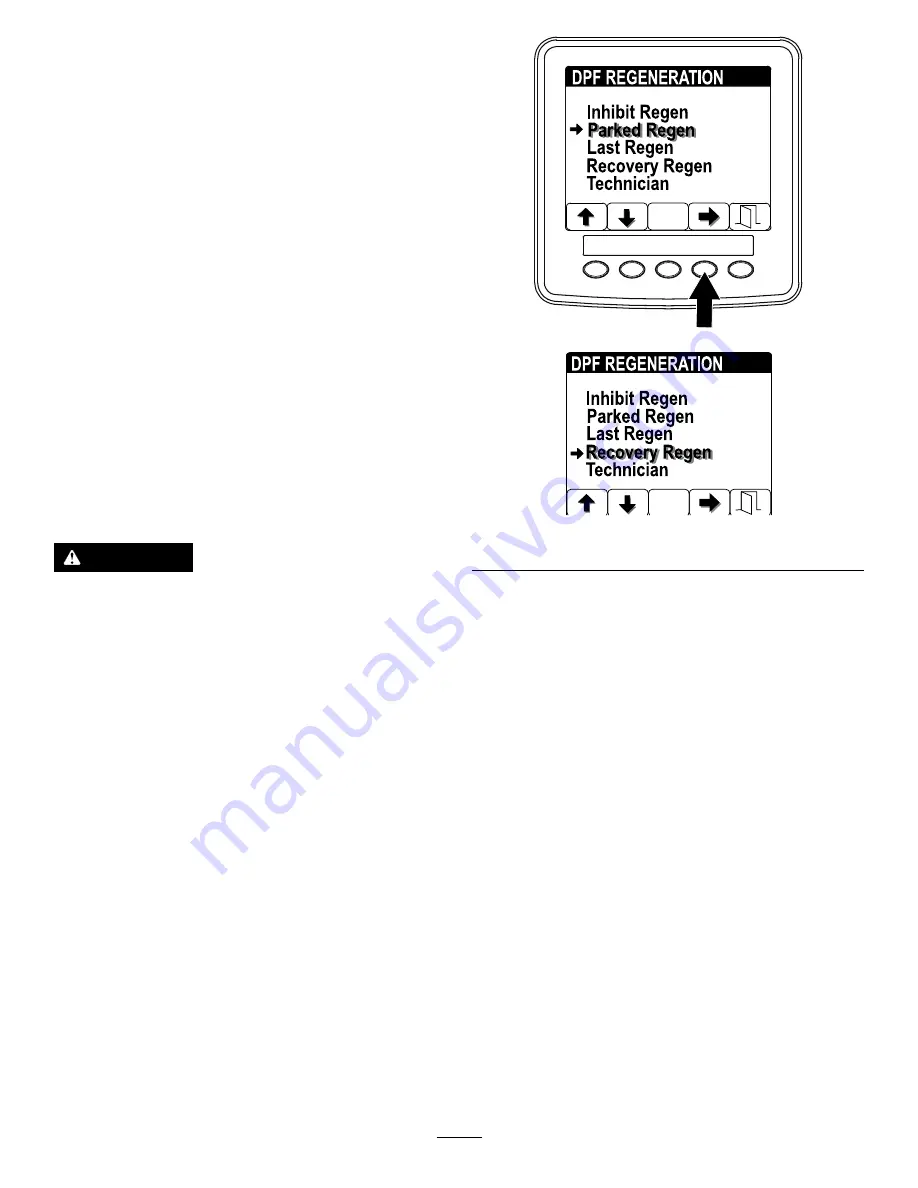
Preparing to Perform a Parked or Recovery
Regeneration
1.
Ensure that the machine has fuel in the tank for
the type of regeneration you are performing:
•
Parked Regeneration:
Ensure that you
have 1/4 tank of fuel before performing the
parked regeneration.
•
Recovery Regeneration:
Ensure that you
have 1/2 tank of fuel before performing the
recovery regeneration.
2.
Move the machine outside to an area away from
combustible materials.
3.
Park the machine on a level surface.
4.
Ensure that the traction control or motion-control
levers are in the N
EUTRAL
position.
5.
If applicable, shut off the PTO, and lower the
cutting units or accessories.
6.
Engage the parking brake.
7.
Set the throttle to the low I
DLE
position.
Performing a Parked or Recovery
Regeneration
CAUTION
The exhaust temperature is hot (approximately
600°C (1,112°F) during DPF regeneration. Hot
exhaust gas can harm you or other people.
•
Never operate the engine in an enclosed
area.
•
Make sure that there are no flammable
materials around the exhaust system.
•
Never touch a hot exhaust system
component.
•
Never stand near or around the exhaust
pipe of the machine.
Important:
The computer of the machine cancels
DPF regeneration if you increase the engine speed
from low idle or release the parking brake.
1.
Access the DPF Regeneration menu, and press
buttons 1 or 2 to scroll down to the P
ARKED
R
EGEN
option or the R
ECOVERY
R
EGEN
option
(
).
g241869
g241870
Figure 54
2.
Press the button 4 to select the Parked Regen
entry or the Recovery Regen entry (
).
3.
On the Parked Regen menu or Recovery
Regen menu, press the button 4 to start the
regeneration (
).
49
Summary of Contents for 31698
Page 97: ...Notes ...