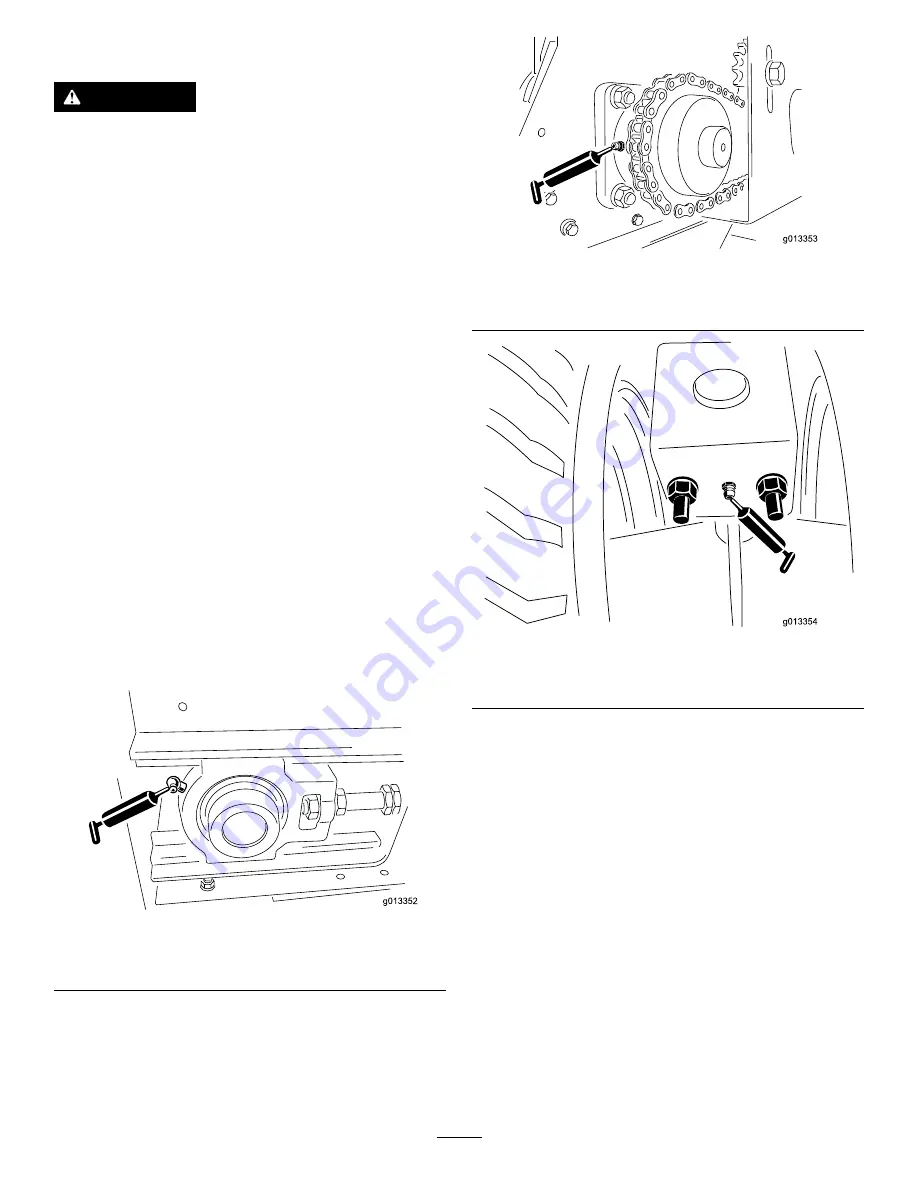
Maintenance
WARNING
Disconnect all power sources to the machine before
doing maintenance work.
Note:
Download a free copy of the schematics by visiting
www.Toro.com and searching for your machine from the
Manuals link on the home page.
Lubrication
Lubricating the machine
•
Use an automotive, all-purpose grease.
•
Lubricate regularly, after 25 hours of normal operation.
•
Lubricate daily when operating in extremely dusty and
dirty conditions.
•
Lubricate all bearings, bushings, and chains.
Lubrication Procedure
Several grease fittings are located on the machine and the
tow-behind chassis (
and
1.
Clean the grease fittings.
2.
Pump the grease into the bearings and the bushings.
3.
Clean off the excess grease.
4.
Clean and repack the wheel bearings every year or
every 300 hours of operation
Figure 52
1.
Grease fitting on Base Model (one at left front, one at right
front)
Figure 53
1.
Grease fitting on Base Model (one at left rear, one at right
rear)
Figure 54
1.
Grease fitting on tow-behind chassis (front and rear, left and
right). Grease once per year.
Daily Checks
At the start of each day, complete these safety checks before
operating the machine. Report any safety problems to your
supervisor. See the Safety Instructions in this manual for
details.
Tires and Wheels
•
The recommended tire pressure for the Tow Chassis is 10
psi (69 kPa), or as recommended by the tire manufacturer.
Refer to the Operator's Manual for the tow vehicle tire
specifications.
•
Check for excessive wear or visible damage.
•
Check that the wheel bolts are tight and none are missing.
Rear Gate
Check that the adjustable section of the rear gate opens and
closes without sticking.
34