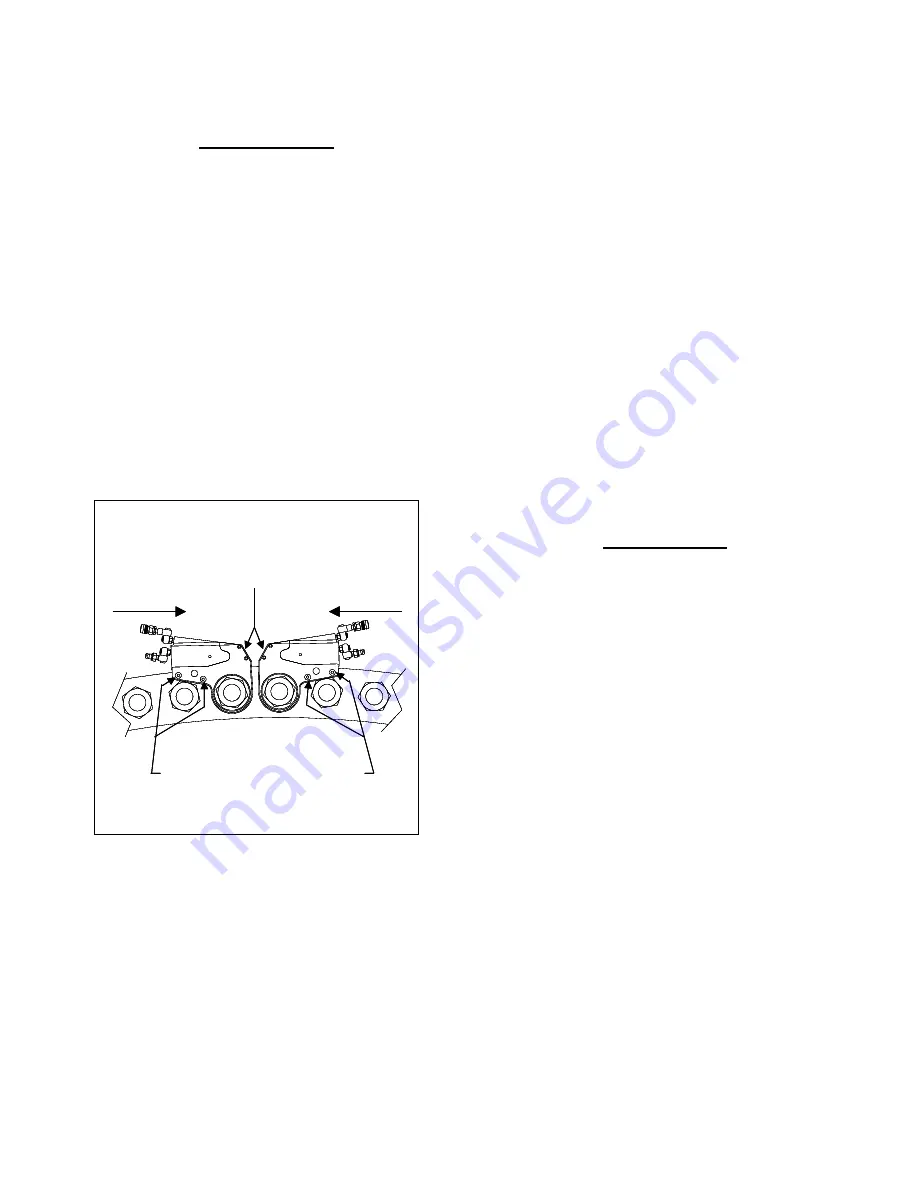
PLACING THE TOOL IN SERVICE
ADJUSTMENTS
SETTING THE TORQUE
After determining the desired torque, use the torque con-
version charts on pages 4 and 5 to determine the pressure
that is necessary to achieve that torque.
1. Connect the tool to the power supply and turn the
pump on.
2. Depress the remote control button causing the
pressure to be shown on the gauge.
3.
Adjust the pressure by loosening the wing nut that
locks the pressure adjustment thumbscrew. Rotate the
thumbscrew clockwise to increase the pressure and
counterclockwise to decrease the pressure. When
decreasing pressure, always lower the pressure below the
desired point and then bring the gauge back up to the
desired pressure.
4.When the desired pressure is reached, retighten the
wing nut and cycle the tool again to confirm that the
desired pressure setting has been obtained.
OPERATING THE WRENCH
The position of the tool relative to the nut determines
whether the action will tighten or loosen the nut. (Refer
to Dwg. 2 for application examples). The power stroke
of the Piston Assembly will always turn the Ratchet Hex
toward the Shroud.1.Place the Ratchet Hex on the nut.
Make certain it is the correct size for the nut and that it
fully engages the nut.
2. Position the reaction surface against an adjacent nut,
flange or solid system component. Make certain that
there is clearance for the hoses, swivels, and inlets.
DO
NOT
allow the tool to react against the hoses, swivels,
or inlets.
3. After having turned the Pump on and presetting the
pressure for the correct torque, depress the remote
control button to advance the Piston Assembly. If the
notch in the piston rod did not engage the Retract Pin in
the Ratchet Link when the Link was joined to the
Housing, it will engage the Pin automatically during the
first advance stroke.
4. When the Link is connected to the Housing and the
wrench is started, the reaction surface of the wrench will
move against the contact point and the nut will begin to
turn.
5. When the nut is no longer turning and the Pump
Gauge reaches the preset pressure, release the remote
control button. The piston rod will retract when the
button is released and under normal conditions, an
audible “click” will be heard as the tool resets itself.
6. Continue to cycle the tool until it “stalls” and the
preset psi/torque has been attained.
7. Once the nut stops rotating, cycle the tool one last
time to achieve total torque.
LUBRICATION
Marine Moly Grease
Lubrication frequency is dependent on factors known
only to the user. The amount of contaminants in the
work area is one factor. Tools used in a clean room
environment will obviously require less service than a
tool used out-doors and dropped in loose dirt or sand.
Marine Moly Grease is formulated not to wash out of the
tool in areas where lubrication is critical. Whenever
lubrication is required, lubricate as follows:
1.
Separate the Low Profile Cylinder from the Ratchet
Link if they are joined.
2.
After wiping of the old grease, apply a daub of Marine
Moly Grease to the hooking notch in the Piston rod
and wipe a film of Marine Moly Grease onto the sides
and faces of the two Sliders.
3.
Disassemble the Ratchet Link as instructed in the
Maintenance Section and wash the components in a
suitable cleaning solution in a well-ventilated area.
4.
Dry the components, then wipe a film of Marine Moly
Grease onto the wear surface of both Side Plate
Sleeves and the hubs of the Ratchet.
5.
Spread a light film of Marine Moly Grease onto the
inner faces of both Side Plates covering the area where
the Drive and Segment Pawl travel.
DO NOT
pack the
teeth of the Segment Pawl or Ratchet with lube. It can
prevent the teeth from engaging properly.
6. Reassemble the Ratchet Link as instructed in the
Maintenance Section.
Wrench Positions
Dwg. 2
TIGHTEN
LOOSEN
SHROUD
REACT BETWEEN THESE POINTS
TIGHTEN
TIGHTEN
LOOSEN
LOOSEN
SHROUD
SHROUD
SHROUD
REACT BETWEEN THESE POINTS
4/20