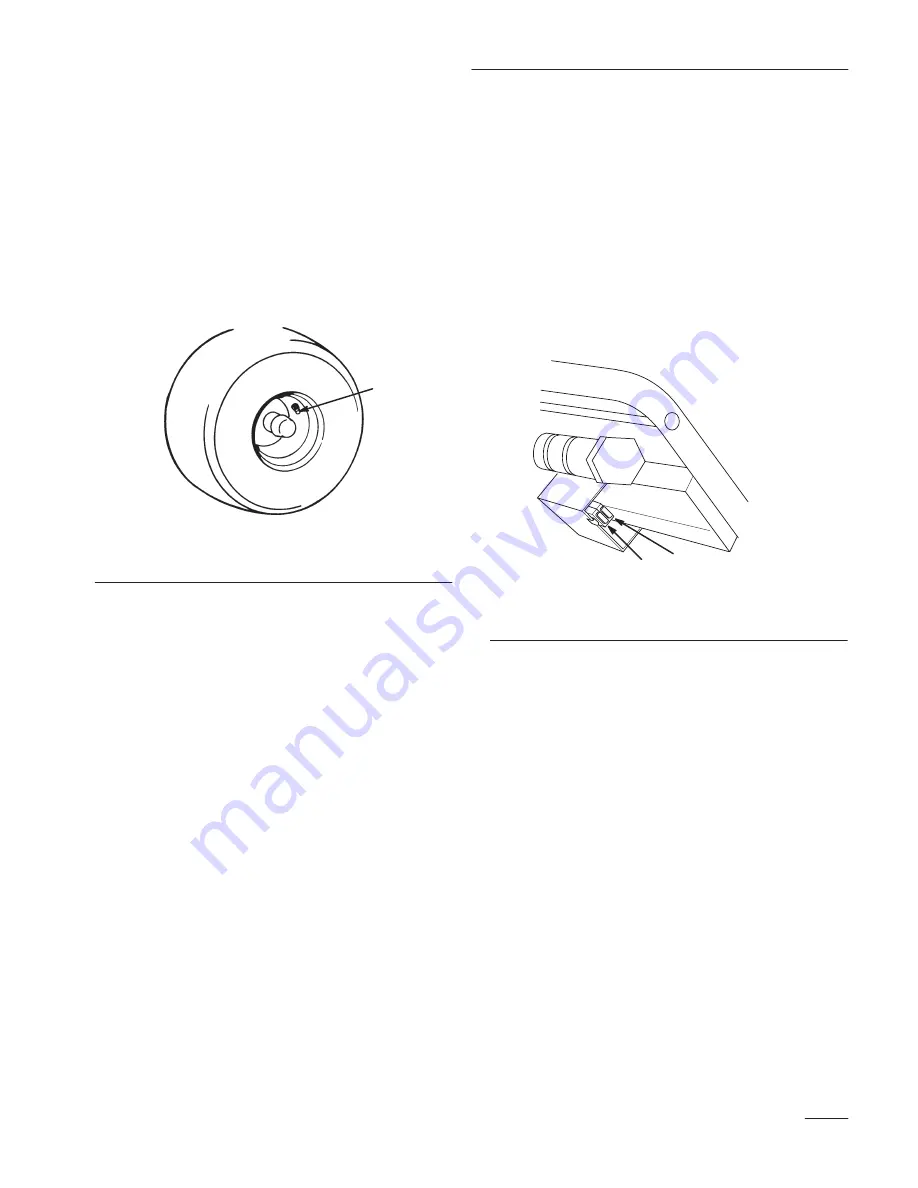
Maintenance
29
Tire Pressure
Maintain the air pressure in the front and rear tires as
specified. Uneven tire pressure can cause uneven cut.
Check the pressure at the valve stem after every 50
operating hours or monthly, whichever occurs first
(Fig. 23). Check the tires when they are cold to get
the most accurate pressure reading.
Pressure: 15 psi (.103 kPa) rear and castor tires
1
m–1872
Figure 23
1.
Valve stem
Fuse
Service Interval/Specification
The electrical system is protected by a fuse. It
requires no maintenance, however, if the fuse blows
check component/circuit for malfunction or short. To
replace fuse pull out on the fuse (Fig. 24) to remove
or replace it.
Fuse:
F1
Main–7.5 amp, blade-type
F2
Starter–30 amp, blade-type
m–3100
2
1
Figure 24
1.
Fuse 7.5 amp
2.
Fuse 30 amp
Summary of Contents for ProLine 20 HP
Page 9: ...Safety 7 Slope Chart Read all safety instructions on pages 2 9...
Page 10: ...8...
Page 40: ...Maintenance 38 Wiring Diagram...
Page 41: ...Maintenance 39 Hydraulic Diagram...
Page 45: ......
Page 46: ......
Page 47: ......