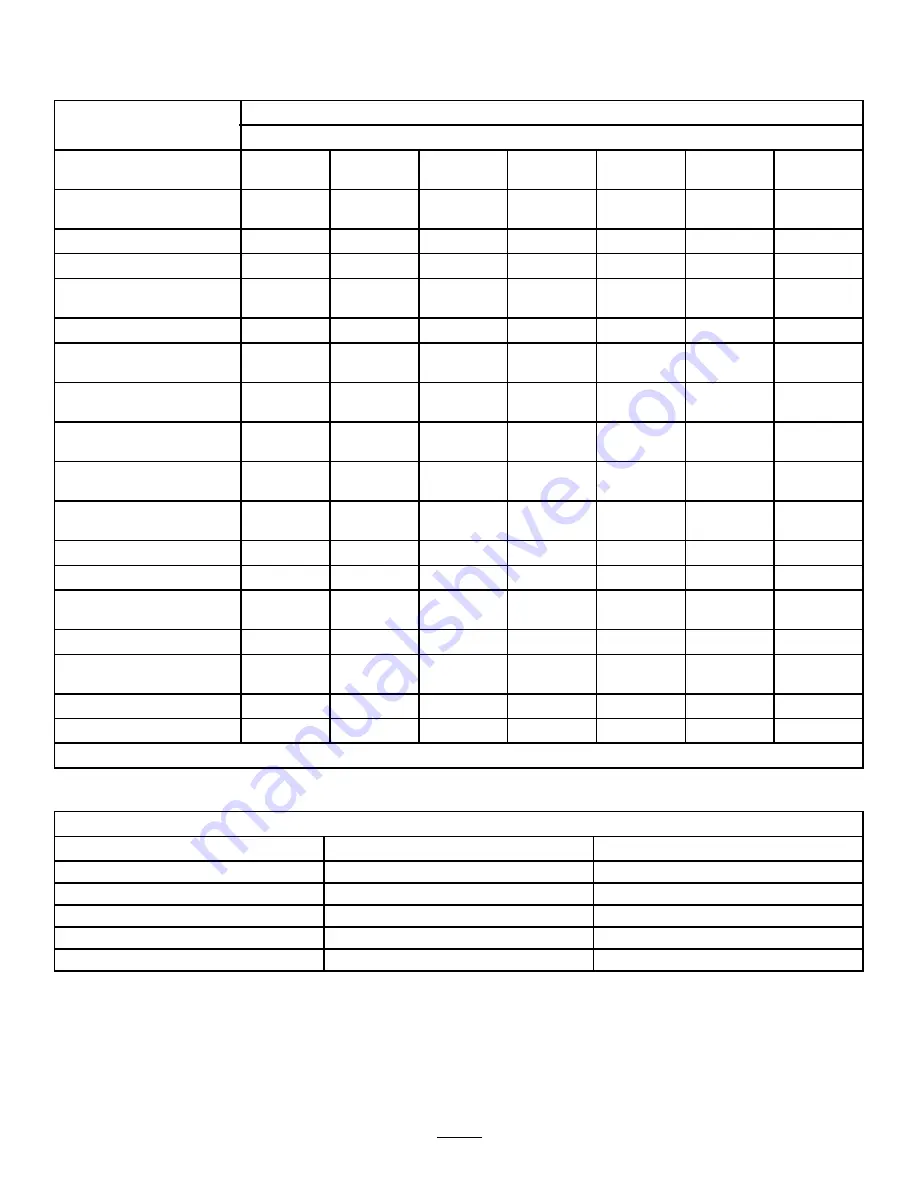
Daily Maintenance Checklist
Duplicate this page for routine use.
For the week of:
Maintenance Check Item
Mon.
Tues.
Wed.
Thurs.
Fri.
Sat.
Sun.
Check the safety-interlock
operation.
Check the instrument
operation
Check the brake operation.
Check the fuel level.
Check the hydraulic-fluid
level.
Check the engine-oil level.
Clean the engine-air-cooling
fins.
Inspect the air-filter
pre-cleaner.
Check any unusual engine
noises.
Check the reel-to-bedknife
adjustment.
Check the hydraulic hoses
for damage.
Check for fluid leaks.
Check the tire pressure.
Check the height-of-cut
adjustment.
Lubricate all grease fittings.
1
Lubricate the mow, lift, and
brake linkage.
Touch-up damaged paint.
Wash the machine.
1. Immediately after every washing, regardless of the interval listed.
Notation for Areas of Concern
Inspection performed by:
Item
Date
Information
27
Summary of Contents for Greensmaster 3120
Page 45: ...Notes...
Page 46: ...Notes...