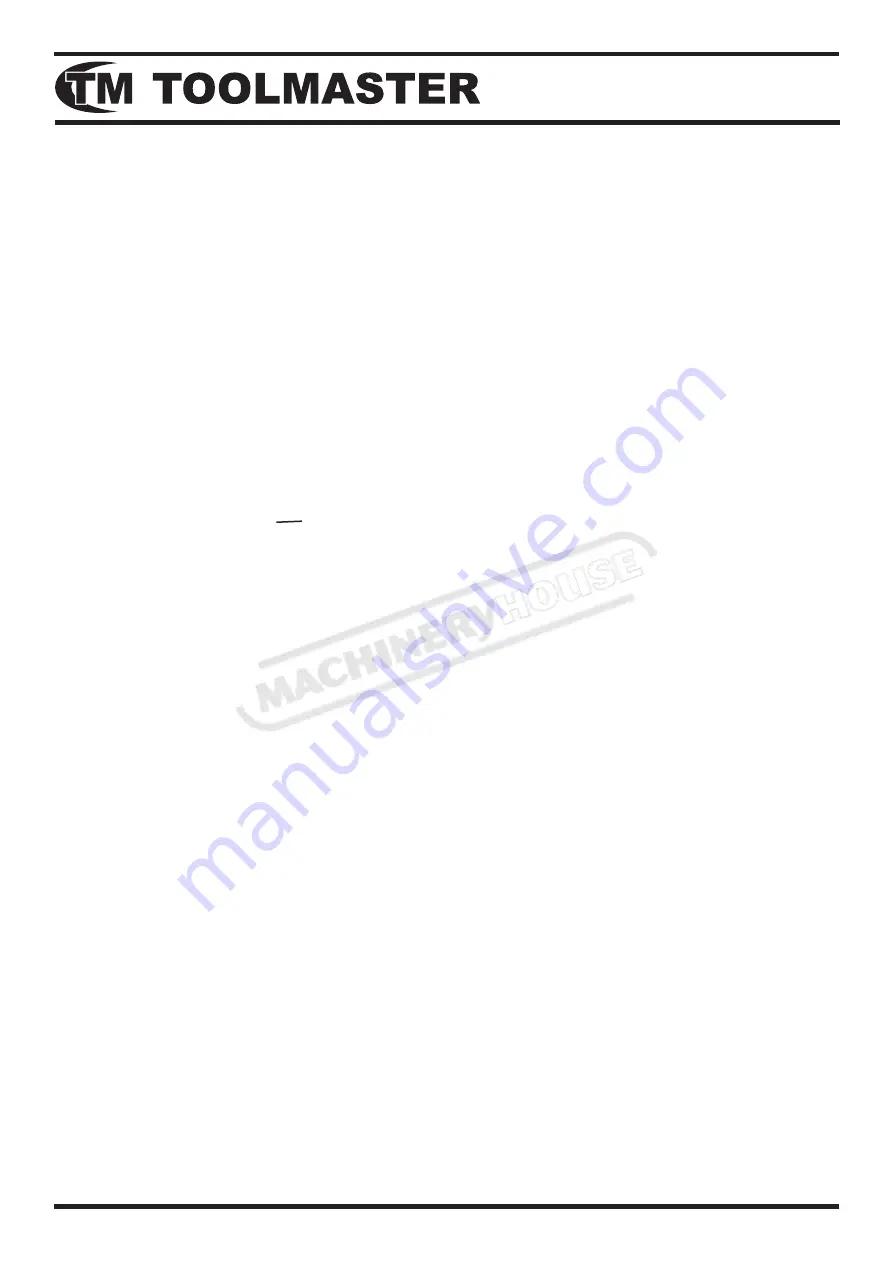
Circular Grinding of -Cutters
Grinding the Back Angle of End Cutting Edges
Cutter profiles having either on-center or-off-center radii are derived from cylindrical single lip cutters
having a straight end cutting edge by rounding off the corner as shown in Fig.1(No. 2 and 3 profiles).
In rounded cutters of this type the back rake angle of the side cutting edge Is the same as that of the
end cutting edge.
For this reason it is necessary, :during grinding the end rake angle, that the work fixture is set at the side
rake angle by means of setting scale S2. If the end cutting edge is ground immediately after grinding
the side sutting edge, it will not be necessary to re-set the work fixture and to re-align the cutting lip by
means of gauge C.
Setup Operations
1.
Engage index pin P into short-slot; and bring the white dot Into window O.
2.
a.
No. 2 Profile
: Release clamping lever Ti and rotate knurled knob S4 to set cross slide by
means of vernier scale C1 for desires radius (to the right). Tingten the clamping lever Ti,(see
Fig. 2) as the radiused corner is required to be tangent to the cutter diameter, the amount
of off-set
“a” is a = D - r.
2
Example :
Given r =0.06” (1.5mm);
D=0.30”
(8mm)
a =0.15” (4mm) - 0.06”
(1.5mm) = 0.09” (2.5mm)
b.
No. 3 Profile
: The vernier scale Cl of the cross slide must be set zero (see Fig. 3).
3,
Rotate fine adjustment screw H to bring the side cutting edge of the cutter into light contact with
the face of the grinding whe.el. Caution ! Do not injure the land of the side cutting edge. Now
screw H must no longer be rotated.
Grinding the Back Rake Angle
4.
Swivel the index head through 90° (see Fg, 4). Depth of cut adjustment now is by index head
slide S1. The adjustment is by micromenter screw S6 of the index head slide with adjusment
screw S5 thghtened. The end of the cuuter is rounded by slowly swivelling the index head back
to its original position while the collet bearing is continously rotated back and forth between the
stops, the ratation being through 180° (see Fig. 5 and 6).
Prior to grinding, be sure to with draw the index head a slight amount by rotating screw S in
order to prevent overheating of the cutter by excessive stock removal. After each pass of the
grinding wheel the cutter is then feed toward the wheel by means of screw S.
In order to obtain a satisfactory cutting edge it is advisable, as a final operation, to swivel the
Index head through 90° with the cutter lip pointing vertically upward.
In cases where cutters given a No. 3 profile are intended for the machiring of hard steel which
requires a small back rake angie, it is good practice to flatten the curvature of the cutter by a
manual grinding operation as shown in Fig. 7.
Summary of Contents for TM-U3
Page 1: ...INSTRUCTION MANUAL TM U3 Universal D BIT Grinder 240V 1 4HP G1975...
Page 10: ......
Page 12: ......
Page 14: ......
Page 16: ......
Page 18: ......
Page 20: ......
Page 25: ...12mm Collet This slot sets the travel Location pin0...
Page 30: ...SPARE PARTS...
Page 31: ......
Page 32: ......
Page 33: ......