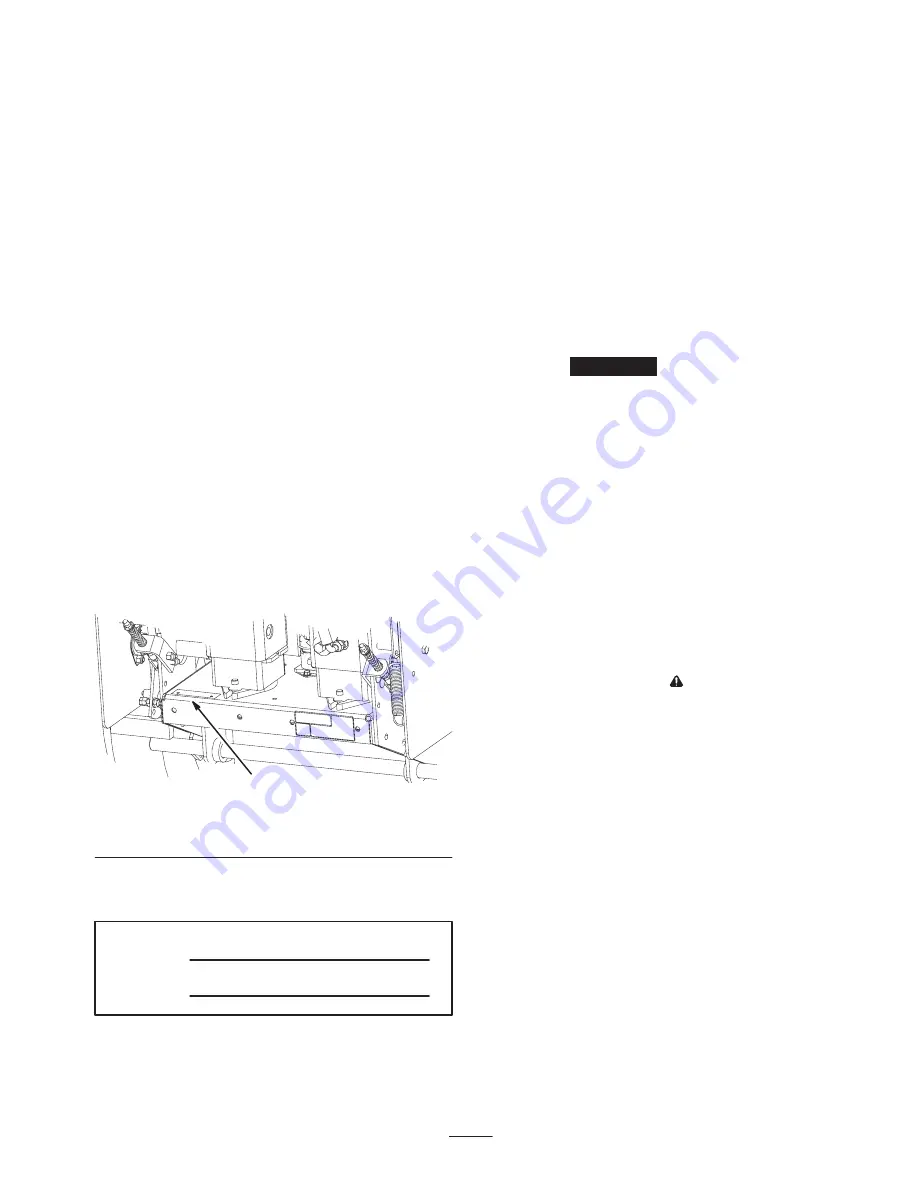
3
Page
Matching the Height of Cut
47
. . . . . . . . . . . . . . . . .
Replacing the Mower Belt
48
. . . . . . . . . . . . . . . . . .
Replacing the PTO Drive Belt
48
. . . . . . . . . . . . . . .
Replacing the Caster Wheel Fork Bushings
49
. . . .
Caster Wheel and Bearings Service
50
. . . . . . . . . . .
Replacing the Grass Deflector
50
. . . . . . . . . . . . . . .
Wiring Diagram
51
. . . . . . . . . . . . . . . . . . . . . . . . . .
Hydraulic Diagram
52
. . . . . . . . . . . . . . . . . . . . . . . .
Cleaning and Storage
53
. . . . . . . . . . . . . . . . . . . . . .
Troubleshooting
53
. . . . . . . . . . . . . . . . . . . . . . . . . . . . .
The Toro Total Coverage Guarantee
56
. . . . . . . . . . . . .
Introduction
Read this manual carefully to learn how to operate and
maintain your product properly. The information in this
manual can help you and others avoid injury and product
damage. Although Toro designs and produces safe
products, you are responsible for operating the product
properly and safely.
Whenever you need service, genuine Toro parts, or
additional information, contact an Authorized Service
Dealer or Toro Customer Service and have the model and
serial numbers of your product ready. Figure 1 illustrates
the location of the model and serial numbers on the
product.
1
m–6612
Figure 1
1.
Location of the model and serial numbers
Write the product model and serial numbers in the space
below:
Model No.
Serial No.
This manual identifies potential hazards and has special
safety messages that help you and others avoid personal
injury and even death. Danger, Warning, and Caution are
signal words used to identify the level of hazard.
However, regardless of the hazard, be extremely careful.
Danger signals an extreme hazard that will cause serious
injury or death if you do not follow the recommended
precautions.
Warning signals a hazard that may cause serious injury or
death if you do not follow the recommended precautions.
Caution signals a hazard that may cause minor or
moderate injury if you do not follow the recommended
precautions.
This manual uses two other words to highlight
information.
Important
calls attention to special
mechanical information and Note: emphasizes general
information worthy of special attention.
Safety
This machine meets or exceeds the B71.4–1999
specifications of the American National Standards
Institute in effect at the time of production.
Note: The addition of attachments made by other
manufacturers that do not meet American National
Standards Institute certification will cause noncompliance
of this machine.
Improper use or maintenance by the operator or owner
can result in injury. To reduce the potential for injury,
comply with these safety instructions and always pay
attention to the safety alert
symbol, which means
CAUTION, WARNING, or DANGER—“personal
safety instruction.” Failure to comply with the
instruction may result in personal injury or death.
Safe Operating Practices
The following instructions are from ANSI standard
B71.4—1999.
Training
•
Read the Operator’s Manual and other training
material. If the operator(s) or mechanic(s) can not read
English it is the owner’s responsibility to explain this
material to them.
•
Become familiar with the safe operation of the
equipment, operator controls, and safety signs.
•
All operators and mechanics should be trained. The
owner is responsible for training the users.