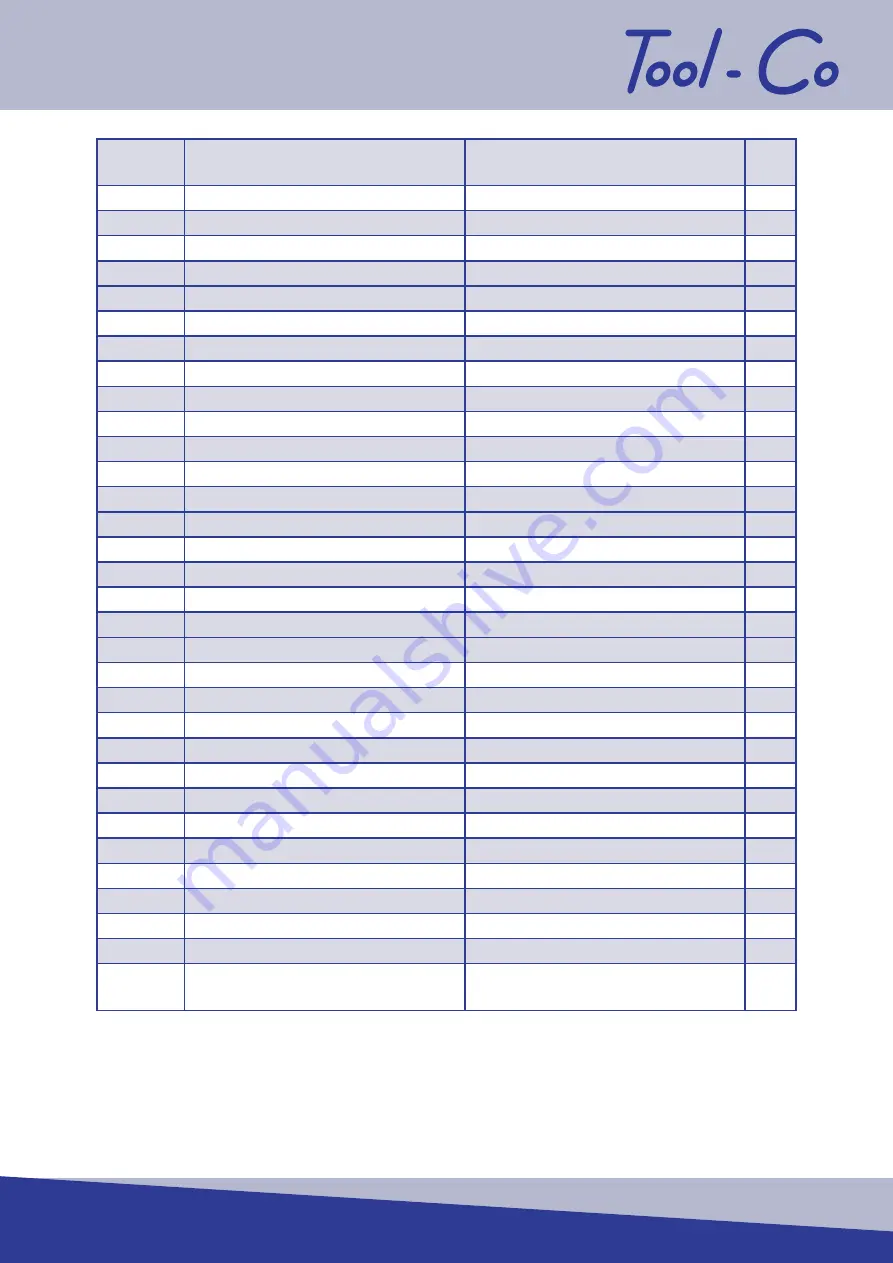
MANUAL
Pg.7
Position
Number
Part Number
Description
Qty
Req
41
BDG2501/0442
Spring Lock Washer
7
42
BDG2501/0443
Adjusting Shaft
2
43
BDG2501/0444
Wheel Shaft
2
44
BDG2501/0109
Grease Nipple (Zerk Fitting)
1
BDG2501/0445
Plain Washer
1
45
BDG2501/0446
Inner Hexagon Screw
2
46
BDG2501/0447
Eccentric Shaft
1
47
BDG2501/0448
Lift Lever
1
48
BDG2501/0266
Spacer Plate
1
49
BDG2501/0449
Spring Lock Washer
6
50
BDG2501/0450
Hexagon Bolt
2
51
BDG2501/0451
Pipe Clip
2
52
BDG2501/0452
Flexible Conduit Length 480mm
1
BDG2501/0453
Small Clip
2
53
BDG2501/0454
Vent-Pipe
1
54
BDG2501/0455
Big Plain Washer
3
55
BDG2501/0456
Water Spout
1
56
BDG2501/0457
Hexagon Head Bolt
4
BDG2501/0458
Plain Washer
4
57
BDG2501/0459
Shroud Strip Long
1
58
BDG2501/0460
Enclosure
1
59
BDG2501/0465
Key
1
60
BDG2501/0272
Flex Coupling
1
61
BDG2501/0461
Hexagon Head Bolt
2
62
BDG2501/0463
Hexagon Head Bolt
1
63
BDG2501/0466
Hexagon Nut
2
64
BDG2501/0267
Driving Sleeve
1
65
BDG2501/0462
Hexagon Head Bolt
2
66
BDG2501/0463
250mm Blank Plate
1
67
BDG2501/0277
Countersunk Cap Screw
2
68
BDG2501/0239
Dowel Disc
1
69
BDG2501/0290
M10 x 25
Countersunk Cap Screw
4
*NB “Qty Req” Indicates the quantity of parts required to make up a full set.*
**Parts are ordered individually.**