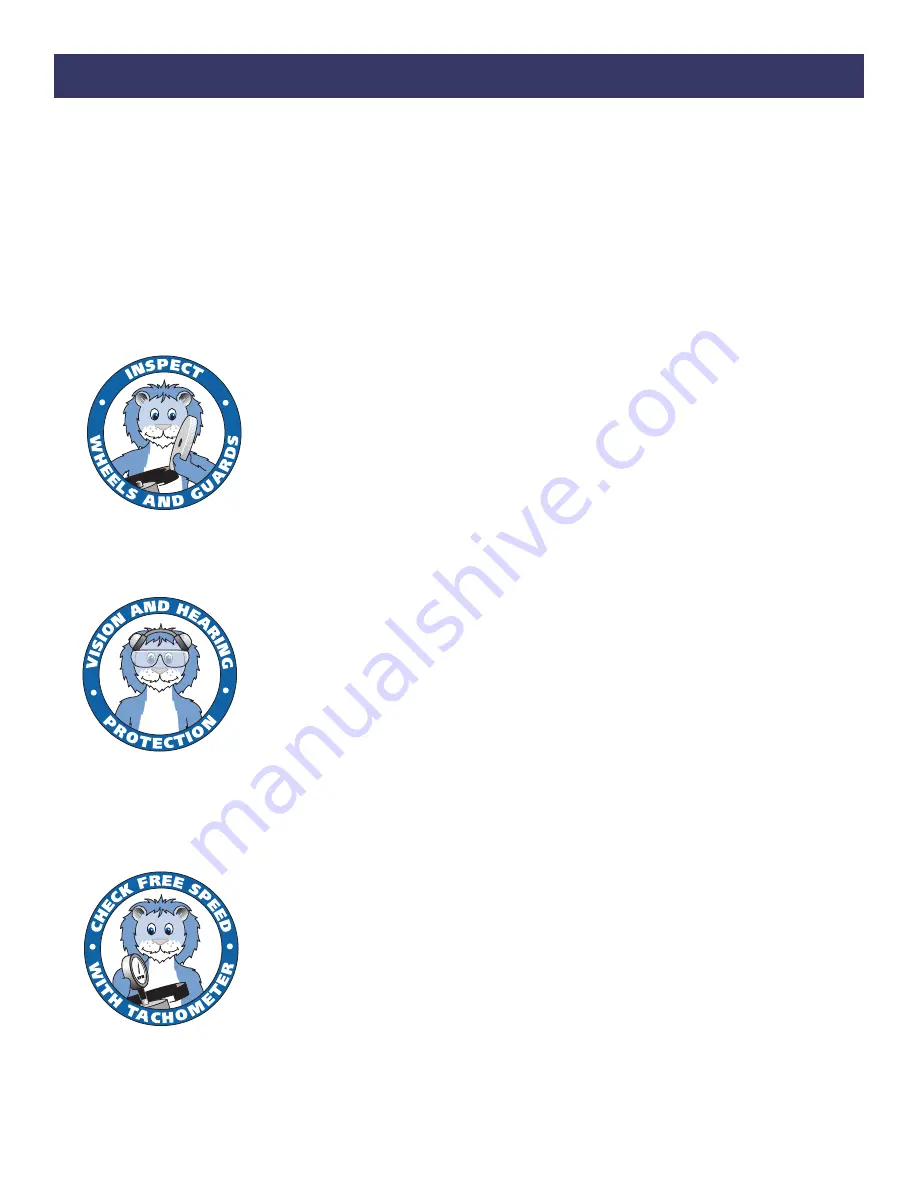
This is meant to highlight sections of safety standards published by the American National Standards
Institute and the Occupational Safety and Health Administration. This is not meant to replace those
standards but only highlight certain areas.
When care is taken to ensure that the right tool is operated properly, and safety and maintenance
procedures are followed, accidents can be avoided. Read and follow all instructions and directions.
Comply with all rules governing the use of power tools, personal protective equipment and equipment
guards.
Remember - machines, attachments and accessories must be used only for the purpose for which
they were designed. Safety reasons and product liability prohibit any modifications to tools. Any
attachments or accessories must be agreed to in advance with an authorized technical representative
of T.C. Service Co.
Operators Instructions and Safety Precautions
The grinding equipment must be approved for the rated speed of the
machine. The rated speed, marked on the machine, should not be
exceeded. Be sure to learn the proper handling and storage of abrasive
wheels and inserted tooling.
Inspect the wheel guard for any signs of wear and that it is properly
mounted to the tool. Any guard showing signs of wear such as bends,
chips, nicks, or cracks should be replaced.
Always wear eye and hearing protection, and when necessary, other
personal protective equipment such as gloves, an apron, and helmet.
Additional information on eye protection is available in the following
national regulatory standards.
1) Federal OSHA Regulations 29 CFR, Section 1910.133 (Eye and
Face Protection)
2) ANSI Z87.1 (Occupational and Educational Eye and Face Protection)
Check hose size and air pressure. The air pressure at the tool shall not
exceed 90 psi (6.2 bar). All hoses should be inspected regularly and
kept away from heat, oil and sharp edges. Be sure the tool is secured to
the air hose.
Measure the speed of grinders every 20 hours of actual use or once per
week, whichever comes first.
Measure speed of all types of grinders after maintenance or repair,
whenever a grinder is issued from the tool crib and at each wheel
change. Several readings should be taken.
This form of inspection should be made with the grinding wheel removed.
Summary of Contents for 467BRA1
Page 4: ...Maintenance...