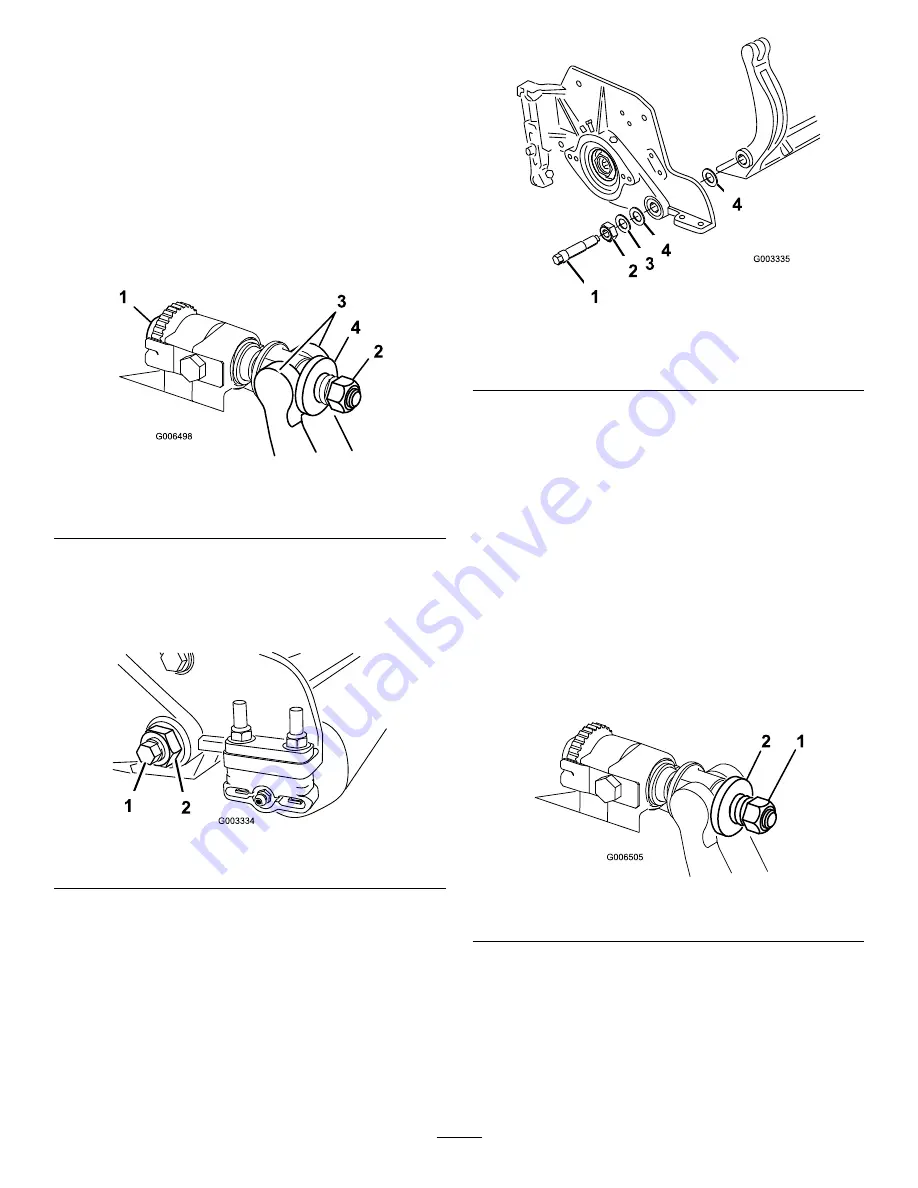
Note:
Reel bearings do not require preload.
Over tightening reel bearing adjuster nut will
damage reel bearings.
4. Retighten set screw securing bearing adjusting nut to
bearing housing. Torque to 12-15 in-lb.
Servicing the Bedbar
Removing the Bedbar
1. Turn bedbar adjuster screws, counterclockwise, to
back bedknife away from reel (Figure 32).
Figure 32
1.
Bedbar adjusting screw
3.
Bedbar
2.
Spring tension nut
4.
Washer
2. Back out the spring tension nut, until the washer is
no longer tensioned against the bedbar (Figure 32).
3. On each side of the machine, loosen the lock nut
securing the bedbar bolt (Figure 33).
Figure 33
1.
Bedbar bolt
2.
Lock nut
4. Remove each bedbar bolt allowing bedbar to be
pulled downward and removed from machine bolt
(Figure 33). Account for 2 nylon and 1 stamped steel
washers on each end of bedbar (Figure 34).
Figure 34
1.
Bedbar bolt
3.
Steel washer
2.
Nut
4.
Nylon washer
Assembling the Bedbar
1. Install bedbar, positioning mounting ears between
washer and bedbar adjuster.
2. Secure bedbar to each side plate with bedbar bolts
(nuts on bolts) and 6 washers. A nylon washer is to
be positioned on each side of side plate boss. Place
a steel washer outside each of the nylon washers
(Figure 34). Torque bedbar bolts to 27-33 ft.-lb.
Tighten locknuts until the outside steel washer
stops rotating and end play is removed but do not
overtighten or deflect side plates. Washers on inside
may have a gap.
3. Tighten spring tension nut until spring is collapsed,
then back off 1/2 turn (Figure 35).
Figure 35
1.
Spring tension nut
2.
Spring
19