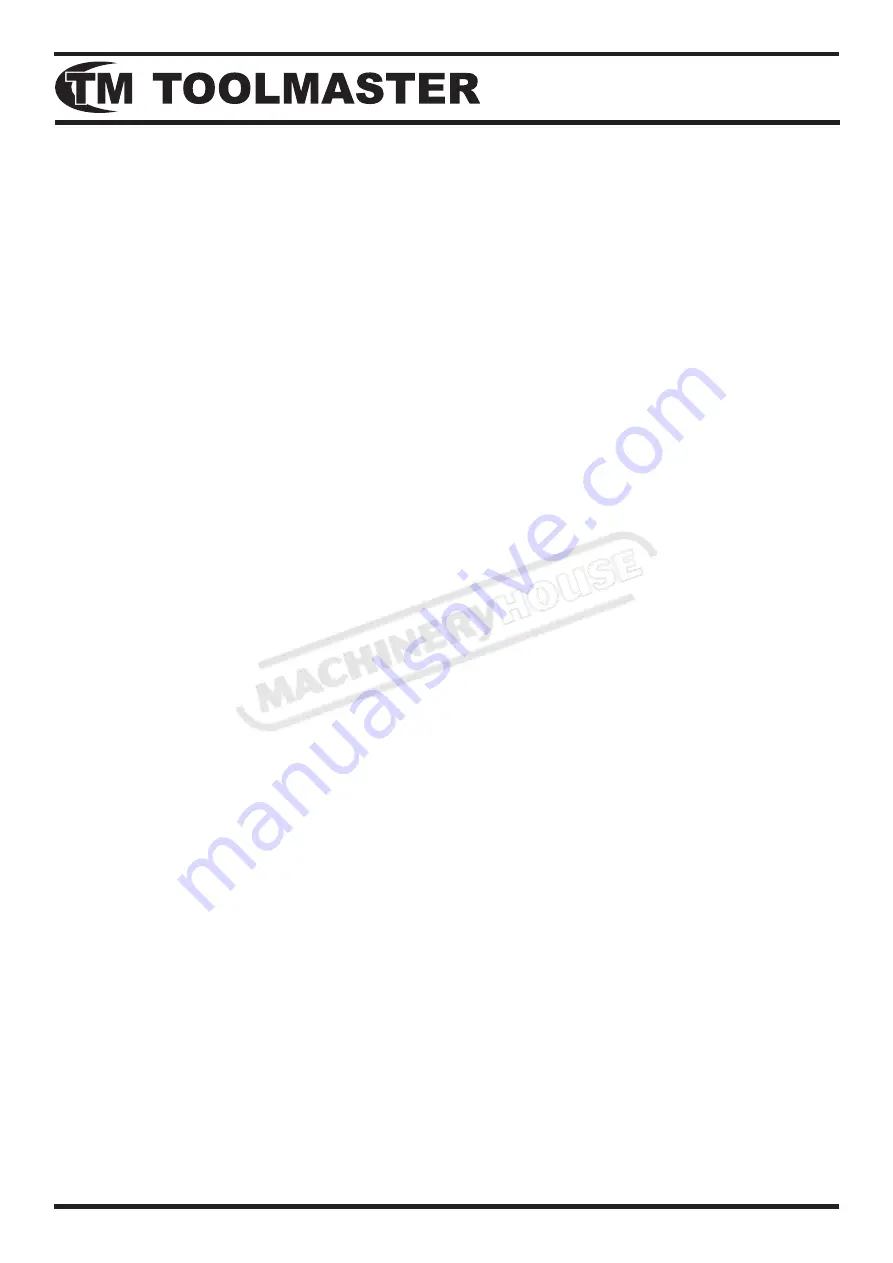
Nomenclature of Controls
The details below are used in most of the procedures listed in this manual, unless otherwise stat-
ed.
D
Wheel dressing attachment
A
Spring collet clamping quill
T1
Cross slide clamping lever
S2
Vertical swivel mount setting scale
T2
Vertical swivel mount clamping lever
T3
Horizontal swivel mount clamping lever
T4
Tubular guide clamping lever
F
Horizontal swivel mount index drum
T7
Clamping lever for adjustment along tubular guide
H
Index head bracket fine adjustment screw
G
Adjustable stop screw
T5
Index head slide clamping lever
C
Cutter lip aligning gauge
C1
P
S
Cross slide vernier scale for off-center radii
Spring collet index pin
Index head slide
S5
Index head slide fine adjustment set screw
S1
Index head slide fine adjustment screw
Q
Cross slide
T6
Index durm F clamping lever
B1
Collet sleeve
U2
Screw
A1
Stop plate for 90 degree
U3
Screw for Al
N4
Index drum
N5
Ring nut
E
Index ring bearing sleeve
M3
Nut for index sleeve
R7
Slotted disc
A3
Adjusting eccentric pin
M4
Nut
Summary of Contents for TM-U3
Page 1: ...INSTRUCTION MANUAL TM U3 Universal D BIT Grinder 240V 1 4HP G1975...
Page 10: ......
Page 12: ......
Page 14: ......
Page 16: ......
Page 18: ......
Page 20: ......
Page 25: ...12mm Collet This slot sets the travel Location pin0...
Page 30: ...SPARE PARTS...
Page 31: ......
Page 32: ......
Page 33: ......