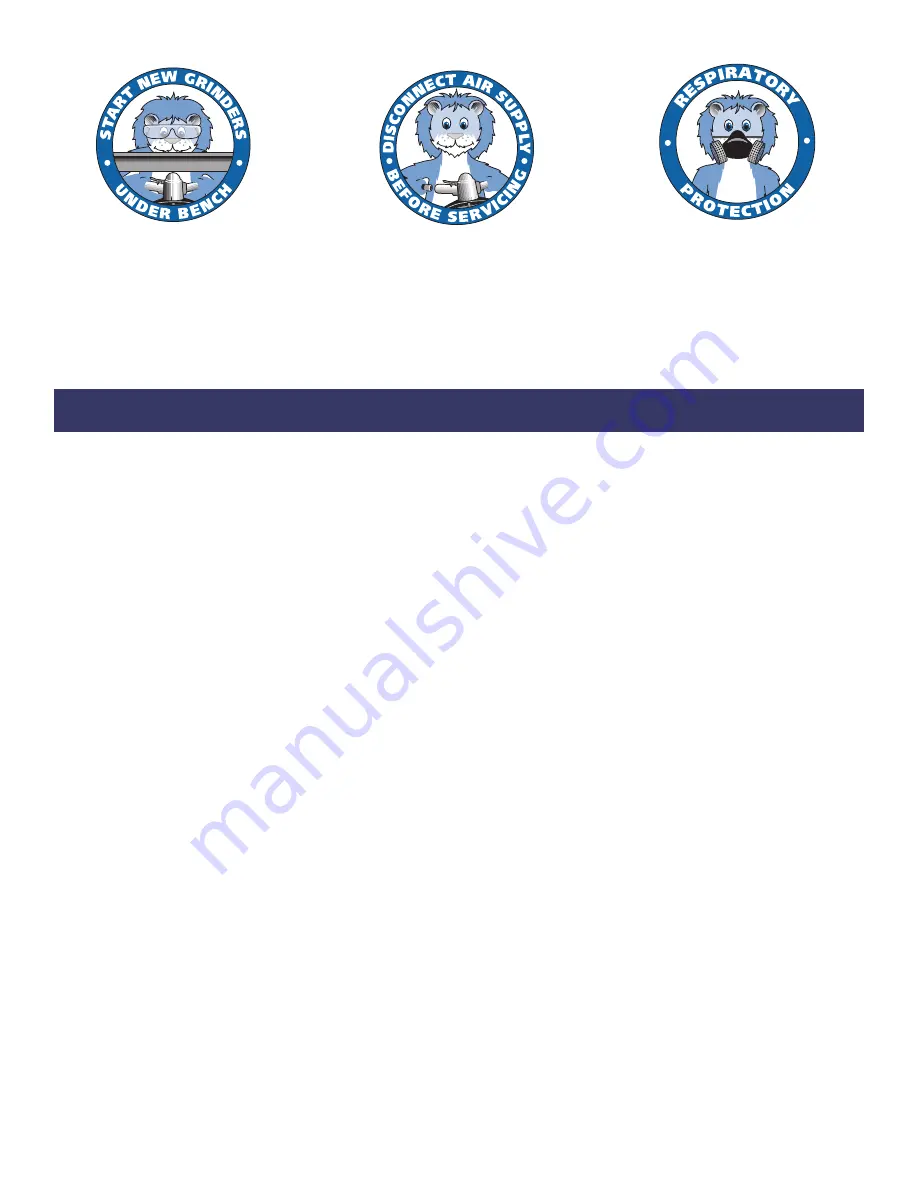
Proper mounting of grinding
wheels and inserted tooling
is crucial to safe operation
and efficient working condi-
tions. Ensure the exhaust
air is directed away from
bystanders.
Disconnect the tool from the air
supply before doing any service.
This prevents accidental start-ups.
Do not disassemble or adjust the
governor. The governor is guaran-
teed for the life of the tool, if not
abused.
The safety procedures for operating air tools are everyone’s responsibility. The following lists several
aspects of air tool safety that should be considered during operation. Please be aware of the these
aspects and report any unsafe practice you see to a supervisor or safety officer immediately.
1) Start any new wheel under a bench and away from bystanders. (Run for a minimum of one
minute.)
2) When starting a cold/new wheel, apply to the work slowly, allowing the wheel to warm gradually.
3) Support the work piece properly.
4) When cutting off, support the work piece so that a jamming of the wheel does not occur. (A Slot
shall remain constant or become wider during operation.)
5) If a jamming of the wheel does occur during a cutting off operation, shut the air supply off to the tool
and ease the wheel free. (Inspect the wheel for damage before continuing operation.)
6) Ensure that sparks from the process do not create a hazard to the eyes or will ignite the
environment.
7) Grinders shall not be used in potentially explosive atmospheres.
8) Pneumatically driven tools are not generally insulated from coming in contact with electrical
sources. Be sure to avoid contact with wires or other possible current carrying sources.
9) The operator must check that no bystanders are in the vicinity.
10) Remember that there is a running on after the throttle has been released.
11) If a grinder fitted with an abrasive wheel is dropped, the wheel must be thoroughly examined
before re-use.
12) Disconnect the tool from the air source before servicing and changing wheels.
13) Release the control device in case of interruption of air supply.
14) Always keep the tool in a clean, dry place when not in use.
15) Beware of loose hair and clothing so as not to become tangled or trapped during operation.
16) The inserted tool on heavy types of percussive non-rotary tools is exposed to heavy strains and
can after long periods of use break due to fatigue.
17) Unexpected tool movement or breakage of inserted tooling may cause injuries to lower limbs.
18) Unsuitable postures may not allow counteracting of normal or unexpected movement of a power
tool. (A working position shall be adopted which remains stable in the event of a break up of inserted
tooling.)
19) Do not hold the tool near the body when operating.
20) Keep a firm grip on the tool body during operation.
Safety in Operation
Airborne particulate
resulting from the
grinding process can
cause hazards. Wear
appropriate protective
equipment.
Summary of Contents for 467BRA1
Page 4: ...Maintenance...