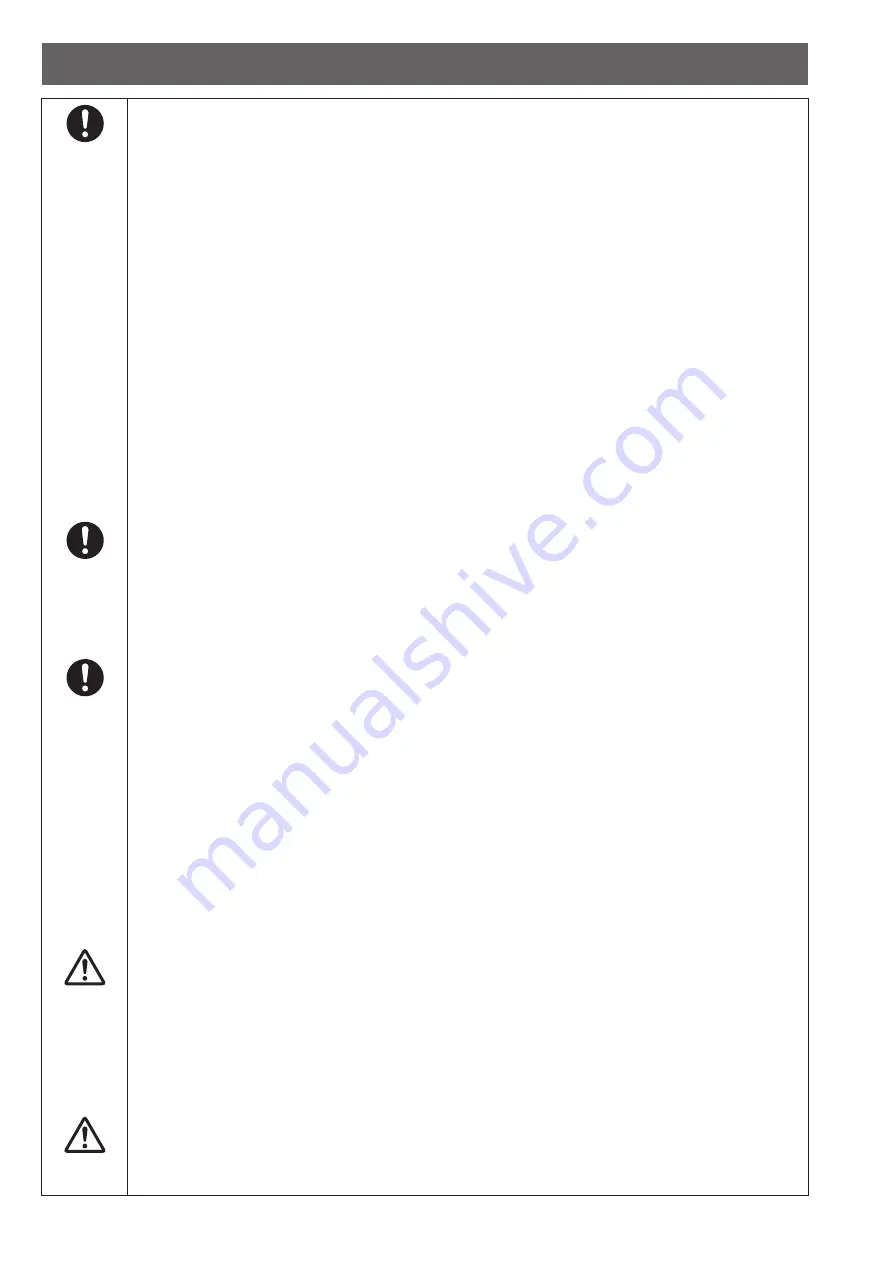
WARNING
CAUTION
2.4.6 Modification
This product should not be modified. Deterioration of durability or breakage of this product may pose a
danger to the environment.
2.4.7 External manual operation
Care must be taken for the following items at external manual operation.
①
For only double-acting type cylinders, a valve can be opened or closed manually by turning the
output shaft of the actuator with a spanner after the supply and exhaust pressures become the
same with the bypass valve (except Type T750).
Please note that, when the bypass valve is opened, the valve opening changes due to fluid
pressure.(Please refer to
4-4 Manual operation procedure for how to use the bypass valve.)
②
The manual operation torque may change abruptly depending on the valve opening, and you
may lose balance, resulting in falling. Manual operation should be performed while securing
safety with scaffolding, space, etc.
③
In the case of Type T750, large operating force is required and operation with small tools is
dangerous. Thus external manual operation should not be performed with a spanner or a
monkey wrench. Please use a manual gear for the operation.
④
For single-acting type cylinders, manual opening/closing operation should not be performed with a
spanner, a monkey wrench, or a manual lever for double-acting type cylinders (hereinafter "dedicated
lever"). If the output shaft is turned with a spanner, a monkey wrench, or the dedicated lever, the shaft is
rotated backwards by the spring force, which is dangerous. Please use the manual screw handle.
⑤
The spanner, monkey wrench, or special lever used at manual operation must be removed at comple-
tion of the operation. In case of automatic operation with them mounted, the spanner, monkey wrench,
or special lever may come off and fall out, which may cause personal injuries or machine damage.
⑥
In the case of a unit with a manual gear, before switching operation to automatic operation
after manual operation, check that the manual gear is at the position of automatic operation
and the bypass valve is closed. (They are not returned automatically.)
2.4.8 Others
①
If air supply is stopped for a long period of time after compressed air, etc. is supplied to this
product, the valve opening position may not be kept.
②
When operation is restarted after a long downtime (5 days or more), operation time may be
longer than usual due to increase in grease viscosity or valve resistance, etc.
2.5.1 Residual pressure
Even after supply of compressed air, etc. to this product is stopped, compressed air may gush out
or unexpected operation may occur due to residual pressure in the cylinder. Installation work and
maintenance should be performed after removing residual pressure from the cylinder.
2.5.2 Maintenance and inspection of this product
Maintenance and inspection should be performed according to
5-1 Disassembly procedure in this
manual. At maintenance and inspection of this product, inspection should be made while paying
attention to the following items.
①
For single-acting type cylinders, the cover may fall out due to the force of the internal spring
even if compressed air, etc. is not supplied, which may cause injury or damage.
②
Bolts should not be loosened, while compressed air, etc. are supplied, or this product or the
valve can be operated. Compressed air may gush out or unexpected operation may occur.
2.5.3 Daily check
Daily check including the following items on this product should be performed.
①
Water accumulated in the filter regulator etc. should be drained from the drain exhaust port.
②
During operation of this product, visual check and noise check should be performed from a
safe location. Inspection should be made on defective appearance, such as looseness of the
bolts, abnormal noise during operation, rattling, air leakage to the outside, air leakage from
exhaust vents and piping joints, etc.
③
If compressed air, etc. is supplied even if operation of this product is stopped, inspection
should be made on looseness of the bolts, air leakage to the outside, and air leakage from
exhaust vents and piping joints.
2-5 Maintenance
2.4.1 Operating air
The following items should be checked on operating air of this product.
1) Use clean operating air to operate this product.
2) It should be checked that compressed air, etc. supplied to this product should be within the range
between 0.4 MPa and 0.7 MPa.
3) Supplied air should be filtered with an air filter etc. to remove foreign substances. The filter should
be of 40 µm or finer mesh.
4) Supplied air should be dehumidified with an air dryer, etc. (dew-point temperature at atmospheric
barometric pressure is -15°C or lower) to remove moisture from the air.
5) Compressed air, etc. should be kept free from the following to prevent defective or abnormal
operation of the unit.
•
Chemicals, synthetic oils with organic solvent base, corrosive gas, deteriorated compressor oil
6) Attachments (solenoid valve, regulator, filter, pneumatic line size, joint, etc.) should be selected with
consideration of pressure loss so that the air pressure is within the range of the specified pressure
at the air inlet port of this product. Otherwise the opening and closing times may slow down.
7) In case of lack of supply of compressed air, etc. to this product, intermittent operation of the pistons
occur, or the valve is stuck. Care should be taken to avoid lack of air supply amount and air supply
pressure. When the pneumatic pipeline is 5 m or more, take measures, such as use of a large-
diameter pipeline, etc.
8) Cylinder capacity of a pneumatic actuator varies largely subject to type of actuator. Please select
the suitable air compressor capacity. Please refer to
3-4 Air consumption.
2.4.2 Supply pressure adjustment
Piping should be designed so that suitable compressed air amount and pressure are supplied to this product.
Insufficient air supply amount or air supply pressure may affect opening/closing operation of the valve.
In cases of pneumatic devices in which the pneumatic pipeline inlet of this product or the end of the plant
pipeline is connected with a long pipeline, air supply amount and air supply pressure may be insufficient
for this product due to loss at pipelines. An auxiliary air tank should be installed, etc. as needed.
2.4.3 Operation check
When this product is purchased separately, operation check should be performed with the following
procedure.
①
It should be checked that there is no flaw in the appearance, damage or loss of parts.
②
This product should be checked separately for proper operation.
③
After connecting to the valve, adjust the valve opening. (Please refer to
4-3 Adjustment of valve
position for details.)
④
Valve opening/closing operation should be checked.
When this product integrated with a valve (hereinafter "finished product") is purchased, operation check
should be performed with the following procedure.
①
It should be checked that there is no flaw in the appearance, damage or loss of parts.
②
It should be checked that pipelines for compressed air and electric signals are connected.
③
It should be checked that there is no air leakage from pipeline connecting sections and this product.
④
Valve opening/closing operation should be checked.
2.4.4 Valve opening adjustment
Valve opening should be adjusted while paying attention to the following points.
①
When finished products are purchased, the stopper bolts at the closing side should not be
loosened. If the stopper bolts at the closing side are loosened, the valve full closing position
changes, and valve seat leakage may occur.
②
Before adjustment, compressed air, etc. should be discharged from this product. If there is any
residual pressure due to compressed air, the stopper bolts may fall out.
③
After adjustment, it should be checked that there is no air leakage from the stopper bolts.
2.4.5 Opening and closing time
If the opening and closing time is shorter than the minimum time of the product specifications, durability
of this product may be deteriorated.
2-4 Use and adjustment
CAUTION
CAUTION
CAUTION
7
8