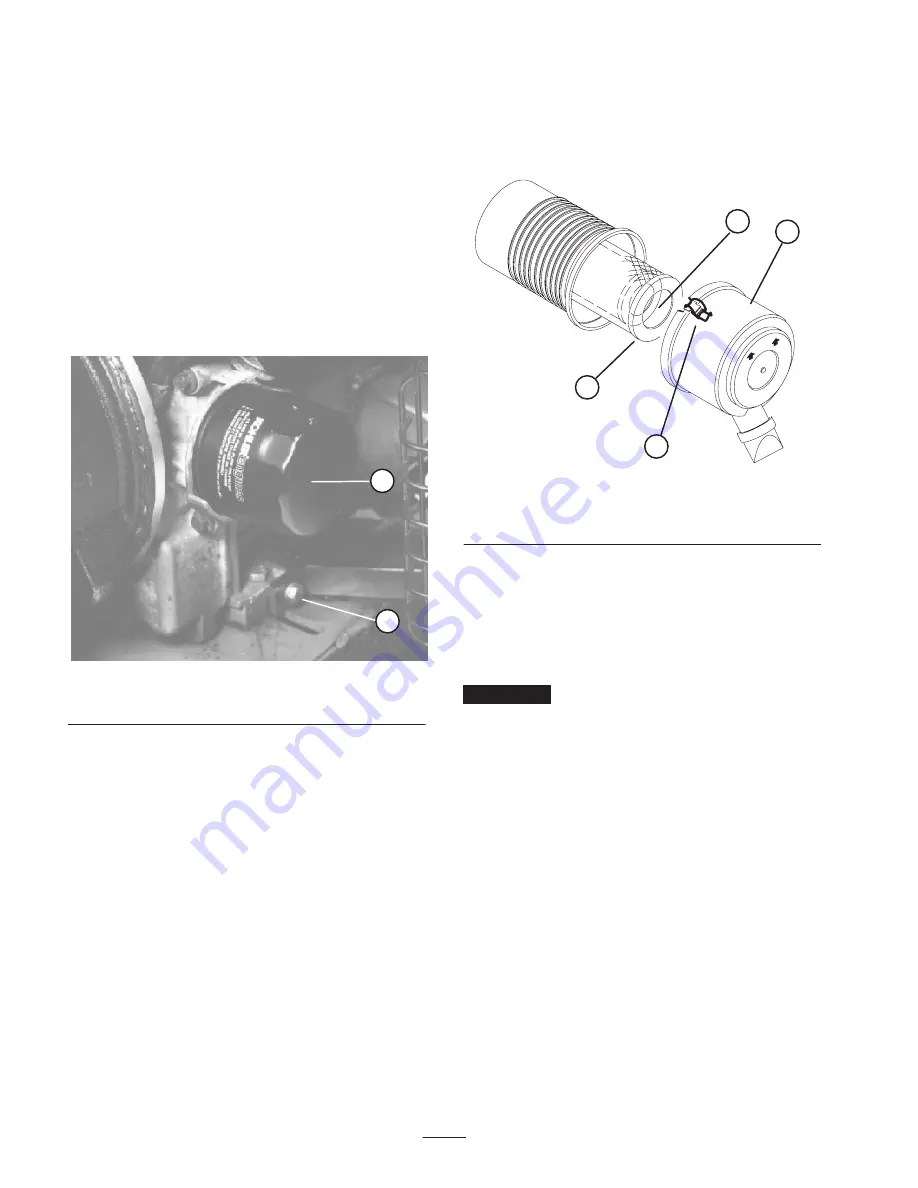
16
Changing Engine Oil and Filter
Change oil initially after the first 5 hours of operation,
thereafter change oil every 100 hours and filter every 200
hours.
1.
Park the machine on a level surface and turn the engine
off.
2.
Remove drain plug and let oil flow into drain pan.
When oil stops, install drain plug.
Note:
Warm oil flows better and carries more contaminants
than cold oil.
3.
Remove oil filter. Apply a light coat of clean oil to the
new filter gasket.
1
2
Figure 18
1. Drain plug
2. Oil filter
4.
Screw filter on by hand until gasket contacts mounting
plate, then tighten 1/2 turn further. DO NOT
OVER–TIGHTEN.
5.
Add oil to crankcase, refer to Check Engine Oil.
6.
Dispose of used oil properly.
General Air Cleaner
Maintenance
•
Check air cleaner body for damage which could
possibly cause an air leak. Replace a damaged air
cleaner body.
•
Service the air cleaner filters every 400 hours (more
frequently in extreme dusty or dirty conditions). Do not
over service air filter.
•
Be sure cover is sealing around air cleaner body.
Servicing Air Cleaner
1.
Release latches securing air cleaner cover to air cleaner
body. Separate cover from body. Clean inside of air
cleaner cover.
2
ÎÎ
ÎÎ
ÎÎÎ
ÎÎÎ
ÎÎÎ
ÎÎ
ÎÎ
ÎÎ
ÎÎ
1
3
4
Figure 19
1. Air cleaner latches
2. Dust cup
3. Primary filter
4. Safety filter
2.
Gently slide primary filter out of air cleaner body to
reduce the amount of dust dislodged. Avoid knocking
filter against air cleaner body.
Do not remove safety
filter.
3.
Inspect primary filter and discard if damaged. Do not
wash or reuse a damaged filter.
Important
Never attempt to clean a safety filter.
Replace the safety filter with a new one after every
three primary filter services.
4.
Blow compressed air from inside to the outside of dry
filter element. Do not exceed 100 psi to prevent damage
to the element.
5.
Keep air hose nozzle at least 2” from filter and move
nozzle up and down while rotating the filter element.
Inspect for holes and tears by looking through the filter
toward a bright light.
6.
Inspect new filter for shipping damage. Check sealing
end of filter. Do not install a damaged filter.
7.
Insert new filter properly into air cleaner body. Make
sure filter is sealed properly by applying pressure to
outer rim of filter when installing. Do not press on
flexible center of filter.
8.
Reinstall cover and secure latches. Make sure cover is
positioned with TOP side up.
Summary of Contents for RAKE-O-VAC 07050
Page 6: ...6 92 8309 93 4041...