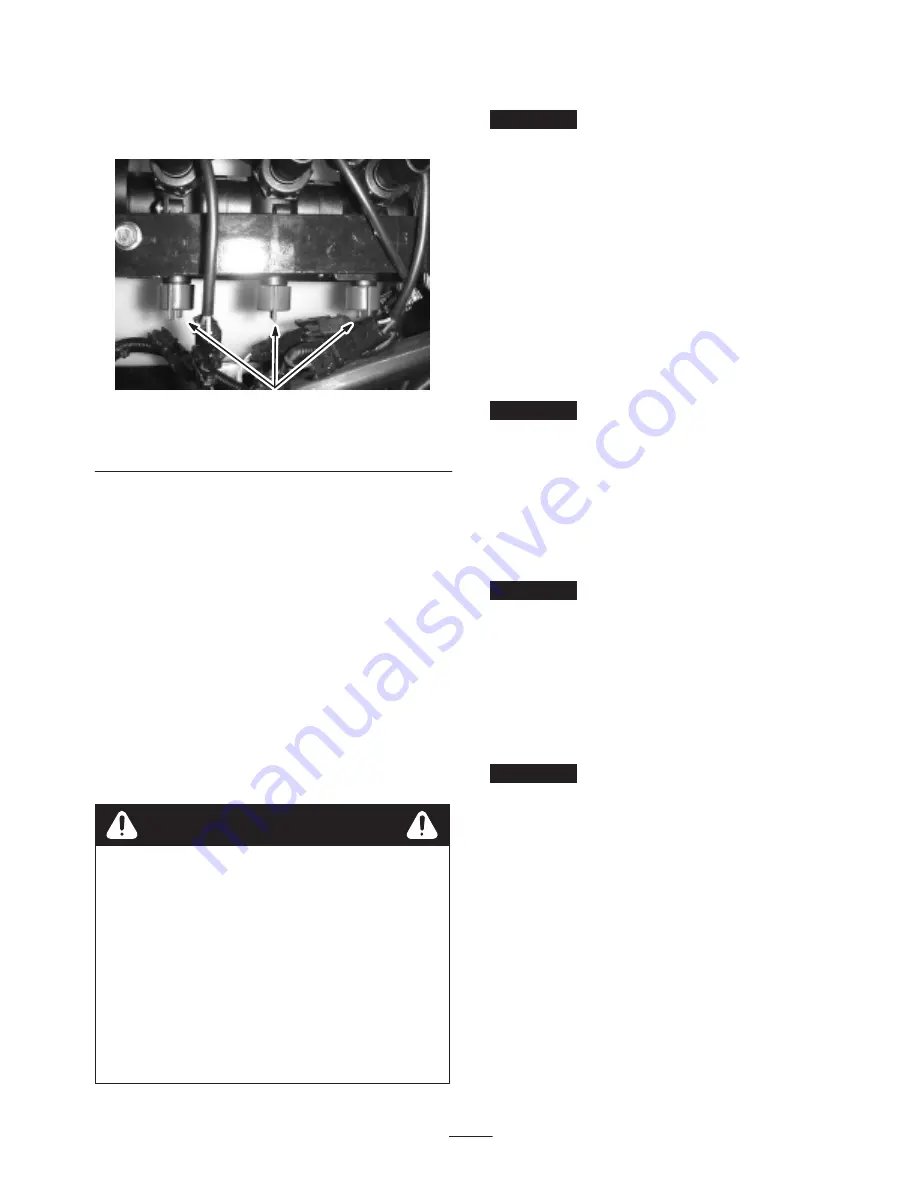
27
11. Adjust the boom bypass valve (Fig. 26) under the
boom control valve for the boom you turned off until
the pressure reading on the gauge is the same as it was
in step 8.
1
Figure 32
1.
Boom bypass valves
12. Turn the boom on.
13. Repeat steps 10 through 12 for the other booms.
14. Drive the vehicle at the desired speed while spraying
and turn each boom off individually. The pressure on
the gauge should not change.
Operating the Sprayer
To operate the sprayer you first fill the spray tank, then
apply the solution to the work area, and finally clean the
tank. It is important that you complete all three of these
steps in succession to avoid damaging the sprayer. For
example, do not mix and add chemicals in the spray tank
at night and then spray in the morning. This would lead to
separation of the chemicals and possible damage to the
sprayer components.
Chemicals are hazardous and can cause personal
injury.
•
Read the directions on the chemical labels
before handling the chemicals and follow all
manufacturer recommendations and
precautions.
•
Keep chemicals away from your skin. Should
contact occur, wash the affected area
thoroughly with soap and clean water.
•
Wear goggles and any other protective
equipment recommended by the chemical
manufacturer.
Caution
Filling the Spray Tank
Important
Ensure that the chemicals you will be using
are compatible for use with Viton (see the manufacturer’s
label; it should indicate if it is not compatible). Using a
chemical that is not compatible with Viton will degrade
the o-rings in the sprayer, causing leaks.
1. Stop the sprayer on a level surface, move the range
selector to the Neutral position, stop the engine, and
set the parking brake.
2. Determine the amount of water needed to mix the
amount of chemical you need as prescribed by the
chemical manufacturer.
3. Open the lid on the spray tank.
4. Add 3/4 of the required water to the spray tank using
the anti-siphon fill receptacle.
Important
Always use fresh clean water in the spray
tank. Do not pour concentrate into an empty tank.
5. Start the engine, engage the PTO, and set the hand
throttle if equipped.
6. Turn the agitation control valve to the 9 o’clock
position to start agitation in the tank.
7. Add the proper amount of chemical concentrate to the
tank, as directed by the chemical manufacturer.
Important
If you are using a wetable powder, mix the
powder with a a small amount of water to form a slurry
before adding it to the tank
8. Add the remaining water to the tank.
Note: Better agitation can be achieved by decreasing the
application rate setting.
Applying Chemicals
Important
In order to ensure that your solution
remains well mixed, use the agitation feature whenever
you have solution in the tank. For agitation to work, the
PTO must be engaged and the engine must be running
above an idle. If you stop the vehicle and need agitation
on, place the shift lever in the Neutral position, set the
parking brake, Engage the PTO, engage the clutch, and set
the hand throttle, if equipped.
Note: This procedure assumes that the PTO is engaged
from the Filling the Spray Tank procedure.
1. Swing the booms into position.
2. Set the master boom switches to the Off position. The
Spray Pro monitor displays “HOLD.”
3. Set the individual boom switches, as needed, to the On
positions.
4. Drive to the location where you will be spraying.