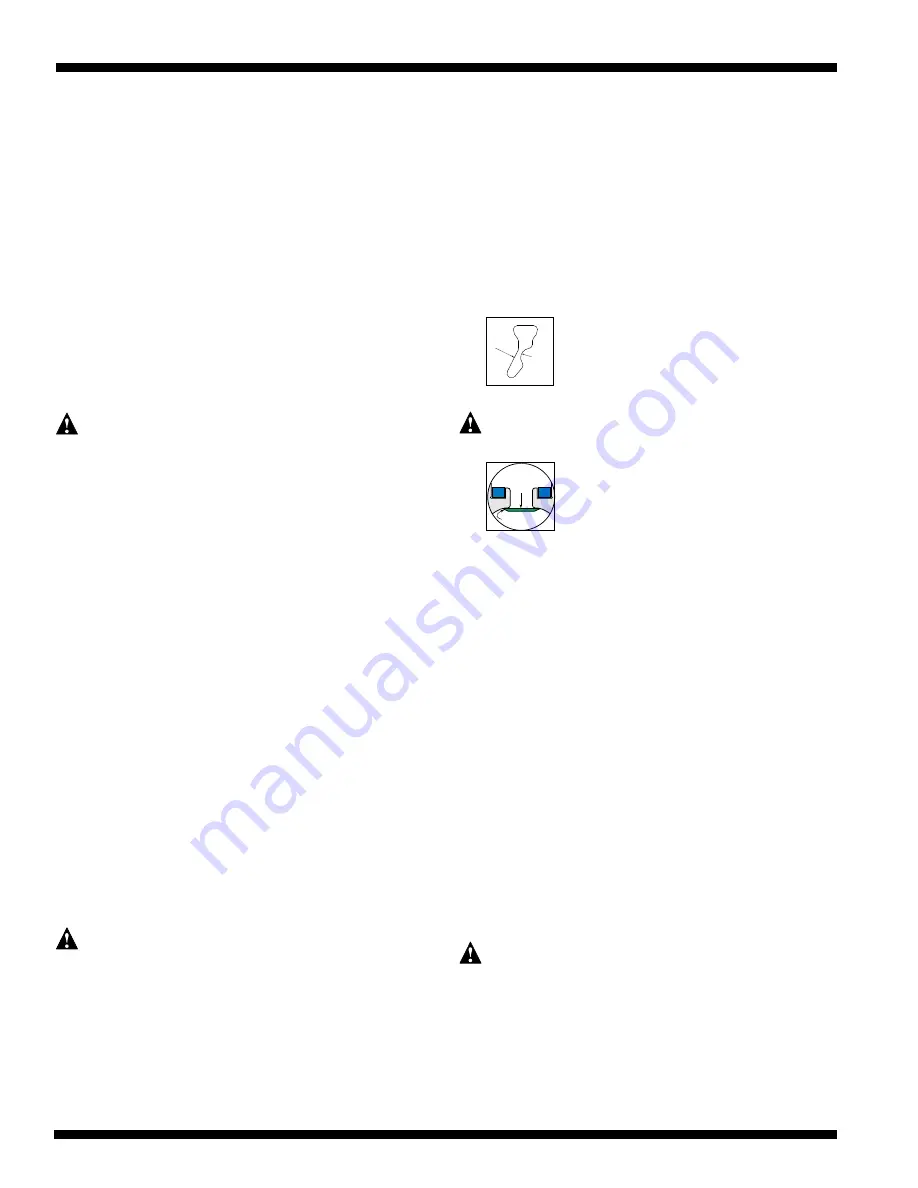
Tolomatic • URL: http://www.tolomatic.com • Email: [email protected] • Fax: (763) 478-8080 • Toll Free: 1-800-328-2174
2 – Instructions
MXP25P
Parts Sheet #8100-4106_06_MXP25Pps
CYLINDER DISASSEMBLY INSTRUCTIONS
Begin with a clean work area. Make sure all replacement parts are available
and have no visual damage or defects. The following tools and materials are
recommended for proper disassembly and assembly. (Exact wrench sizes will
vary depending on cylinder size.)
•
Allen wrench set (std. and metric)
•
Small Straight edge screwdriver
•
Socket wrench & socket set
•
Needle nose pliers
•
RheoGel TEK664 grease
•
Tin snips
For best actuator performance it is recommended that the following instruc-
tions be read and followed carefully.
1. REMOVE BAND CYLINDER FROM MACHINERY
Remove all mounting hardware and air connections, if present, from the
Cylinder Heads (15) and/or Carrier (24).
2. REMOVE CARRIER FROM CYLINDER
Remove Screws (28) from Carrier (24). Slowly lift up the Carrier (24), and
remove it from the cylinder.
CAUTION:
Contaminating the Bearing Block (29b) will hinder the opera-
tion of the cylinder.
Do not Remove the Bearing Blocks from the
Rails.
If the Bearing Blocks need to be replaced so will the Bearing Rail.
Remove Screws (26) and Carrier Adjustment Plates (25) from the cylinder.
3. REMOVE BEARING BLOCKS AND BEARING RAIL (OPTIONAL)
The MX Bearing System is designed to provide maximum life. Should the
Bearing Blocks need replacement, the Bearing Rail will need to be replaced
as well. Bearing Blocks (29b) and Bearing Rail (29a) must remain together.
If the cylinder stroke requires two Bearing Rails to be mounted, the
cylinder will need to be sent to the factory. It is critical that the two
Rails are aligned properly. This requires special fixtures and cannot be
done in the field.
To remove both the Bearing Blocks and Bearing Rail, slide each
Bearing Block off one at a time and place in a clean area. Next remove
Screws (31) from the Bearing Rail (29a). Lift up on the Rail and place
in a clean area.
4. LOOSEN BANDS
Loosen Screw (16) from Cylinder Head (15) approx. 4 to 5 turns, but do
not remove the Screw. Tap the Screw into the Head to disengage the
Band Clamp (17). Repeat the process for the other Head.
5. REMOVE HEADS
Remove the four Head Screws (20) to free each Cylinder Head (15).
Remove each head by rocking it up and down until the Head is free from
the Cylinder Tube.
DO NOT TWIST!
Remove the small Band Tab (23)
mounted over the top of the Dust Band (3). Remove the O-Ring (19) from
both Heads with a small screwdriver.
6. REMOVE DUST BAND
Remove End Caps (7) from both ends of the Piston Bracket (5) by
removing Screws (9). To remove the Dust Band (3), lift one end and pull
the Band thru the Piston Bracket. The Band is magnetically retained so
some resistance will be present when removing.
7. REMOVE SEAL BAND
CAUTION:
Sealing Band edges are sharp. Grasp the top and bottom of
the Band when removing, not the edges.
Slide Piston Bracket (5) out of the Tube, then remove the Sealing
Band (4). Keep the Sealing Band available to assist in the reassembly
of the new Sealing Band. A 6-inch piece of Band is also included in the
repair kit for use during reassembly.
8. DISASSEMBLE PISTON BRACKET
Remove Wipers (10) from the Piston Bracket (5). With a small straight
edge screwdriver, remove the U-Cups (14) from both Pistons (6).
Remove the Cushion Seals (13) from the Piston. Remove the Pistons (6)
by inserting the screwdriver under the Piston side tabs until the side
retaining tabs are disengaged from the Piston Bracket (5). With a small
screwdriver, remove the Band Ramps (8) by disengaging the side retain-
ing tabs from the Piston Bracket (5). Keep the Piston Bracket (5) and
Pistons (6) separated for reassembly.
CYLINDER ASSEMBLY INSTRUCTIONS
1. CLEAN AND LUBRICATE
Thoroughly clean all components, particularly the Tube Bore, Tube Slot
and Bands. Thoroughly lubricate the bore of the Tube with a thin, uni-
form layer of RheoGel TEK664 grease.
2. ASSEMBLY OF PISTON BRACKET
With the Piston Bracket (5) in hand, install the Band Ramps (8) so the
smaller ends are on the bottom. Install the Pistons (6) with the ramp
facing up. Slide the Piston onto the Piston Bracket. It should snap easily
into place. Install new lubricated U-Cups (14) (seal lips facing out), and
Cushion Seals (13) (small end facing out). Slide new
Wipers (10) into the groove on the Piston Bracket (5),
flat side of Wiper faces out, Wiper groove on inside (see
illustration). Trim to edge of Piston Bracket (5) and flare
Wiper (10) edges outward.
3. INSTALL INNER SEALING BAND
CAUTION:
Metal edges of Sealing Band are sharp. Exercise caution to
avoid injury to yourself while installing. Handle Sealing Band with care.
Do not damage edges while handling.
Insert Sealing Band (4) into Cylinder Tube (1) by laying
the Band out along the length of the actuator and pass-
ing it sideways through slot in Tube. With flat side facing
up (ground side facing down), position the Band so a
Piston Bracket’s length of Band extends from the Tube at
one end.
4. INSTALL PISTON ASSEMBLY
Place generous amounts of grease around bore of Tube (1) on both
ends and fill indentations on both sides of Piston Bracket (5) with
grease. Using 6-inch length of Seal Band included with repair kit, or a
short length of the old Seal Band, slightly kink the Band upwards, one
inch (25mm) from the end. Insert into slot between the Band Ramp (8)
and Piston (6) on the Piston Bracket, and stop against opposite side of
the Piston. Feed the extended Sealing Band (4) through the opposite
end of the Piston Bracket (5) and up the short length of inserted Band.
Once the Sealing Band (4) is through the Piston Bracket (5), remove the
short length of Band material and discard.
Grasp the Piston Bracket (5) while holding the Wipers (10) in place with
your fingers. Flare the Wiper edges out while inserting the Piston Bracket
partway into the Tube. Do not force the Piston Bracket. Place a finger
over the opposite end of the Piston Bracket to keep the Wipers in place,
while pushing the remainder of Piston Bracket into the Tube. If the Piston
Assembly experiences resistance, use a small screw driver to press in
on the ends of the Band Ramps (8) where it contacts the Tube (1). With
the Piston Bracket in place, slide the length of the greased Tube until the
end of the Piston just extends out the Tube. Wipe off the excess grease
from the Piston end.
NOTE: If Tube and Piston Assembly were greased properly, excess
grease should be present as the Piston exits end of Tube. If this is not
the case, more grease will need to be added.
5. INSTALL ONE HEAD
CAUTION:
Twisting the Head during installation may cut the O-Rings
resulting in excessive leakage during operation.
Install new lubricated O-Rings (19) onto each Head (15). Position the
Seal Band (4) leaving .490" (12.4 mm) of Band protruding from the end
of the Tube. Install Head (15) into Tube (1) holding Screw (16) in place.
Position the Seal Band (4) on the bottom side of the Band Clamp (17).
Use a slight up and down rocking motion (not side-to-side or twisting)
to insert the first Head into Tube. The Head should be flush with the end
of the Tube after installation. Apply RheoGel TEK664 to threads of Head
Screw (20) and install into Head. Torque Screws to 70 – 80 in-lbs (8 – 9
N-m).
FLAT
SIDE
GROUND SIDE
FLAT SIDE
OF WIPER
FACES OUT
GROOVE
TO INSIDE