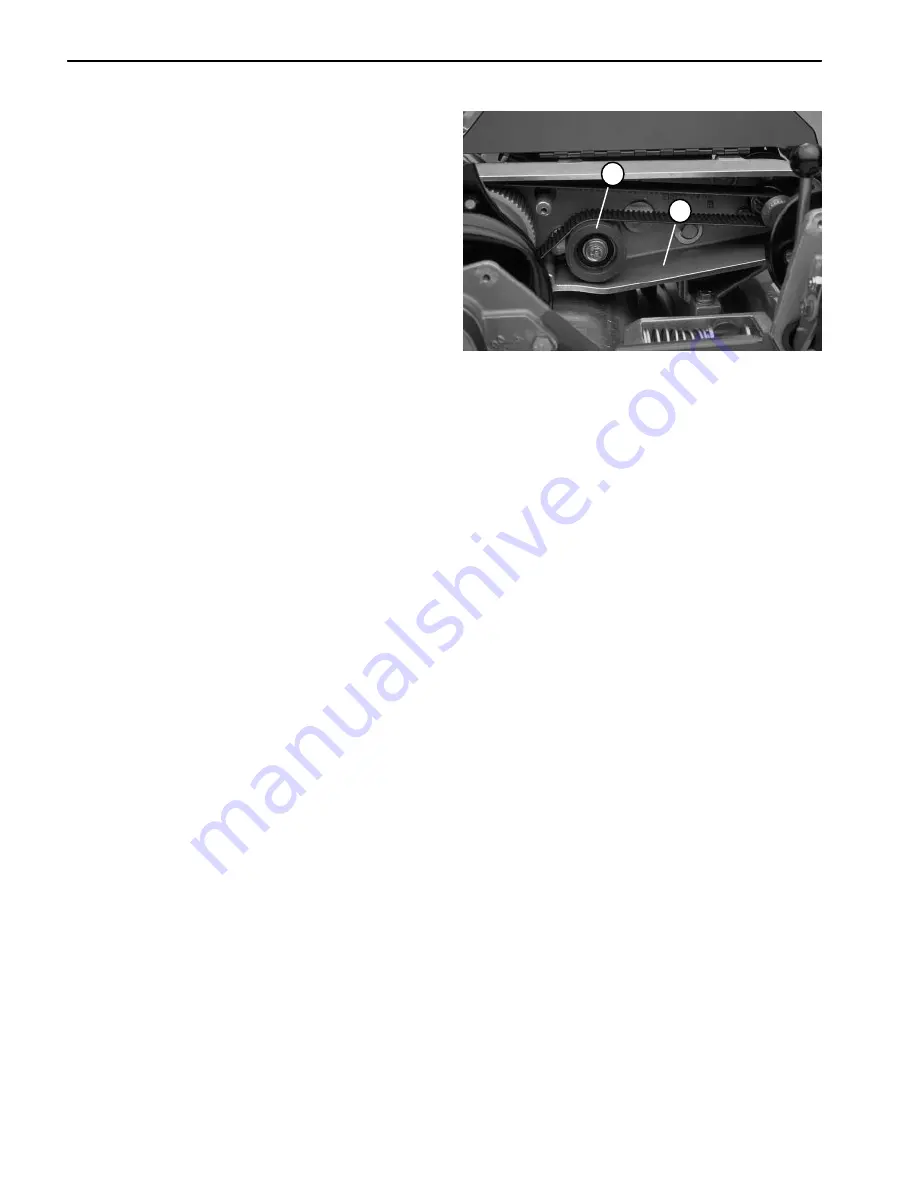
Greensmaster 1000/1600
Traction and Reel Drive Systems
Page 4 – 24
Differential Idler and Bearing
Removal
1.
Park mower on a level surface. Make sure engine
is OFF. Remove high tension lead from the spark plug.
2.
Remove capscrews (39) and lock washers (40) se-
curing rear and front box covers (38 and 39) to the coun-
tershaft housing (1). Pull covers from housing (Fig. 33).
3.
Remove cap screw and lock washer that secure the
idler pulley (Fig. 37). Remove idler pulley from counter-
shaft housing (Fig. 39).
Disassembly (Fig 33)
1.
Remove cap screw (47), lock washer (12), and flat
washer (46) from the spacer (54). Remove retaining ring
(48) from the pulley (44).
2.
Press spacer (54) out of the pulley (44). Press bear-
ings (45) out of the pulley.
Assembly (Fig 33)
1.
Press bearings (45) into the pulley (44). Press
spacer (54) into the pulley.
2.
Install retaining ring (48) into the pulley (44). Secure
cap screw (47), lock washer (12), and flat washer (46)
into the spacer (54).
Installation
1.
Park mower on a level surface. Make sure engine
is OFF. Remove high tension lead from the spark plug.
2.
Reinstall idler pulley to the countershaft housing
(Fig. 39). Secure idler pulley with cap screw and lock
washer. Tighten cap screw until washer just starts to
compress. Spacer must be free to rotate (Fig. 37).
3.
Adjust differential belt tension and reinstall front and
rear box covers (see Differential Belt Adjustment).
1. Idler
pulley
2. Countershaft
housing
Figure 39
1
2
Summary of Contents for Greenmaster 1000
Page 2: ...Greensmaster 1000 1600...
Page 4: ...Greensmaster 1000 1600...
Page 8: ...Greensmaster 1000 1600 Page 1 4 Safety On Control Panel Part No 93 9012...
Page 10: ...Greensmaster 1000 1600 Page 2 2 Product Records and Manuals Equivalents and Conversions...
Page 12: ...Greensmaster 1000 1600 Page 2 4 Product Records and Manuals...
Page 30: ...Greensmaster 1000 1600 Page 3 14 Engine...
Page 66: ...Greensmaster 1000 1600 Traction and Reel Drive Systems Page 4 36...
Page 96: ...Greensmaster 1000 1600 Page 6 14 Wheels and Accessories...
Page 138: ...Greensmaster 1000 Grooming Reel Kit Page 8 22...
Page 139: ......
Page 140: ...Commercial Products PART NO 96889SL Rev A The Toro Company 1996 1997 Printed in U S A...