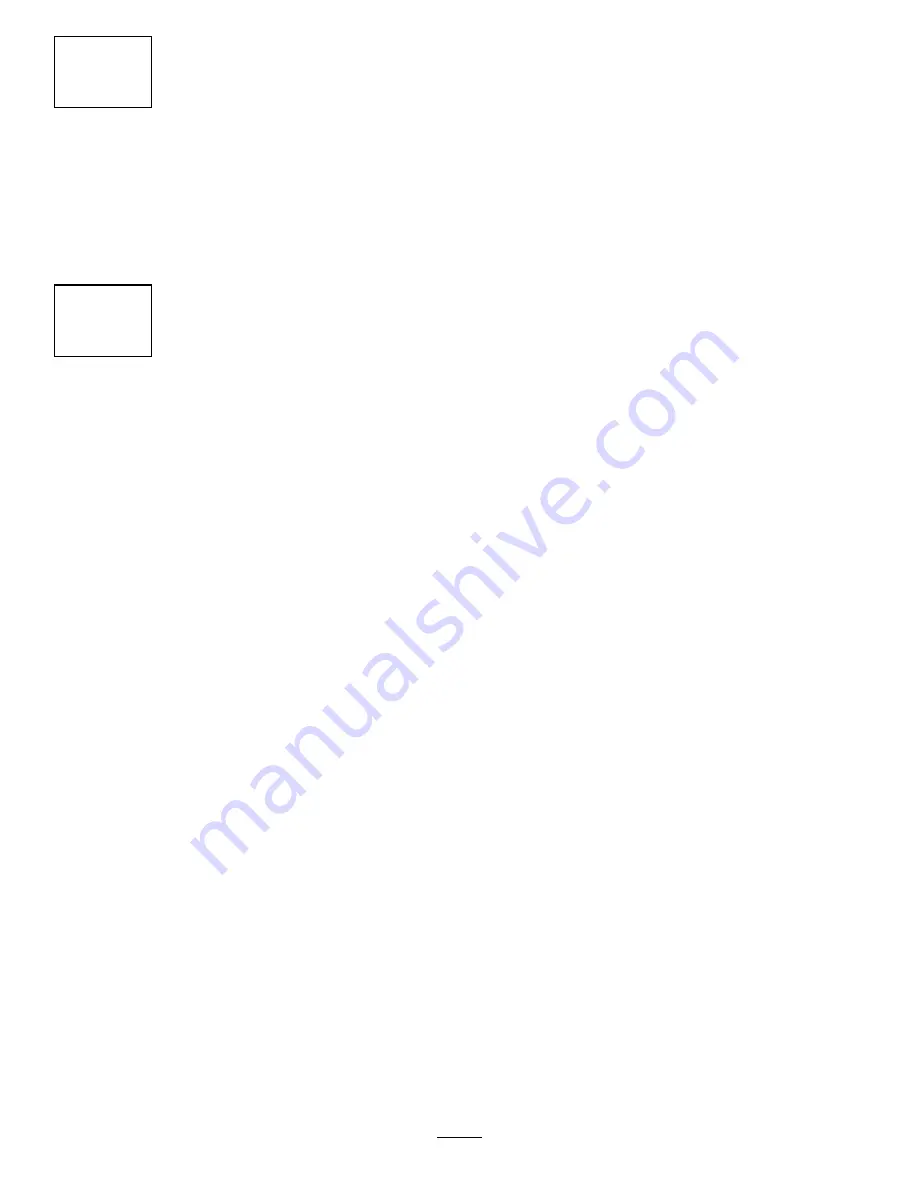
9
Adjusting the Brush Height
No Parts Required
Procedure
Refer to
Adjusting the Brush Height (page 23)
.
10
Leveling the Core Processor
No Parts Required
Procedure
Refer to
Leveling the Core Processor (page 24)
.
19
9
Adjusting the Brush Height
No Parts Required
Procedure
Refer to
Adjusting the Brush Height (page 23)
.
10
Leveling the Core Processor
No Parts Required
Procedure
Refer to
Leveling the Core Processor (page 24)
.
19