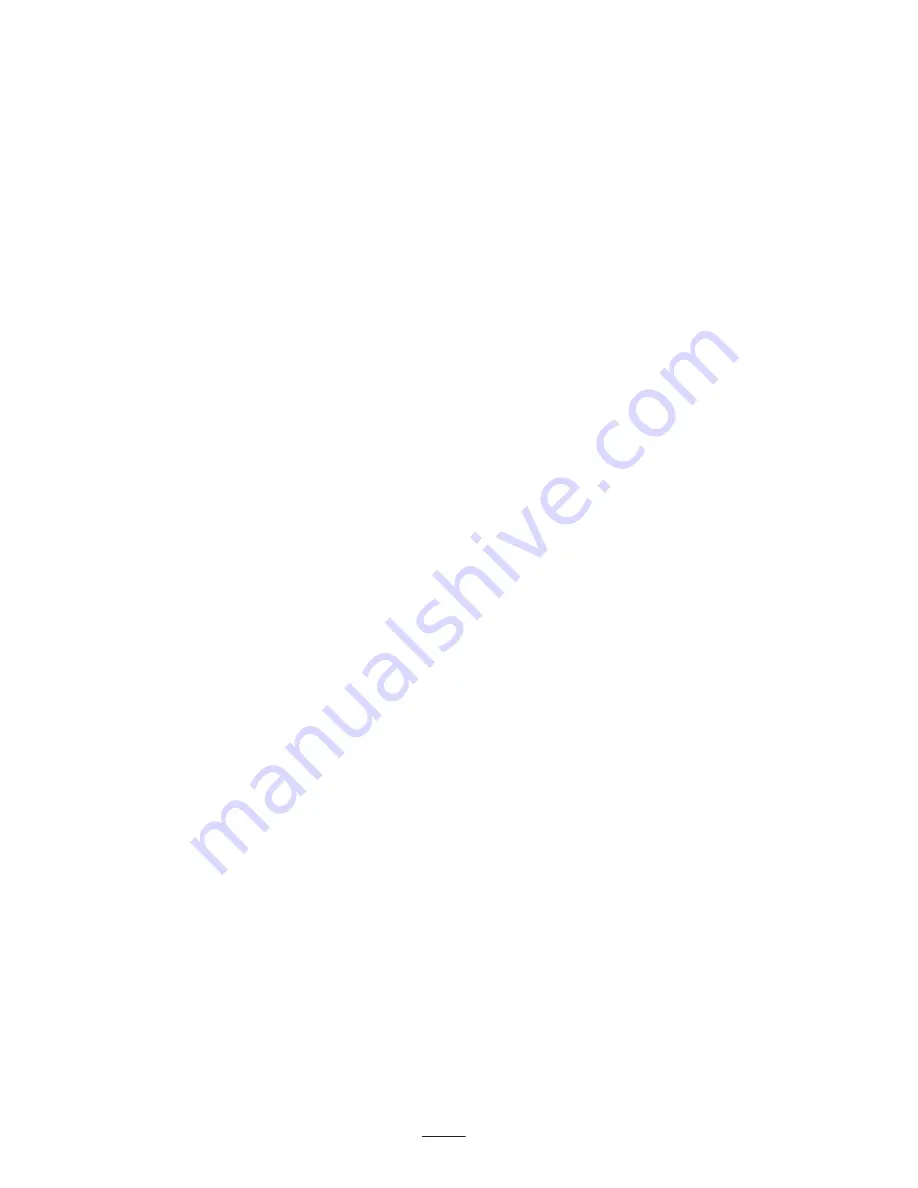
4
•
Use extra care when handling gasoline and other fuels.
They are flammable and vapors are explosive.
•
Use only an approved container
•
Never remove gas cap or add fuel with engine
running. Allow engine to cool before refueling.
Do not smoke.
•
Never refuel or drain the machine indoors.
•
Check that operator’s presence controls, safety
switches and shields are attached and functioning
properly. Do not operate unless they are functioning
properly.
Operation
•
Never run an engine in an enclosed area.
•
Only operate in good light, keeping away from holes
and hidden hazards.
•
Be sure all drives are in neutral and wheels are
chocked and blocked before starting engine. Only start
engine from the operator’s position.
•
Be sure of your footing while using this machine,
especially when backing up. Walk, don’t run. Never
operate on wet grass. Reduced footing could cause
slipping.
•
Slow down and use extra care on hillsides. Be sure to
travel side–to–side on hillsides. Turf conditions can
affect the machine’s stability. Use caution while
operating near drop–offs.
•
Slow down and use caution when making turns and
when changing directions on slopes.
•
Never raise deck with the blades running.
•
Never operate with the PTO shield, or other guards not
securely in place. Be sure all interlocks are attached,
adjusted properly, and functioning properly.
•
Never operate with the discharge deflector raised,
removed or altered, unless using a grass catcher.
•
Do not change the engine governor setting or
overspeed the engine.
•
Stop on level ground, disengage drives, chock or block
wheels, shut off engine before leaving the operator’s
position for any reason including emptying the
catchers or unclogging the chute.
•
Stop equipment and inspect blades after striking
objects or if an abnormal vibration occurs. Make
necessary repairs before resuming operations.
•
Keep hands and feet away from the cutting unit.
•
Look behind and down before backing up to be sure of
a clear path.
•
Keep pets and bystanders away.
•
Slow down and use caution when making turns and
crossing roads and sidewalks. Stop blades if not
mowing.
•
Be aware of the mower discharge direction and do not
point it at anyone.
•
Do not operate the mower under the influence of
alcohol or drugs
•
Use care when loading or unloading the machine into
or from a trailer or truck
•
Use care when approaching blind corners, shrubs,
trees, or other objects that may obscure vision.
Maintenance and storage
•
Disengage drives, chock or block wheels, stop engine
and remove key or disconnect spark plug wire. Wait
for all movement to stop before adjusting, cleaning or
repairing.
•
Clean grass and debris from cutting unit, drives,
mufflers, and engine to help prevent fires. Clean up oil
or fuel spillage.
•
Let engine cool before storing and do not store near
flame.
•
Shut off fuel while storing or transporting. Do not store
fuel near flames or drain indoors.
•
Park machine on level ground. Chock or block wheels
when it is parked. Never allow untrained personnel to
service machine.
•
Use jack stands to support components when required.
•
Carefully release pressure from components with
stored energy.
•
Remove spark plug wire before making any repairs.
•
Use care when checking blades. Wrap the blade(s) or
wear gloves, and use caution when servicing them.
Only replace blades. Never straighten or weld them.
•
Keep hands and feet away from moving parts. If
possible, do not make adjustments with the engine
running.
•
Keep all parts in good working condition and all
hardware tightened. Replace all worn or damaged
decals.
Toro Mower Safety
The following list contains safety information
specific to Toro products and other safety information
you must know.
Summary of Contents for 30339
Page 6: ...6 ...
Page 7: ...7 Slope Chart ...
Page 8: ...8 ...
Page 10: ...10 105 4146 1 523552 98 0776 98 4387 95 1543 104 8569 105 4144 104 8172 ...
Page 11: ...11 105 4109 105 0840 105 4110 104 8186 104 8171 105 4106 ...
Page 12: ...12 105 4108 ...